詳細(xì)分析如何將GaN Systems的GaNPX? 和PDFN封裝下的E-HEMT器件焊接到PCB。
概括:
? 焊錫模板的設(shè)計(jì)
? 焊錫與助焊劑
? 回流焊的溫度曲線
? 手工焊接和拆焊、
好的焊錫模板設(shè)計(jì)可以有效改善焊錫空洞、多余焊錫球等焊接問題。以下是GaN Systems的建議:
? 設(shè)計(jì)焊錫模板時(shí),盡量避免對一個(gè)焊盤使用一個(gè)大的網(wǎng)孔。應(yīng)該使用幾個(gè)小的網(wǎng)孔,從而使得焊錫分小
方塊狀覆蓋焊盤。
? 焊錫小塊之間的距離對形成焊錫空洞與否起著決定作用。相對大的距離會(huì)容許回流焊中焊錫里的揮發(fā)物
有效溢出,從而降低焊錫空洞的概率。
? 合理范圍內(nèi),焊錫量越少,越會(huì)抑制焊錫空洞和多余焊錫球的形成。建議如下:
詳細(xì)文檔免費(fèi)下載:GaNPX?和PDFN封裝器件的焊接建議
*附件:GaNPX?和PDFN封裝器件的焊接建議.pdf
GaNPX?和PDFN封裝器件的焊接建議總結(jié)
一、簡介
本文檔提供了GaN Systems的GaNPX?和PDFN封裝下E-HEMT器件焊接到PCB的詳細(xì)建議,涵蓋焊錫模板設(shè)計(jì)、焊錫與助焊劑選擇、回流焊溫度曲線以及手工焊接和拆焊方法。
二、焊錫模板設(shè)計(jì)
- ?避免大網(wǎng)孔?:設(shè)計(jì)焊錫模板時(shí),避免使用大的網(wǎng)孔覆蓋整個(gè)焊盤,建議采用多個(gè)小網(wǎng)孔,使焊錫分小方塊狀覆蓋焊盤。
- ?焊錫小塊距離?:焊錫小塊之間的距離對減少焊錫空洞至關(guān)重要,較大的距離有助于焊錫中的揮發(fā)物溢出。
- ?焊錫覆蓋率?:建議4mil(100um)厚的焊錫模板使用70%~75%焊錫覆蓋率,5mil(120um)厚的焊錫模板使用55%~60%焊錫覆蓋率。
三、焊錫與助焊劑
- ?焊錫選擇?:推薦使用空洞率低、揮發(fā)性低的焊錫,如Indium 6.4 water soluble SAC 305。
- ?助焊劑殘留?:GaNPX?封裝器件焊接后需保持清潔,助焊劑殘留可能導(dǎo)致漏電,影響電性測試。高溫或高濕度環(huán)境下,即使使用免洗焊錫也建議清洗。
- ?助焊劑類型?:避免使用活性或酸性助焊劑,以防腐蝕影響焊點(diǎn)可靠性。
- ?布線建議?:建議在布線時(shí)避免在GaNPX? Top Cooled(頂部散熱)封裝器件下方布高壓電路,以防短路。
四、回流焊溫度曲線
- ?推薦溫度曲線?:提供了詳細(xì)的回流焊溫度曲線,確保焊錫空洞率<20%,并保證較長時(shí)間的高溫浸泡,以揮發(fā)助焊劑和焊錫中的水汽。
五、手工焊接與拆焊
- ?手工焊接步驟?:
- 將熱電偶貼到器件表面監(jiān)控溫度。
- 在PCB焊盤上涂焊錫和助焊劑(如焊盤已鋪錫并含助焊劑,可省略此步)。
- 對準(zhǔn)并放置器件。
- 預(yù)熱PCB至100-120°C,用熱風(fēng)槍吹器件表面至260-280°C,保持20-30秒。
- 撤掉熱風(fēng)槍和按壓力,待器件冷卻后清洗多余助焊劑。
- ?拆焊步驟?:
- 預(yù)熱PCB至100-120°C。
- 用熱風(fēng)槍吹器件表面至260-280°C,待器件松動(dòng)后用鑷子取下。
通過以上詳細(xì)的焊接建議,可以確保GaNPX?和PDFN封裝器件在焊接過程中獲得最佳的焊接質(zhì)量和可靠性。
-
GaN
+關(guān)注
關(guān)注
19文章
2207瀏覽量
76792 -
PCB焊接
+關(guān)注
關(guān)注
0文章
16瀏覽量
8143
發(fā)布評(píng)論請先 登錄
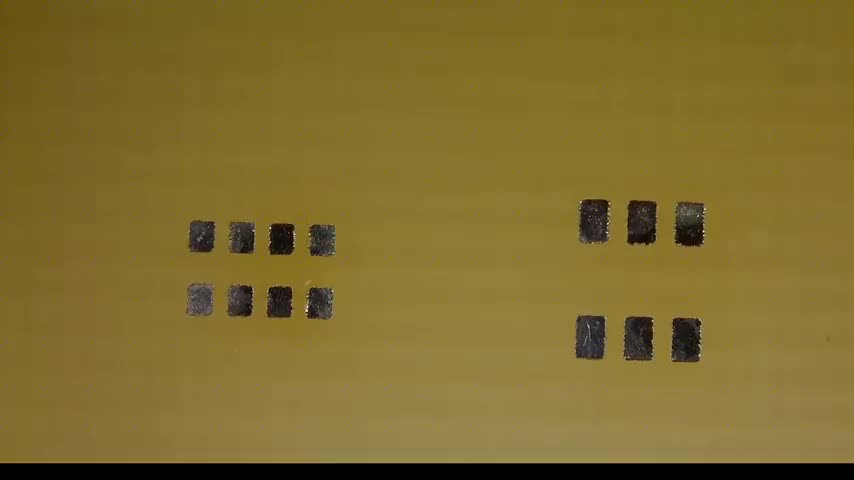
[原創(chuàng)]專業(yè)經(jīng)營電子元器件(以集成電路為主)
焊接技術(shù)-貼片元器件(密引腳IC)焊接教程
PCB LAYOUT(1):元器件布局與焊接工藝
從官網(wǎng)下載的元器件封裝可以直接用嗎?
請問器件封裝焊接工藝邊緣有損壞對器件有什么影響嗎?
焊接的幾個(gè)經(jīng)驗(yàn)
VS2508AE -20V -55A P管 PDFN3*3封裝 MOS管 場效應(yīng)管
原子哥零距離互動(dòng),分享創(chuàng)業(yè)經(jīng)驗(yàn)
QFN封裝應(yīng)該怎么焊接?
幾種不同類型器件的焊接
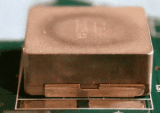
新潔能車規(guī)級(jí)PDFN 5x6雙面散熱功率器件介紹
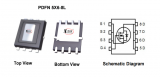
GaNPX?和PDFN封裝器件的熱設(shè)計(jì)
基于RC熱阻SPICE模型的GaNPX?和PDFN封裝的熱特性建模
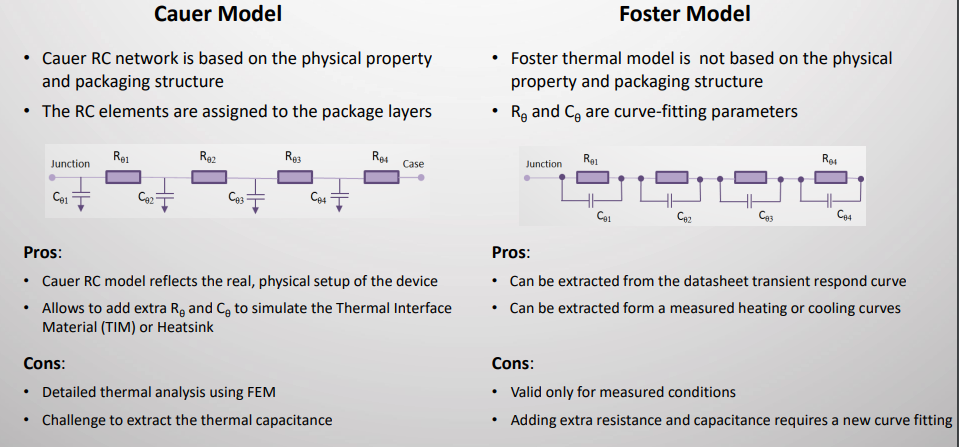
實(shí)測案例:如何用推拉力測試機(jī)進(jìn)行SMT元器件焊接強(qiáng)度測試?
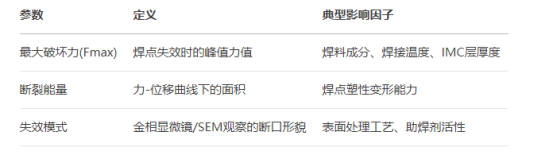
評(píng)論