倒裝芯片工藝挑戰SMT組裝
原作者:不詳
1 引言
20世紀90年代以來,移動電話、個人數字助手(PDA)、數碼相機等消費類電子產品的體積越來越小,工作速度越來越快,智能化程度越來越高。這些日新月異的變化為電子封裝與組裝技術帶來了許多挑戰和機遇。材料、設備性能與工藝控制能力的改進使越來越多的EMS公司可以跳過標準的表面安裝技術(SMT)直接進入先進的組裝技術領域,包括倒裝芯片等。由于越來越多的產品設計需要不斷減小體積,提高工作速度,增加功能,因此可以預計,倒裝芯片技術的應用范圍將不斷擴大,最終會取代SMT當前的地位,成為一種標準的封裝技術。
多年以來,半導體封裝公司與EMS公司一直在攜手合作,在發揮各自特長的同時又參與對方領域的技術業務,力爭使自己的技術能力更加完善和全面。在半導體工業需求日益增加的環境下,越來越多的公司開始提供"完整的解決方案"。這種趨同性是人們所期望看到的,但同時雙方都會面臨一定的挑戰。
例如,以倒裝芯片BGA或系統封裝模塊為例,隨著采用先進技術制造而成的產品的類型由板組裝方式向元件組裝方式的轉變,以往似乎不太重要的諸多因素都將發揮至關重要的作用。互連應力不同了,材料的不兼容性增加了,工藝流程也不一樣了。不論你的新產品類型是否需要倒裝芯片技術,不論你是否認為采用倒裝芯片的時間合適與否,理解倒裝芯片技術所存在的諸多挑戰都是十分重要的。
2 倒裝芯片技術
"倒裝芯片技術",這一名詞包括許多不同的方法。每一種方法都有許多不同之處,且應用也有所不同。例如,就電路板或基板類型的選擇而言,無論它是有機材料、陶瓷材料還是柔性材料,都決定著組裝材料(凸點類型、焊劑、底部填充材料等)的選擇,而且在一定程度上還決定著所需設備的選擇。在目前的情況下,每個公司都必須決定采用哪一種技術,選購哪一類工藝部件,為滿足未來產品的需要進行哪一些研究與開發,同時還需要考慮如何將資本投資和運作成本降至最低額。
在SMT環境中最常用、最合適的方法是焊膏倒裝芯片組裝工藝。即使如此,為了確保可制造性、可靠性并達到成本目標也應考慮到該技術的許多變化。目前廣泛采用的倒裝芯片方法主要是根據互連結構而確定的。如,柔順凸點技術的實現要采用鍍金的導電聚合物或聚合物/彈性體凸點。
焊柱凸點技術的實現要采用焊球鍵合(主要采用金線)或電鍍技術,然后用導電的各向同性粘接劑完成組裝。工藝中不能對集成電路(1C)鍵合點造成影響。在這種情況下就需要使用各向異性導電膜。焊膏凸點技術包括蒸發、電鍍、化學鍍、模版印刷、噴注等。因此,互連的選擇就決定了所需的鍵合技術。通常,可選擇的鍵合技術主要包括:再流鍵合、熱超聲鍵合、熱壓鍵合和瞬態液相鍵合等。
上述各種技術都有利也有弊,通常都受應用而驅動。但就標準SMT工藝使用而言,焊膏倒裝芯片組裝工藝是最常見的,且已證明完全適合SMT。
3 焊膏倒裝芯片組裝技術
傳統的焊膏倒裝芯片組裝工藝流程包括:涂焊劑、布芯片、焊膏再流與底部填充等。但為了桷保成功而可靠的倒裝芯片組裝還必須注意其它事項。通常,成功始于設計。
首要的設計考慮包括焊料凸點和下凸點結構,其目的是將互連和IC鍵合點上的應力降至最低。如果互連設計適當的話,已知的可靠性模型可預測出焊膏上將要出現的問題。對IC鍵合點結構、鈍化、聚酰亞胺開口以及下凸點治金(UBM)結構進行合理的設計即可實現這一目的。鈍化開口的設計必須達到下列目的:降低電流密度;減小集中應力的面積;提高電遷移的壽命;最大限度地增大UBM和焊料凸點的斷面面積。
凸點位置布局是另一項設計考慮,焊料凸點的位置盡可能的對稱,識別定向特征(去掉一個邊角凸點)是個例外。布局設計還必須考慮順流切片操作不會受到任何干擾。在IC的有源區上布置焊料凸點還取決于IC電路的電性能和靈敏度。除此之外,還有其它的IC設計考慮,但晶片凸點制作公司擁有專門的IC焊點與布局設計準則來保證凸點的可靠性,從而可確保互連的可靠性。
主要的板設計考慮包括金屬焊點的尺寸與相關的焊料掩模開口。首先,必須最大限度地增加板焊點位置的潤濕面積以形成較強的結合點。但必須注意板上潤濕面積的大小應與UBM的直徑相匹配。這有助于形成對稱的互連,并可避免互連一端的應力高于另一端,即應力不均衡問題。實際上,設計時,通常會采用使板的焊點直徑略大于UBM直徑的方法,目的是將接合應力集中在電路板一端,而不是較弱的IC上。對焊膏掩模開口進行適當的設計可以控制板焊點位置上的潤濕面積。
既可采用焊膏掩模設計也可采用無焊膏掩模設計,但將這兩種方法結合起來的設計是最可靠的設計手段。在相關的電路板圖形上使用矩形開口并將焊膏掩模的清晰度也考慮在內即可設計出恰當的板焊點位置。如果設計不合理,一旦組裝環境發生變化或機械因數有所改變,IC就會出現焊膏疲勞斷裂。采用底部填料的方法的確能夠極大地提高倒裝芯片元件互連的可靠性,但如果不嚴格遵循設計準則的話還是不可避免地會產生同樣的失效機理。
4 晶片的凸點制作/切片
焊料凸點的作用是充當IC與電路板之間的機械互連、電互連、有時還起到熱互連的作用。在典型的倒裝芯片器件中,互連由UBM和焊料凸點本身構成。UBM搭接在晶片鈍化層上,以保護電路不受外部環境的影響。實際上,UBM充當著凸點的基底。它具有極佳的與晶片金屬和鈍化材料的粘接性能,充當著焊膏與IC鍵合金屬之間的焊膏擴散層,同時還為焊膏提供氧化勢壘潤濕表面。UBM疊層對降低IC焊點下方的應力具有十分重要的作用。
如前所述,焊料凸點制作技術的種類很多。采用蒸發的方法需要在晶片表面上濺射勢壘金屬(采用掩模或用光刻作為輔助手段)形成UMB,然后蒸發Sn和Pb形成焊料。在隨后的工藝中對Sn和Pb焊料進行再流,形成球形凸點。這一技術非常適用于采用耐高溫陶瓷基板的含鉛量較高的凸點(相對易熔焊料凸點而言)。但對有機電路板上的SMT應用而言,IC上的高鉛焊料凸點還需要采用易熔焊料來形成互連。
低成本的凸點制作技術,如電鍍或模版印刷(與濺射或化學鍍UBM相結合)都是目前常用的制作工藝。這些工藝的凸點制作成本要比蒸發低一些,而且在電路上使用易熔焊料還可省去再將其放置到電路板上的那步工藝及其費用。目前生產的其它焊料合金包括無鉛焊料、高鉛焊料和低α焊料等。
對電鍍凸點工藝而言,UBM材料要濺射在整個晶片的表面上,然后淀積光刻膠,并用光刻的方法在IC鍵合點上形成開口。然后將焊接材料電鍍到晶片上并包含在光刻膠的開口中。其后將光刻膠剝離,并對曝光的UBM材料進行刻蝕,對晶片進行再流,形成最終的凸點。另一種常用的方法是將焊料模版印刷到帶圖形的UBM(濺射或電鍍)上,然后再流。
控制凸點的最終高度具有十分重要的作用。它可以保證較高的組裝成品率。用于監測凸點制作工藝的破壞性凸點切斷測試方法常常會使焊膏中產生失效模式,但絕不會對UBM或下面的IC焊點造成這樣的結果。
晶片切割常常被看作是后端組裝中的第一步。磨蝕金剛石刀片以60,000rpm的轉速進行切片。切割中要使用去離子水以提高切割的質量并延長刀片的壽命。目前,降低單個IC上的屑片缺陷是一項十分緊迫的任務。因為頂部的屑片有可能接近芯片的有源區,背面的屑片對倒裝芯片的可靠性極其不利。邊緣的斷裂,甚至是芯片區內的背面芯片在熱應力和機械應力的作用下常會擴展,導致器件的早期失效。
5 焊劑/拾裝/再流
完成晶片切割后,可將切分好的單個芯片留在晶片上,也可將其放置到華夫餅包裝容器、凝膠容器、Surftape或帶與軸封裝中。倒裝芯片布局設備必須具有處理帶凸點的芯片的能力。華夫餅容器適應于小批量需求,或用于免測芯片;帶與軸適用于SMT貼裝設備;送至貼裝設備的晶片較為普遍,且最適合大批量制造應用。
實際的倒裝芯片組裝工藝由分配焊劑開始。分配焊劑的方法有多種,包括浸液、擠涂分配、模版印刷、或噴涂等。每一種方法都有其優點和應用范圍。貼裝設備上通常要裝有焊劑或粘接膠浸潤組件。這種方法具備將焊劑固定到芯片凸點上的優點。
控制焊劑膜的高度和盤的旋轉速度對批量生產的可重復性十分必要。焊劑分配工藝必須精確控制焊劑的分配量與可重復性。模版印刷焊劑適用于大批量制造,但對逆流設備的要求較高。不管采用哪一種方法,在粘貼倒裝芯片器件時都必須考慮材料的特性和所用焊劑的兼容性。
完成焊劑分配工藝后就可以采用多頭高速元件拾裝系統或超高精度拾裝系統拾取芯片了。為了促進半導體后端制造與EMS組裝市場的結合,目前的拾裝設備,如西門子SiPlaceHF新型設備都具有較高的速度與精度。倒裝芯片與電路板對準由高精度攝像機完成。
拾裝工藝的關鍵參數包括元件的適當拾取、定位精度與可靠性、貼裝的力度大小、停留時間和成品率等。倒裝芯片拾裝精度通常要求在凸點節距的10%左右,以最大限度地減小平移偏移和旋轉偏移。許多公司已在不同板條件下對各種工藝參數進行了廣泛的研究和探討,包括芯片尺寸、凸點節距、凸點高度和每個芯片上的凸點數量等。
拾裝設備上所用的噴嘴類型是根據芯片尺寸與/或凸點引腳(全陣列與環形陣列)等因素而決定的。將分好的晶片中的芯片拾取,面朝下放好,貼到電路板上。如果噴嘴的硬度和一致性都正常的話就不會對凸點和芯片造成損壞。將芯片翻動,拾取,對準并貼裝。
為了避免已裝置好的芯片在再流工藝前發生移動,操作時應倍加小心。因此,再流工藝通常在直排的多級連續爐中采用對流、紅外加熱、或傳導加熱(強熱對流)進行。在任何一種情況下都必須嚴格控制爐內氣氛和溫度分布,以確保可靠的再流焊點。主要的影響參數包括液化、峰值溫度、斜坡速率、吸收時間、吸收溫度、冷卻速率與對流速率等。精確的分布(即,在芯片下放置熱電偶)具有十分重要的作用,因為這樣可以防止基板退化、焊膏不足和焊膏起球等現象。此外,焊劑的一致性、焊劑的活化以及均勻的熱傳遞都是十分關鍵的參數。
6 底部填充
焊膏再流工藝之后要使用底部填料以實現芯片與電路板的耦合,從而極大地提高互連的完整性與可靠性。最常用的技術就是在焊膏再流之后分配底部填料。但有一些應用也采用芯片粘貼之前分配不流動的底部填料或在電路板上印刷,并在焊膏再流期間進行固化。
要想順利地完成底部填料工藝就必須考慮一些重要的參數,如底部填充材料的特性與兼容性(適當地Tg、CTE和模件等)、分配量、分配形式、板的溫度與底部填充流動的機理等。利用毛細作用的傳統的底部填充流動主要取決于芯片的尺寸和外形、凸點的式樣、間隔大小、填充材料的黏度、芯片與板的表面張力、以及填充材料的潤濕角等。
針的尺寸、離芯片邊緣的分配距離、針距板的高度和分配的速度也是必須了解并加以控制的重要參數。此外,在填充工藝期間控制板的溫度可以提高毛細管的流動,同時還可避免先期凝膠。
要確保高可靠的倒裝芯片組裝就必須充分了解材料的流動特性,避免氣孔或分層(采用C模式掃描聲學顯微鏡可以看出)。濕氣與/或溫度循環會引起填充材料與芯片或基板的分層,而一旦產生分層就有可能造成高應力集中,并導致焊點的預先失效。
底部填充材料的固化工藝可在連續直排爐或間歇爐中完成。控制溫度的一致性、固化時間、以及爐內的氣氛條件,充分實現底部填料所具有的優點是十分重要的。
倒裝芯片的成功實現與使用包含諸多設計、工藝、設備與材料因素。只有對每一個因素都加以認真考慮和對待才能夠促進工藝和技術的不斷完善和進步,才能滿足應用領域對倒裝芯片技術產品不斷增長的需要。
- 倒裝芯片(16076)
- MT組裝(5778)
相關推薦
【華秋DFM】SMT組裝工藝流程的應用場景(多圖)

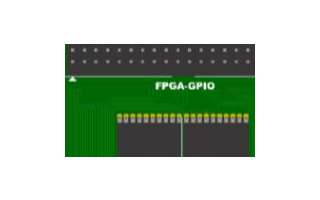
表面組裝技術(SMT)培訓綱要

淺談倒裝芯片封裝工藝

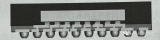
什么是倒裝芯片 倒裝芯片技術的優點 倒裝芯片封裝工藝流程

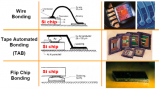
SMT組裝工藝流程的應用場景(多圖)

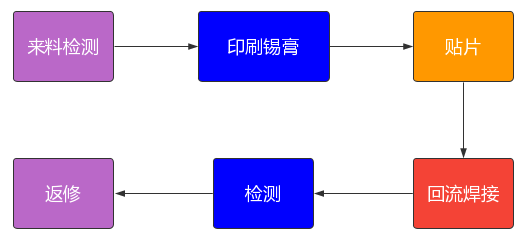
SMT工藝---簡介
SMT組裝工藝流程的應用場景
SMT組裝工藝流程的應用場景(多圖)
SMT優化系統的設計與實現
SMT基本工藝
SMT定義及工藝技術簡介
SMT最新技術之CSP及無鉛技術
SMT最新技術之CSP的基本特征
SMT焊接工藝解讀
SMT環境中的新技術介紹
SMT貼片工藝(雙面)
SMT貼片加工技術的組裝方式介紹
SMT貼片生產制造工藝
倒裝芯片與表面貼裝工藝
倒裝芯片和晶片級封裝技術及其應用
倒裝芯片應用的設計規則
倒裝芯片的特點和工藝流程
倒裝COB顯示屏
倒裝晶片的組裝基板的設計及制造
倒裝晶片的組裝的助焊劑工藝
倒裝晶片的組裝的回流焊接工藝
倒裝晶片的組裝工藝流程
倒裝晶片的定義
倒裝晶片的貼裝工藝控制
Flip-Chip倒裝焊芯片原理與優點
PCB拼版對SMT組裝的影響
【華秋干貨鋪】SMT組裝工藝流程的應用場景
【轉】SMT貼片加工的發展特點及工藝流程
啥?PCB拼版對SMT組裝有影響!
我們是否可能像搭積木一樣來組裝芯片呢?
最新SMT復雜技術
表面組裝技術簡述
表面組裝技術(SMT)培訓綱要

SMT倒裝芯片的非流動型底部填充劑工藝

SMT環境中倒裝芯片工藝與技術應用

倒裝芯片封裝的發展

芯片級封裝器件返修工藝

正裝、倒裝、垂直LED芯片結構的介紹及LED倒裝芯片的優點

LED倒裝晶片所需條件及其工藝原理與優缺點的介紹

PCB板的SMT組裝工藝與焊接工藝介紹

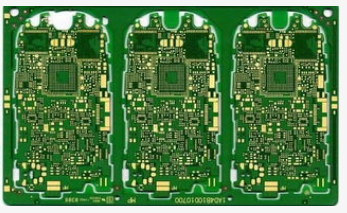
SMT基本工藝及焊接與拆焊技巧的介紹

SMT貼片加工的組裝方式及發展方向介紹

倒裝芯片工藝制程要求

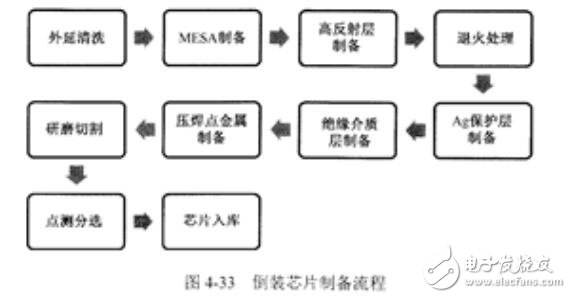
SMT組裝的詳細步驟


led倒裝芯片和正裝芯片差別

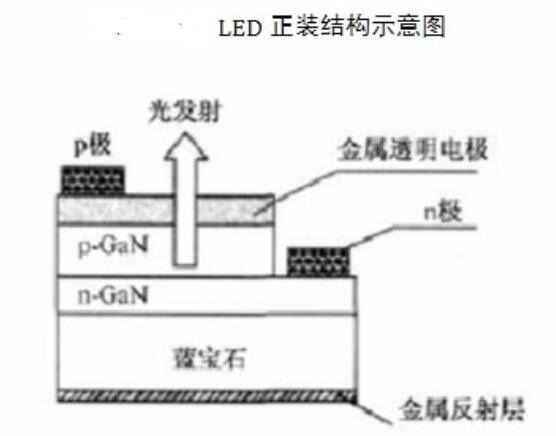
SMT工藝中對組裝工藝材料有什么要求

SMT工藝材料的種類有哪些,其有什么作用

LED倒裝芯片的水基清洗劑工藝介紹

單面SMT電路板的組裝工藝流程的解說

倒裝芯片的材料有哪些應該如何設計

如何針對SMT組裝工藝流程優化PCB設計

傳統SMT元件與倒裝芯片FC之間的區別是什么

如何應對倒裝晶片裝配的三大挑戰

SMT生產工藝的詳細介紹

倒裝芯片凸點制作方法

芯片制造倒裝焊工藝與設備解決方案

SMT PCB組裝的因素

在無鉛組裝流程中組裝高引線DS2502倒裝芯片

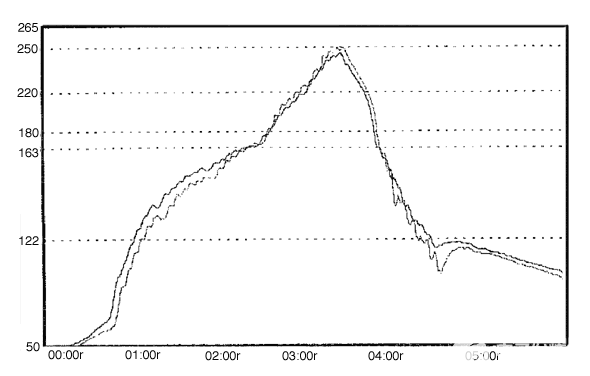
倒裝芯片球柵陣列工藝流程與技術

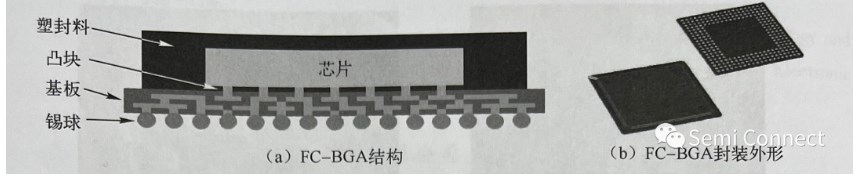
倒裝芯片,挑戰越來越大

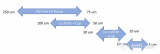
SMT電子組裝都有哪些生產步驟呢

倒裝恒流芯片NU520產品應用

SMT貼片組裝有哪些流程?

SMT表面組裝件的安裝與焊接方法

倒裝晶片的組裝工藝流程

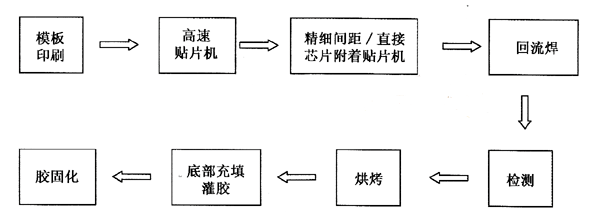
SMT組裝工藝流程的應用場景(多圖)


【華秋干貨鋪】SMT組裝工藝流程的應用場景

【華秋干貨鋪】SMT組裝工藝流程的應用場景

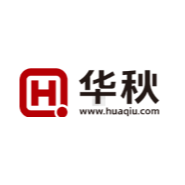
SMT組裝工藝流程的應用場景

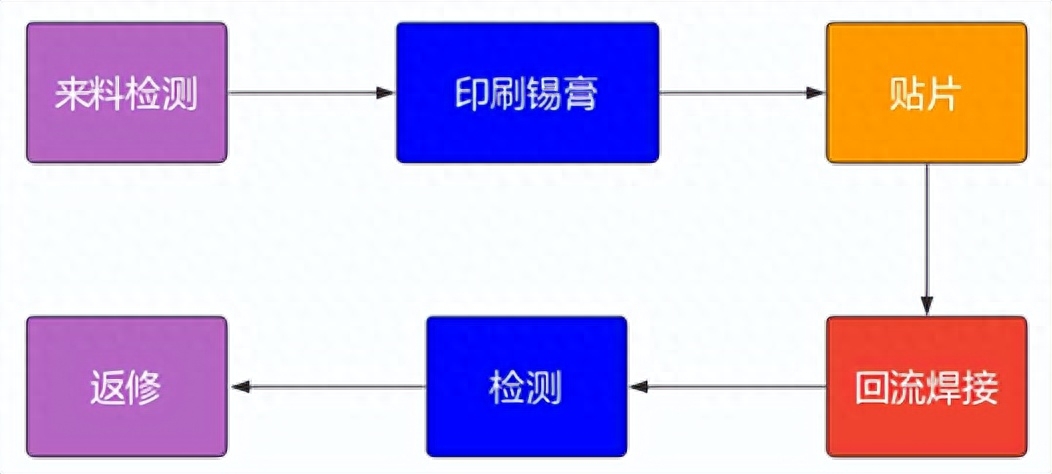
PCB板用倒裝芯片(FC)裝配技術

芯片倒裝Flip Chip封裝工藝簡介

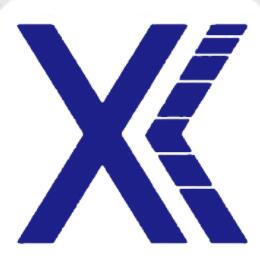
smt電子組裝有哪些生產步驟和特點

淺談FCCSP倒裝芯片封裝工藝

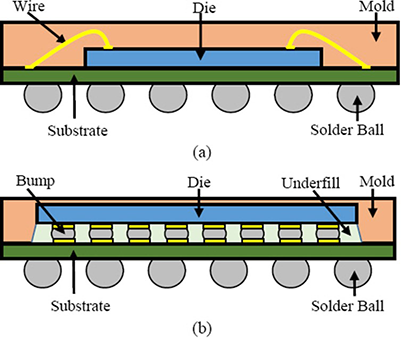
環氧助焊劑助力倒裝芯片封裝工藝

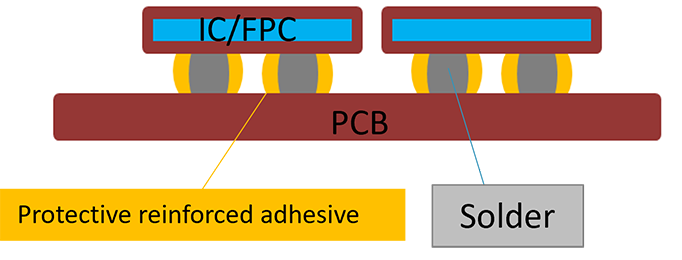
評論