當服務器、新能源汽車不斷突破功率密度極限,磁集成技術正通過融合變壓器與電感的物理邊界,實現體積與成本的雙重壓縮,成為高能效電源設計的勝負手。但磁集成在實踐過程中,材料兼容性、熱管理、測量精度等卻成了新的技術高墻。本期《對話》匯聚6位頂尖專家,直面磁集成對磁性材料、線材的核心需求,用實踐錨定路徑——這場關于空間與能量的博弈,正在重塑電源產業的競爭規則。
問題導覽:
1.磁集成對磁性材料、線材提出了哪些要求?
2.磁性材料、線材對磁集成設計有哪些約束?
3.國內磁性材料性能是否能夠滿足磁集成使用要求?
1.在開發高功率密度電源(如服務器電源、車載充電機)時,磁集成技術能帶來哪些性能提升?對磁性材料/線材而言,當前最迫切希望突破的瓶頸是什么?
陳為教授:磁集成的核心優勢在于其拓撲適配性:磁集成在特定電路拓撲中展現顯著價值,尤其適用于LLC、DAB等諧振拓撲:
可替代獨立諧振電感:磁集成直接利用變壓器漏感作為諧振電感,精簡電路結構(傳統BUCK等拓撲需獨立變壓器與電感)。
核心挑戰:功能復合化。磁集成將能量傳遞(變壓器)與能量存儲(電感)功能融合于單一磁件,導致:
功能復雜化:磁集成單一元件需同時承擔多物理過程;
分析方法失效:傳統磁路計算因以下原因不再適用:
磁集成產品漏感磁通分布于空氣中(非磁芯內部),需通過電磁場仿真精確分析空間磁場分布。
此外,測量問題是磁集成技術落地的關鍵路障:目前研發人員被迫沿用失真方法,導致設計驗證偏差;同時,磁芯損耗與繞組損耗的混疊阻礙了磁集成產品熱優化與效率提升。這需要設備商、學術界與產業界協同攻克參數解耦與高精度傳感技術。
磁集成設計的三大關鍵維度
一是結構創新設計。磁路組合策略:磁集成采用解耦柱、多磁芯拼接等方式,設計人員需基于電磁理論選擇正耦合/反耦合磁集成結構。
材料組合挑戰:磁集成后鐵氧體(變壓器)與金屬粉芯(電感)共存引發兼容性問題;磁性材料排布決定磁集成磁場分布(如粉芯在左右/上下側,磁場模式截然不同)。
二是分布參數主動控制。漏感設計為磁集成核心目標:通過磁集成繞組結構調整(如增加空氣路徑),刻意構建磁集成所需漏感;
繞組工藝復雜性:磁芯組合方式直接決定磁集成繞組結構;軟線繞制尚可應對,扁線立繞因形狀畸變導致磁集成繞線難度劇增。
三是熱管理瓶頸。磁集成產品散熱能力下降:獨立器件具備更大有效散熱面積;磁集成后熱量積聚風險顯著增加。
磁集成設計成敗關鍵:溫升超標是當前磁集成方案主要失效原因(大量案例因散熱失敗);必須通過熱設計優化控制磁集成產品溫升,否則磁集成方案失去實用價值。
陽光電源蔡國慶:磁集成技術主要帶來三方面優勢:
一是顯著降低成本(業界最關注點): 磁集成通過減少磁性元件數量,直接節省了磁性材料、線材成本和工藝成本,效果最為可觀。
二是有效降低損耗(部分方案):例如變壓器與電感的磁集成方案,磁集成產品整體損耗可能低于分立器件的總和,從而提升系統效率。
三是提升生產效率與系統可靠性:磁性元件通常難以實現全自動化貼片生產。磁集成通過減少其數量可縮短人工操作環節(如傳統變壓器所需的焊接工序),降低工時。同時,元件數量的減少也有助于提高整個系統的可靠性。
隨著隔離型拓撲中軟開關技術的普及,開關器件的損耗占比已顯著降低,主要為高頻通斷損耗。因此,磁性元件的損耗占比相對提升。以往通常在20%-30%之間,如今可能達到30%-40%甚至更高。
磁集成對損耗的降低幅度取決于應用場景:
小漏感場景(效果顯著):例如在充電樁磁集成應用中,成功的小漏感磁集成方案可完全消除一個分立電感的損耗,銅損降低約20%,效率提升明顯。
大電感值場景(效果受限):如車載OBC磁集成需要30-40μH的大感值電感時,磁集成大幅降低損耗的難度顯著增加。實踐中,將磁集成后的總損耗做到與分立器件總和持平已屬不易,還需兼顧兼容性與散熱設計。最終損耗降低幅度呈浮動狀態,很大程度上取決于企業的具體設計能力。
小結:綜上所述,磁集成雖能帶來顯著性能提升,但磁集成設計受到磁性材料高頻特性、非線性、熱膨脹以及線材高頻損耗、絕緣、尺寸等多重因素制約。
2.在設計磁集成元件(如平面變壓器、集成電感-變壓器模組)時,磁性材料的高頻損耗、磁導率非線性、熱膨脹系數對結構設計有哪些限制?線材對磁集成元件又有何影響?
田村聶應發:高頻損耗:高頻下磁芯損耗(磁滯+渦流)顯著增加,需選擇低損耗材料(對變壓器如寬溫低損耗鐵氧體及納米晶、對高頻電感氣霧化金屬粉芯)。磁集成結構上需減小磁路長度,及增加截面積或采用分段式設計以降低渦流效應。
磁導率非線性:B-H曲線的非線性導致電感量隨電流變化,可能引發飽和。需引入氣隙或梯度磁路設計,或采用多段繞組補償非線性。
熱膨脹系數:磁芯與線圈的熱膨脹差異易導致機械應力開裂。不同材料的熱膨脹系數不同,在溫度變化時可能導致磁集成元件內部產生應力。這就要求磁集成在結構設計時考慮材料的匹配,避免因熱膨脹系數差異過大而損壞元件,如在封裝材料和磁芯材料的選擇上要綜合考慮熱性能。磁集成結構設計上需要考慮對工作磁場范圍進行限制,或者采用補償電路來應對這種變化。
線材影響:繞線的趨膚效應和鄰近效應在高頻下顯著增加銅損。解決方案包括使用扁平銅帶、多股細線絞合(Litz線),或采用導電膠粘接減少接觸電阻。此外,線材的絕緣性能也至關重要,若絕緣不佳,可能會導致短路等問題,影響元件的可靠性。
銘普光磁李禮鵬:高頻損耗對結構沒有明顯的限制,在高頻損耗控制方面,我們通過磁路拓撲優化結合磁性材料特性曲線建模,將磁集成產品損耗降低。針對磁導率非線性難題,銘普首創的應力緩沖層結構設計,通過有限元仿真驗證可降低磁集成熱應力畸變,該技術已應用于我們為新能源汽車開發的DC-DC模塊磁集成產品。對于線材選型,不同的磁集成產品可能會關聯不同的電氣網絡,需要重視絕緣、安規要求。
德瓏磁電李新功:磁性材料的高頻損耗,主要表現在渦流損耗,磁滯損耗和剩余損耗,在低頻情況下,比如說MHz以下,剩余損耗其實是可以忽略不計的,主要是渦流損耗和磁滯損耗;對于高頻損耗,一般會采用寬溫低損的磁芯材料,在磁集成結構上,往往會采用中柱分段氣隙來減少磁芯的渦流損耗;
對于磁導率非線性問題,因高磁場強度下磁導率下降(飽和效應),導致電感量或變壓器耦合系數變化。故會采用預留氣隙以延緩飽和,但需權衡磁導率降低。采用分布式氣隙或復合磁材(如金屬粉芯)等方法設計磁集成產品。
關于熱膨脹系數對于結構的限制,往往表現在磁性材料與PCB或骨架磁芯與膠水等,線材的CTE不匹配會導致熱循環后機械應力下降(如開裂、脫層)等方面。為改善這類問題,采用選擇CTE匹配的材料,對于磁芯,同時要考慮高溫應用時居里溫度的限制。
線材對于磁元件的影響,主要有以下幾點:
因高頻趨膚效應與鄰近效應的存在,高頻下電流集中于導體表層,增加交流電阻,因此會優化繞組布局(如交錯繞制)降低鄰近效應。
因磁集成技術的使用,使得電源模塊的功率密度提高,磁集成產品體積更加緊湊,因此,對于線材的尺寸要求更為突出,需求的線材尺寸更小,更能適應緊湊的空間,同時,因磁集成會帶來熱量集中問題,線材的耐熱性需要提升,又因集膚效應的存在,不同頻率下的電流在導體中分布會有不同,諸如利茲線、膜包線或絞合三層絕緣線,在使用時應依據工作頻率和電流,精確選擇合適的線徑及股數,以保證電流在導體中的均勻分布來減少高頻損耗,同時,也可以根據磁集成實際需要,選用不同股數及絞距的線材,來滿足磁集成相應的散熱要求。另外因磁集成空間的要求,會選用膜包方線或膜包扁線來滿足繞組槽滿率較高的需求。最后,線材的絕緣特性也至關重要,因磁元件在高溫高頻狀態下集成后的磁心結構復雜,對磁性元件的質量穩定性、一致性以及抗冷熱沖擊的性能提出了更高要求。 這些苛刻的要求不僅考驗著磁性材料行業企業的研發實力,而且對磁性材料的應用范圍、生產工藝水平等方面提出了更高的要求,為磁性材料行業企業帶來了全新的挑戰。
磁集成產品
3.目前國內磁性材料性能是否能夠滿足使用要求?磁集成系統中,磁性元件(如電感、變壓器)的哪些性能指標對整體系統的性能或效率影響最大?是否遇到過因磁材/線材批次穩定性導致的良率波動,或性能不足導致的設計妥協?
陳為教授:從理論角度而言,目前磁性材料性能都能滿足使用,國產磁性材料基礎性能層面也已具備可行性,能夠支撐磁集成器件的功能性實現。
關鍵瓶頸已非“能否滿足”,而是“如何優化”,焦點集中于磁集成產品體積與效率的平衡(如提升功率密度與控制溫升)、以及成本與性能的取舍。
磁集成對磁性材料材料性能的需求與分立器件無本質差異。追求磁性材料所有參數(如損耗、飽和強度、成本)同時達到最優是不切實際的。
陽光電源蔡國慶:磁芯方面: 高頻應用基本采用鐵氧體磁芯,其中錳鋅類鐵氧體在國內已發展得非常成熟。國內企業在打樣效率、異形結構定制及大尺寸磁集成(如我們已實現的40*40*218規格)等方面均具備強大能力,部分大型復雜磁芯的制造能力甚至超越外資企業。因此,國內磁芯完全能滿足磁集成各類使用需求。
線材方面:高頻磁性元件主要使用多股利茲線。與國外頭部線材企業相比,國內頭部企業在部分產品規格上仍存在差距:
主流產品(如市場占比最高的0.01mm*300-500股): 國內產品完全可用,性能與國外產品無明顯差異。
大電流/高規格產品(如0.15mm*1600股及以上):在絞線工藝控制(如張力釋放)、股間絕緣可靠性及一致性方面,國內企業尚存不足。我們曾發現存在股間短路等問題。因此,在特殊應用場景或前沿技術探索時,我們仍會優先選用國外頭部企業的產品。
總體而言, 線材市場的主流需求可由國內企業滿足,但高端產品領域仍需追趕。
當前主流漏感磁集成方案,對系統影響較大的有以下四點:
電感值精度(最核心因素):漏感等效電感值必須精準控制。因為它直接影響開關管的軟開關狀態,進而對系統損耗、散熱、開關管應力及壽命產生重大影響。
體積限制:對磁集成組件的體積要求越小,集成難度越高,通常會導致效率下降。整體尺寸對系統設計(尤其是空間布局)的影響至關重要。
電磁干擾 (EMI):不同磁集成方案對周圍器件的干擾特性各異。例如,漏感過大將導致周邊散磁增多,可能干擾鄰近的開關器件、驅動電路等,甚至造成功能異常(實踐中曾多次出現因磁性元件距離驅動電路過近導致系統失效的問題)。
寄生電容:寄生電容會在磁集成產品原副邊間引發高頻諧振。變壓器結構固定后,其原副邊寄生參數與外部電容(包括開關器件自身的寄生電容)可能形成串聯諧振回路,導致波形畸變、異常及額外的損耗(此問題已在實踐中遇到)。
至于因磁性材料、線材性能導致的設計妥協案例,則有很多:
高頻軟磁材料溫升問題:磁集成組件溫升過高,往往源于磁性材料本身的損耗性能不足,無法滿足高頻應用要求。
鐵氧體抗飽和能力限制:鐵氧體材料最典型的缺點是其相對較弱的抗飽和能力。我們在漏感集成方案中遇到的電感飽和問題,就與軟磁材料的飽和特性直接相關。為避免飽和,設計時需特別關注電感值控制。
利茲線非理想換位效應:通常假設多股利茲線能實現理想換位(電流均勻分布),但在磁集成實際應用中,超過20股后基本都呈現非理想換位狀態。這導致理論計算、仿真結果與實際損耗存在顯著偏差(例如:某案例中理論最優為1200股,實測最優卻是1600股,存在400股偏差)。這種非理想性迫使磁集成設計人員在方案上妥協。
綜合影響: 上述非理想因素使得設計人員必須在磁集成裕量設計上反復權衡:裕量過小可能導致磁集成溫升超標;裕量過大則推高磁集成成本。因此,磁集成方案的設計過程往往是在多種約束下尋求折中的過程。
勝美達胡尉燦:目前國內磁性材料、線材基本能夠滿足使用要求,但有些方案可能需要付出成本代價。不過國內產品迭代速度快,只要產品做出來,很快就能找到降本的辦法。
磁集成對磁性材料/線材的核心要求主要有以下方面:
一是散熱壓力要求磁性材料具備更低的高頻損耗,低損耗是優先考慮目標。
二是磁集成導致的微型化與復雜幾何形狀,對材料加工提出特殊要求:
成型:異形磁芯需高精度模具與燒結工藝控制(如納米晶低溫成型);
封裝:低應力灌封膠避免磁集成產品因熱膨脹開裂,激光焊接替代傳統粘接;
繞線:復雜磁芯需3D繞線或分段焊接工藝;自動化設備需適應扁線/利茲線的畸變繞制路徑。
在磁集成產品實際生產過程中,確實碰到過良率波動的問題,其根源有兩方面:
一是技術協議模糊性:定義參數時側重基礎指標(如利茲線線徑、股數),未約束關鍵工藝細節(疊包均勻度、絞合角精度、張力控制范圍);
二是供應鏈認知偏差:國內廠商優先滿足基礎參數,忽視工藝一致性對系統級性能(如損耗均衡性、EMI)的影響。
這也導致磁集成產品累積公差放大,單批次內線材直流電阻波動±8%,導致電感量偏差>10%;
同時量產良率下滑:磁集成后參數耦合效應加劇,使批次間系統效率波動達3-5%。
銘普光磁李禮鵬:確實會有這種情況,但是出現的概率不大,銘普擁有完善的關鍵指標六西格瑪管控。磁集成產品從設計開始,一直到量產過程當中,會經過數次試產、可靠性測試、工藝改善、優化,在磁集成設計方案及工藝都固化之后,才到量產,避免良率波動的問題。
田村聶應發:問題根源:磁性材料燒結工藝波動、線材絕緣層厚度不均。
磁導率波動±15%導致電感量偏差,需分選材料或設計冗余氣隙(如增加5%-10%氣隙長度)。
解決方案:供應商導入SPC(統計過程控制)和DOE(實驗設計)優化工藝;來料批次全檢(如B-H曲線測試、絕緣耐壓測試); 設計容差補償(如氣隙可調結構);采用閉環反饋系統實時調整繞線匝數。
德瓏磁電李新功:有遇到過因磁芯材料一致性問題導致的磁集成產品電感不良現象。
分析其原因:首先,磁性材料供應商批次均勻性不足,導致磁材的物理特性(如磁導率、電阻率)或化學成分在不同批次間存在差異,直接影響產品一致性;其次,生產控制精度不足,設備老化或工藝參數(如燒結溫度、拉絲速度)波動導致加工過程穩定性下降,放大了磁性材料批次差異的影響;最后,管理機制缺失,未建立針對磁性材料波動進行動態調整的補償機制,導致磁集成產品生產計劃與實際需求脫節。
針對以上問題,找到解決辦法如下:
技術升級:通過高精度檢測設備(如光譜儀、磁滯回線儀)強化來料檢驗,建立磁性材料關鍵參數數據庫,篩選合格供應商;
生產端控制:實時監控,在磁集成產品關鍵工序(如繞線、磁芯組裝)引入SPC(統計過程控制)系統,通過σ值監控批次穩定性。
4.磁集成元件的微型化、復雜幾何形狀對磁性材料/線材加工性(如成型、封裝、應力、繞線)提出了哪些特殊要求?
陳為教授:參數調整的耦合效應。傳統電感感量不足時可通過調節氣隙獨立優化;磁集成產品氣隙調整仍可改變基礎感值,但會同步影響漏感(二者強耦合),需在磁集成設計中預判補償。
其本質差異在于參數調控從單變量轉向多變量協同優化,大幅增加磁集成設計復雜度。
磁芯制造的可行性。形狀不規則化:磁集成結構導致磁芯幾何復雜度提升(如多柱拼接、異形開槽),不過國內主流磁性材料廠商已具備較高柔性定制能力,工藝層面(如模具精度、燒結控制)可滿足生產需求,非核心瓶頸。
更大的挑戰在于設計人員理論能力的躍遷:需要從依賴磁路近似計算轉向掌握電磁場邊界問題求解;從獨立器件設計轉向多功能耦合系統優化。亟需通過深化電磁場理論與多參數協同方法,解決氣隙-漏感耦合、熱-磁干涉等深層問題。
分立磁性元件與磁集成對設計人員能力要求的對比
陽光電源蔡國慶:磁集成技術的發展趨勢是磁芯結構日益復雜化。 當前主流方案多基于傳統結構改進,而新型拓撲(如多柱式矩陣變壓器)則要求磁芯高度定制化。
磁芯制造:國內供應商已普遍具備滿足定制需求的能力,復雜結構可通過粘接工藝實現。因此,磁芯制造本身并非主要瓶頸。
采用粘接工藝制造復雜磁芯結構會導致磁集成成本上升,因為增加了拼裝和粘接的工序。 然而,在特定應用場景下(如6.6 kW車載OBC),這是當前磁集成必要的技術選擇。
原因在于:大功率OBC所需的磁芯截面積過大,而磁性材料本身存在類似“趨膚效應”的特性,若使用單塊磁芯將引發嚴重散熱問題。因此,現行磁集成方案是將磁芯拆分為多塊(例如:從傳統的一對磁芯塊變為四對),通過粘接組合。
需要說明的是: 這種拼接需求并不僅限于磁集成設計。高功率等級或其他特定技術要求(如散熱優化)本身就可能成為磁芯必須分塊制造的原因。
繞組設計:
復雜度控制是核心: 必須在磁集成設計源頭主動規避過度復雜的繞組結構。這不僅會顯著推高成本(通常難以接受),也將磁集成難題不合理地轉移給上游。
技術負面影響: 復雜的繞組易導致磁集成產品磁場分布畸變,進而引發額外損耗,損害磁集成效果。
在線材繞制工藝方面,目前可行的優化方案有限。主流做法仍是采用單獨繞制,其過程與傳統方式并無顯著區別。
磁集成繞組的核心差異主要體現在后端組裝環節: 與傳統連續繞制的單一線圈不同,磁集成產品所需的多個繞組需分別繞制后再進行物理組裝。因此,磁集成產品實現組裝環節的自動化是提升效率的關鍵突破口。
值得借鑒的案例: 此前在可立克參觀時,觀察到其采用連續繞制工藝一次性成型兩個獨立線圈(構成不同繞組)。此方案有效規避了磁集成后續組裝痛點,是值得推廣的優化方向。
銘普光磁李禮鵬:微型化磁集成產品的制造難點主要體現在公差管控上。例如,磁芯燒結過程中的變形會顯著影響多方向磁集成產品的公差;磁集成繞組成型產生的回彈應力也會直接影響最終的裝配精度。
田村聶應發:成型:軟磁復合材料(SMC)適合復雜形狀注塑成型,但需優化顆粒取向;納米晶需低溫燒結工藝;
封裝:低收縮率、低應力的灌封膠(如硅膠)避免機械損傷;采用激光焊接或膠粘劑封裝減少磁集成產品機械應力,設計冗余氣隙緩解磁集成產品熱膨脹 。
繞線:微型化需自動化精密繞線設備(如飛線機),復雜形狀需3D打印繞組或PCB嵌入式線圈;異形磁芯可采用分段繞制或激光焊接連接 。
應力控制:磁芯加工后需退火處理以消除殘余應力。
德瓏磁電李新功:磁集成元件微型化、復雜幾何形狀對磁性材料、線材加工提出了高精度、低損耗、高穩定性等要求。如微型磁芯加工需高精度,且需特殊涂層以增強抗腐蝕性和耐用性。磁集成元件微型化后,其復雜幾何形狀不僅要求材料具備優異的加工性能,還需在成型過程中保持高精度,以確保磁集成元件的功能和性能穩定。
封裝時,需考慮材料的熱膨脹系數,以避免應力集中導致的磁集成元件損壞。繞線工藝方面,復雜形狀可能要求采用特殊的繞線設備和技術,以保證線圈的均勻分布和緊密貼合。此外,微型化還意味著對材料的機械強度和耐久性有更高要求,以適應磁集成更苛刻的工作環境。
小結:磁集成元件的微型化和復雜幾何形狀,進一步放大了前文所述的結構設計、熱管理和材料/線材加工方面的挑戰,對磁集成加工工藝提出了特殊要求。
部分磁集成相關供應商匯總
結語
磁集成絕非簡單的元件堆疊,而是一場 “材料-結構-電磁-熱” 的四重奏。當磁集成產品損耗在系統總體損耗占比不斷提高之際,唯有 打通“基材特性-工藝控制-系統驗證” 的數據鏈(如SPC+仿真校準),才能讓磁集成從“可用的折中”走向“最優的必然”。這場靜默的元件革命,終將重塑電力電子的價值分配——其核心不在磁集成本身,而在集成之上的協同智慧。
-
服務器
+關注
關注
13文章
9802瀏覽量
88087 -
磁性材料
+關注
關注
2文章
102瀏覽量
13649
發布評論請先 登錄
這家磁性材料企業如何攻克車載OBC高耗難題
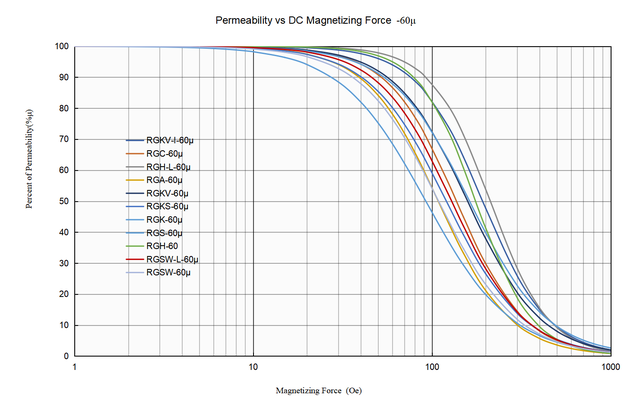
彼利奧如何應對車載OBC磁集成對線材的新考驗

EBSD技術在磁性材料研究中的應用進展
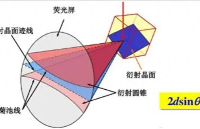
導磁材料的磁導率是多少
導磁材料的主要性質有哪些
首個磁集成專場會議 有哪些不可錯過的亮點
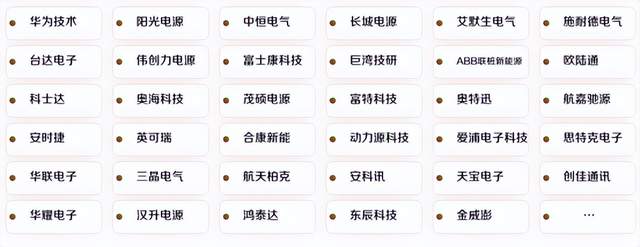
磁性材料企業半年報亮點紛呈,關注這些領域
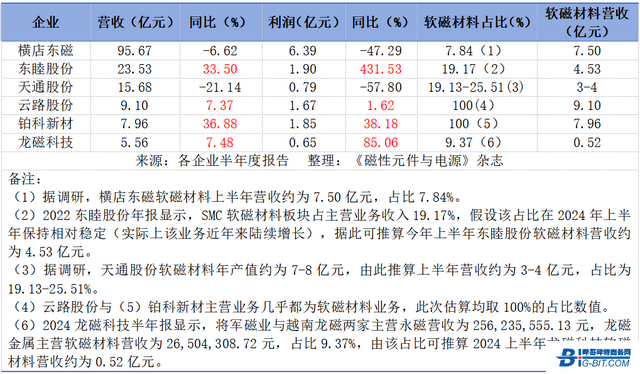
評論