隨著電力電子設備向高頻化、小型化和高功率密度方向快速發展,磁集成技術(Magnetic Integration)成為突破傳統磁性元件體積與效率限制的核心手段。該技術通過將電感、變壓器、濾波器等磁性元件集成到單一磁芯或復合結構中,顯著降低系統損耗并提升功率密度,已廣泛應用于新能源汽車、5G通信電源、數據中心及消費電子等領域。
然而,磁集成技術依然擺脫不了對軟磁材料性能升級的要求。傳統軟磁材料(如鐵氧體、硅鋼)在高頻、高溫、強磁場等極端工況下暴露出明顯短板,倒逼材料科學界與產業界協同創新。
此前,磁技術專業委員會名譽主任委員、福州大學陳為教授在第11屆功率變換器與磁性元件聯合學術年會等公開場合在談及當前國內軟磁材料現狀時,給出的評價是“能用”。這可以說是對國內軟磁材料現狀最貼切的評價了。
本文將系統性解析磁集成對軟磁材料關鍵性能的要求,并探討未來材料創新的潛在路徑。
敦源電子磁集成產品
磁集成的核心需求與軟磁材料性能的協同關系
磁集成技術的本質是通過結構設計與軟磁材料優化,實現電磁能量的高效傳遞與損耗最小化。磁集成核心需求與軟磁材料性能的協同關系如下表所示:
磁集成核心需求與軟磁材料性能的關系,《磁性元件與電源》整理
需要強調的是,磁集成對軟磁材料的要求,不再是傳統磁性元件設計過程中一一對應的靜態映射關系,而技術需求與材料性能之間的動態平衡與迭代優化。
以高頻化為例,高頻化技術要求軟磁材料必須具有低渦流損耗(否則損耗劇增)和高磁導率(否則能量傳遞效率低)。
磁集成技術要實現高頻化、小型化、高可靠性等目標,必須依賴軟磁材料的關鍵性能參數(如飽和磁通密度Bs、損耗、溫度穩定性等),而軟磁材料性能的短板又會限制磁集成的設計邊界,形成“需求-性能”的雙向制約與適配關系。
而從系統層面,磁集成技術的實現需要電力電子、材料科學、熱管理等多領域的交叉協作,而非單一維度的參數匹配。
國家級電氣工程高級工程師、中國電源學會磁技術專委會委員、惠州市磁極新能源科技有限公司(簡稱“磁極新能源”)研發總經理海來布曲表示,目前工程師只能在設計目標與軟磁材料性能參數之間,通過雙向適配與妥協達成整體最優,從這個角度而言,未來軟磁材料的創新或提升空間依然很大。
高頻低損耗:軟磁材料的“生死線”
磁集成設計過程中,損耗增加是目前較為棘手的問題。此前英搏爾CTO高軍表示,當下比較流行的漏感集成方案中,原邊磁場會以非耦合方式進入副邊進而產生雜散磁場,且漏感的磁場會切割線包,加上電感的磁場疊加,導致高頻損耗非常大。
而在高頻磁集成場景(如MHz級開關電源)中,磁芯損耗(包括磁滯損耗、渦流損耗和剩余損耗)占總系統損耗的30%以上,成為制約效率提升的關鍵因素。
浙江工業大學磁電功能材料研究所應耀副教授在介紹其高頻低損耗鐵氧體軟磁材料時提到,剩余損耗的急劇增加,導致功率器件的過度發熱和能效的降低,剩余損耗就必須要考慮了,需要同時降低磁滯損耗、渦流損耗和剩余損耗。
可以說,高頻下損耗急劇增加是限制錳鋅鐵氧體軟磁材料高頻應用的主要障礙,也限制了磁集成向更廣的領域普及。
若現有軟磁材料無法滿足低損耗(如鐵氧體軟磁材料在1MHz下渦流損耗過高),磁集成的高頻化設計將被迫妥協,例如降低工作頻率、增加散熱成本或采取其他折中方案。
這種現象在配合第三代半導體器件的方案中尤為明顯。
為此,院校、產業界也進行了多方嘗試。
應耀教授團隊修正后的軟磁材料高頻損耗分離公式
比如應耀教授團隊通過在錳鋅鐵氧體軟磁材料中適量添加YIG,起始磁導率分別提高了28.2%和13.9%,降低了高頻損耗,在1 MHz和3 MHz的室溫損耗分別降低了56.4% and 36.6%,在25–140?C溫度范圍內也保持低損耗,并提高了晶界電阻Rgb,極大地降低了軟磁材料的渦流損耗。
不同軟磁材料因其物理特性和微觀結構差異,需軟磁材料企業采用針對性的方法降低損耗。
總體而言,不同軟磁材料的降損需結合材料本征特性與工藝創新。以下是我們梳理的不同軟磁材料領域權威專家提到的降損策略:
三類軟磁材料降損策略對比
未來,跨材料復合與原子級結構設計若能取得突破,則是降低高頻損耗極限的關鍵,屆時將進一步推動磁集成技術的普及應用。
低磁致伸縮效應:靜音與精密的基石
磁致伸縮效應(軟磁材料磁化時發生形變)是高頻振動與噪聲的主要來源,這是不同類型軟磁材料的本征特性,對無線充電、醫療設備等場景尤為關鍵。
軟磁材料磁致伸縮系數(λs)對比
不同軟磁材料的磁致伸縮系數,也從根本上限制了其應用場景。
海來布曲告訴《磁性元件與電源》,非晶合金磁芯之所以沒有突破,原因就在于其磁致伸縮系數較大,高頻下嘯叫嚴重,包括鐵基類的非晶材料都存在這一問題。
除了軟磁材料本征特性外,磁集成后也會對原有噪聲源產生疊加效應,使其變得更復雜。
此前《磁性元件與電源》在采訪吉利極氪的一位EMC專家時,其就表示:
一是元器件相互干擾現象更加嚴重。由于磁集成產后品體積縮小,各元器件之間的距離更加緊密,這也導致各個元器件之間形成了的噪聲干擾變得更大。而且磁集成產品限制了功率器件在板上的位置,導致功率器件的VDS,即D極和S極產生的快速變化電壓也成了新增干擾源。
二是從磁性元件本身雜散電容更大且更為復雜。獨立的磁性元件,其雜散電容主要由原邊和副邊的分布電容產生,來源單一,處理起來也比較容易。而磁集成產品集成了多個磁性元件,比如變壓器+電感、電感+電感等等,導致雜散電容更大更復雜,處理起來也更難。
磁致伸縮效應作為軟磁材料的本征特性,直接決定了高頻場景下的噪聲水平,而磁集成技術的引入,更將這一矛盾推向極致——軟磁材料本身的“先天不足”與系統集成的“后天干擾”形成雙重夾擊。唯有將軟磁材料材料革新與結構創新深度綁定,方能打破“高頻必噪”的魔咒,才能進一步拓寬磁集成技術的適用范圍。
可加工性與成本:產業落地的“最后一公里”
即使材料性能優越,若無法低成本加工成復雜磁芯結構,仍難實現商業化應用。
磁集成元件的可加工性直接影響量產效率與良率,尤其在復雜磁芯結構、高頻應用場景中更為突出。
各種軟磁材料加工性能對比與挑戰
從制造角度看,鐵氧體軟磁材料燒結后脆性高,易出現崩邊問題,尤其是平面磁芯薄片(<1mm)加工良率僅60%-70%。
惠州市安可遠磁性器件有限公司(下稱“安可遠”)總經理王理平接受《磁性元件與電源》采訪時表示,金屬磁粉芯由于沒有燒結工藝,通過強壓力壓制成型,需要高制密性才能做出高質量的磁芯產品,對壓制設備的壓強要求高。據了解,目前業界出現成型壓強高達25 噸/平方厘米的磁芯產品。
這導致其制造過程面臨一系列問題,一是設備成本高昂,二是制造效率低,三是能一體成型的體積或尺寸小,以純圓形磁芯為例,能一體成型的最大直徑尺寸在55mm左右。這一系列問題導致金屬磁粉芯的制造成本更高。
而非晶納米晶軟磁材料脆性大,同樣面臨傳統沖壓易開裂;納米晶需退火處理,工藝復雜度高,同樣面臨材料成本高的問題。
廣州勝美達電機有限公司中國新事業部研發經理胡尉燦在接受《磁性元件與電源》采訪時提到,早期POC電感用的工字型鐵氧體磁芯,通常會結合磁仿真和實際應用,在理想型設計結構上調大R角或增加其他改善方式。
而磁集成后,通常會面臨更復雜的磁芯結構。
胡尉燦表示,此前參觀磁芯企業時,曾見過一種應用于海外逆變器項目的磁芯,在類似于EE型磁芯結構的基礎上增加了扎邊,并開風洞以解決散熱問題,整體結構特別復雜,磁芯企業也反饋加工難度劇增。
胡尉燦舉了另外一個案例:近期還出現了一種厚度不到0.1mm的超薄鐵氧體片式磁芯,其制造采用類似于注塑的新工藝,在膠體注塑過程中帶上鐵粉固定,這種工藝比較適合于復雜磁芯的生產制造。
這種更復雜的產品結構,讓加工難度和成本都增加不少。胡尉燦告訴《磁性元件與電源》,勝美達一款應用于車載驅動的勵磁變壓器,僅磁芯加工成本就超過130元。
無論是哪種軟磁材料,磁集成后都面臨加工難度、加工成本上升的問題,尤其是磁芯一體成型的難度大大增加,需要業界探索更先進的制造工藝才能滿足制造需求。
否則對于電源設計工程師而言,只能在性能與現實工藝之間被迫妥協,如履薄冰地尋求平衡點。
結語:材料-器件-系統的協同進化
磁集成技術對軟磁材料的要求已從單一性能指標轉向“高頻-高Bs-高溫-易加工”的多目標協同優化。未來,軟磁材料廠商需與電源端深度合作,通過跨尺度設計(從原子級摻雜到宏觀電路拓撲結構優化),推動軟磁材料進入“按需定制”的新紀元。唯有如此,方能滿足高效能量轉換的終極需求。
本文為嗶哥嗶特資訊原創文章,未經允許和授權,不得轉載,
審核編輯 黃宇
-
磁芯
+關注
關注
6文章
306瀏覽量
23727 -
磁集成
+關注
關注
1文章
18瀏覽量
6188
發布評論請先 登錄
安米集團新能源軟磁材料項目常州備案
磁路中的導磁材料是什么
導磁材料的主要性質有哪些
導磁材料的磁通為什么起到傳遞能量的作用
首個磁集成專場會議 有哪些不可錯過的亮點
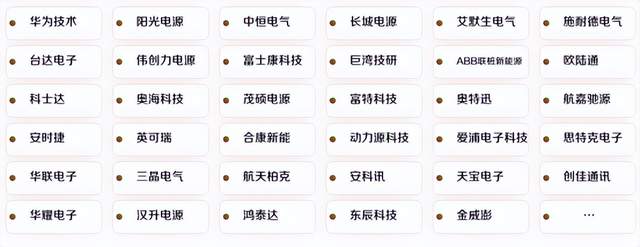
評論