環氧底部填充膠固化后出現氣泡是一個常見的工藝問題,不僅影響美觀,更嚴重的是會降低產品的機械強度、熱可靠性、防潮密封性和長期可靠性,尤其在微電子封裝等高要求應用中可能導致器件失效。
以下是對氣泡產生原因的詳細分析以及相應的解決方案:
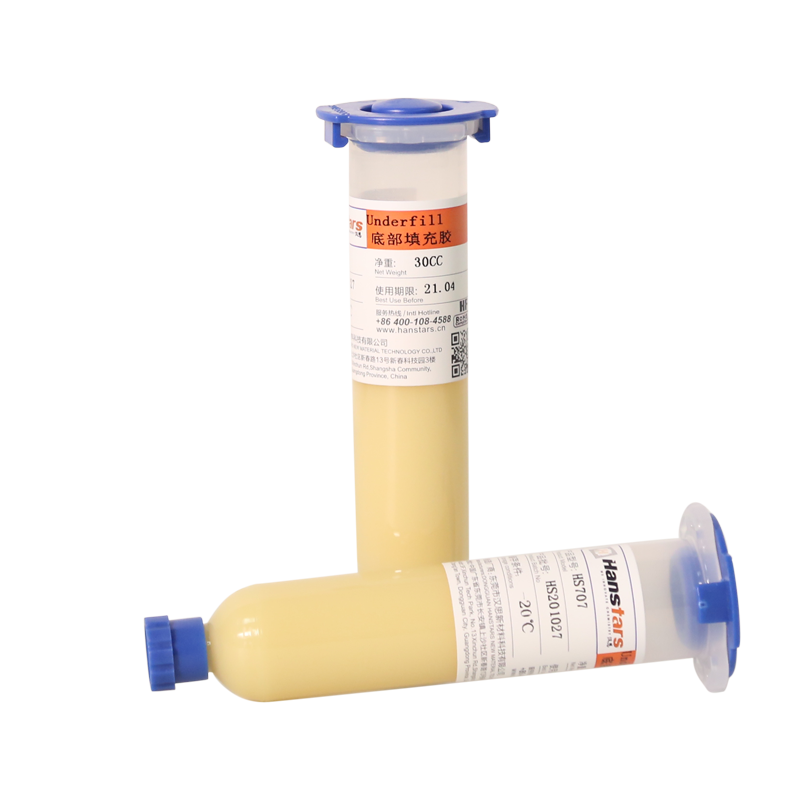
一、 氣泡產生原因分析
1. 材料本身原因:
預混膠中殘留氣泡: 膠水在混合或運輸儲存過程中本身裹入了空氣氣泡。
脫泡性能差: 膠水本身的粘度、觸變性或配方導致其脫泡能力弱,混合后或點膠前靜置脫泡效果不佳。
溶劑或低沸點成分揮發: 某些配方含有溶劑或低沸點成分,在固化升溫過程中揮發形成氣泡。
反應副產物氣體: 固化反應過程中可能產生少量低分子量的氣體副產物。
2. 點膠/施膠工藝:
點膠速度過快: 高速點膠時,膠體沖擊基板或元器件邊緣,容易卷入空氣。
點膠高度不當:
過高: 膠線“跌落”撞擊基板,容易濺射和卷入空氣。
過低: 針頭可能刮蹭到基板或元器件,干擾膠流,導致裹氣。
點膠路徑設計不合理: 路徑過于復雜、急轉彎或點膠起始/結束位置不當,容易在膠流中形成渦流卷入空氣。
針頭選擇不當: 針頭內徑過大或過小、針頭形狀(如平口針)不適合,影響膠流平穩性。
膠量不足或不連續: 膠量不足以填充間隙或點膠中斷,導致填充不連續,末端或角落容易滯留空氣。
點膠壓力/速度波動:設備不穩定導致膠流不均勻,易產生氣泡。
3. 基板與元器件因素:
表面污染: 焊盤、阻焊層、元器件底部或側壁存在油脂、指紋、助焊劑殘留、水分、脫模劑等污染物,影響膠水的潤濕鋪展性,導致填充不良和氣泡滯留。
表面能低/潤濕性差: 某些基板材料或元器件表面(如某些塑封料)本身表面能較低,膠水難以良好浸潤,形成氣穴。
元器件底部間隙復雜: 底部有凸點、凸塊、不平整或狹小縫隙,空氣不易被排出。
元器件或基板吸濕: 存儲環境濕度高,未充分烘烤除濕,在高溫固化時水分汽化形成氣泡(常見于BGA、CSP等底部間隙較大的器件)。
4. 填充環境與過程:
環境濕度高: 空氣中的水汽可能被吸入未固化的膠體中,固化時形成氣泡。
毛細流動受阻: 填充過程中,膠水在芯片底部間隙內的毛細流動前端如果受阻(如污染物、間隙突變),空氣被包裹無法排出。
填充后靜置時間不足: 點膠后立即進入固化,膠水沒有足夠時間讓已卷入的小氣泡上浮逸出(尤其對粘度稍高的膠水更重要)。
5. 固化工藝:
升溫速率過快: 這是非常常見的原因。過快的升溫速度使得膠水粘度迅速降低,同時溶劑/水分揮發或反應副產物氣體產生的速率遠大于膠水粘度降低后氣泡能逸出的速率,導致氣泡被“鎖”在固化膠體中。
固化溫度過高:超出推薦范圍的高溫可能加劇低沸點成分揮發或副反應產氣。
固化曲線不合適: 沒有設置合適的預熱平臺(預固化階段)讓氣泡在膠體粘度較低但尚未凝膠前有足夠時間逸出。
6. 設備與工具:
點膠設備不穩定: 壓力、流量控制不精確,導致點膠不均。
真空脫泡設備效果不佳: 脫泡時間不足、真空度不夠、真空腔體泄漏。
針頭或儲膠管有污染/堵塞: 影響膠流順暢性。
二、 解決方案與預防措施
針對以上原因,需要系統性地排查和改進:
1. 優化材料選擇與處理:
選擇低吸濕、低粘度、高流動性、脫泡性好的膠水: 咨詢供應商,選擇專門針對低氣泡或無氣泡應用設計的底部填充膠。
嚴格進行真空脫泡:
混合后:在點膠前必須進行充分的真空脫泡處理。確保真空度足夠高(通常要求能達到<1 Torr/百帕級別)、脫泡時間足夠(根據膠量和粘度,通常幾分鐘到十幾分鐘)、脫泡罐密封良好無泄漏。
點膠筒/針筒:灌裝到點膠筒后,可能也需要進行短時間的二次真空脫泡。
嚴格控制儲存和使用條件:膠水按要求冷藏/冷凍儲存,使用前回溫至室溫并充分攪拌(如需),避免開封后長時間暴露在空氣中吸濕或污染。
驗證膠水批次穩定性: 新批次膠水上線前進行小批量工藝驗證。
2. 改善點膠工藝:
優化點膠參數:
降低點膠速度,尤其是在拐角和靠近元器件邊緣時。
調整點膠高度,找到最佳高度(通常離基板表面0.1-0.5mm,根據針頭和膠水特性調整),避免刮蹭和飛濺。
優化點膠壓力和出膠量,確保膠流穩定連續。
優化點膠路徑: 設計簡單、順暢的點膠路徑(如“L”型或“U”型),避免急轉彎和復雜路徑。起始點和結束點通常設計在空曠區域或易于排氣的位置。確保膠線首尾相連或重疊。
選擇合適的點膠針頭:選用內徑合適(通常略大于膠點直徑)、錐形或斜口針頭,減少膠流擾動。定期檢查更換磨損針頭。
確保膠量充足且連續:精確計算所需膠量(考慮元器件尺寸、間隙、爬升高度),點膠后目檢膠線是否連續無中斷,能充分填充并形成良好“圍欄”。
3、確保基板與元器件清潔干燥:
嚴格清洗: 在點膠前進行有效的清洗工藝(如等離子清洗、溶劑清洗、水基清洗),徹底去除焊后殘留的助焊劑、油脂、顆粒等污染物。等離子清洗還能提高表面能,改善潤濕性。
充分烘烤除濕:對于吸濕性強的元器件(如BGA、塑封器件)和基板(如某些PCB材料),在點膠前必須按照規范進行高溫烘烤除濕(如125°C,8-24小時),去除吸收的水分。存儲環境應控制濕度(通常<10% RH)。
4、控制填充環境與過程:
控制環境濕度: 點膠和填充過程最好在溫濕度受控的環境中進行(如20-25°C,<40% RH)。
增加填充后靜置時間:點膠完成后,在進入固化爐之前,給予一定的靜置時間(幾秒到幾分鐘,根據膠水特性),讓已卷入的大氣泡有時間上浮破裂。對于復雜結構或高粘度膠水尤為重要。
5、優化固化工藝:
設置階梯式升溫曲線/預固化平臺: 這是解決升溫過快導致氣泡的關鍵!
第一步(預固化/凝膠化階段): 在相對較低的溫度(例如膠水凝膠化溫度附近,如80-100°C)下保溫一段時間(如10-30分鐘,甚至更長)。此階段膠水粘度顯著降低但尚未完全固化,為氣泡提供了最佳逸出窗口期。
第二步(主固化階段): 再緩慢或快速升溫到最終固化溫度(如150-165°C),完成完全固化。確保總固化時間滿足要求。
嚴格控制升溫速率: 在預固化階段結束后的升溫速率也不宜過快,特別是在膠體接近凝膠點時。
確保爐溫均勻性: 定期校驗固化爐(回流焊爐或烘箱)各溫區的溫度均勻性。
6、設備維護與管理:
定期維護點膠設備: 校準壓力、流量傳感器,檢查泵、閥、管路密封性。
確保真空脫泡設備性能: 定期檢查真空泵油、密封圈,校驗真空度。
保持針頭、儲膠管清潔: 及時清洗更換,避免堵塞或污染。
7、過程監控與檢驗:
在線監測: 對關鍵參數(點膠量、點膠路徑、點膠高度、真空度、溫濕度、爐溫曲線)進行在線監控或SPC控制。
離線檢驗:對固化后的產品進行抽檢或全檢(如X-Ray檢查、聲掃檢查、切片分析),及時發現氣泡問題并追溯原因。建立可接受的氣泡標準(如大小、數量、位置)。
總結
解決環氧底部填充膠固化后的氣泡問題是一個需要系統性工程思維的過程。材料選擇、真空脫泡、基板/元件清潔干燥、點膠參數優化(特別是速度和高度)、以及固化曲線的設計(關鍵的預固化平臺)是最常出問題也最需要重點關注的環節。必須通過嚴謹的工藝試驗設計、持續的過程監控和嚴格的物料/設備管理,才能有效控制和消除氣泡,確保底部填充的質量和最終產品的可靠性。
文章來源:漢思新材料
-
芯片
+關注
關注
460文章
52567瀏覽量
441869 -
微電子封裝
+關注
關注
1文章
31瀏覽量
7202
發布評論請先 登錄
評論