來源:能量束加工及應(yīng)用技術(shù)
提高激光強度(激光功率密度)可以有效提高微孔的加工速 率。然而,過高的激光強度在加工過程中也會造成過高的表面溫度以及靶材內(nèi)部 過于陡峭的溫度梯度。毫秒激光加工的熱力學(xué)作用屬性使得人們不得不對其加工 帶來的熱力學(xué)作用給予足夠的重視。為了更易于闡明毫秒激光加工的熱力學(xué)作 用,本節(jié)選取陶瓷-金屬多層材料作為研究對象進行詳細說明。作為航空發(fā)動機葉 片的一種典型材料,帶熱障涂層(thermal barrier coating,TBC)鎳基合金的多層材 料體系主要由表層的陶瓷層、中間的黏結(jié)層(bond coating,BC)以及金屬基體構(gòu) 成,其中保證分層界面處的加工質(zhì)量尤為關(guān)鍵。
毫秒激光微孔加工是瞬態(tài)的熱力學(xué)過程,在脈沖寬度作用時間內(nèi)材料受熱發(fā) 生熔化、相變和氣化,孔腔內(nèi)部產(chǎn)生劇烈的熔體噴射以及熔融層的氣化蒸發(fā)現(xiàn)象。 當脈沖寬度作用結(jié)束時,熔體內(nèi)部開始冷卻降溫,達到一個溫度平衡狀態(tài),當下一 個脈沖到來時,重復(fù)這一過程。材料受到溫度場變化的影響產(chǎn)生變形量,尤其是界面處不同層材料的熱膨脹系數(shù)不匹配將帶來應(yīng)力集中問題。因此,為了預(yù)測和評估毫秒激光加工過程中的熱力學(xué)作用,本書建立了陶瓷-金屬多層材料毫秒激光微孔加工的熱力耦合模型。
1. 陶瓷-金屬多層材料毫米激光微孔加工的熱力耦合模型
陶瓷-金屬多層材料毫米激光微孔加工的熱力耦合模型研究的主要對象為微 孔演化過程中不同層界面處的應(yīng)力變化,為了簡化該計算模型,將涉及的物理模型和條件進行了假設(shè),列舉如下:
(1)激光源為高斯分布。
(2)考慮激光強度隨空間位置的分布。
(3)考慮材料物理特性隨溫度的變化關(guān)系。
(4)考慮不同層材料(涂層材料和鎳基合金)的吸收系數(shù)。
(5)當材料表面溫度超過氣化溫度時,材料去除。
(6)等離子演化以及流體流動未做考慮。
1)模型描述
陶瓷-金屬多層材料毫米激光微孔加工的熱力耦合模型基于經(jīng)典的傳熱方程 對材料內(nèi)部的溫度場分布進行求解,傳熱方程為
式中,p 為物體密度,kg/m3;C 為物體比熱容,J/(kg·K);q 為熱通量密度矢量,W/m2; Q 為內(nèi)熱源,W/m3 。 內(nèi)熱源可以是材料內(nèi)的體積加熱,也可以是電子與聲子之間 的熱耦合(金屬超快傳熱)。對于經(jīng)典的工程問題,熱通量密度大小與溫度場梯度 有關(guān),兩者滿足傅里葉傳熱定律,即
式中,k 為熱傳導(dǎo)系數(shù),W/(m·K)。
為了模擬求解帶涂層鎳基合金系統(tǒng)中的加工過程和應(yīng)力分布,陶瓷-金屬多層 材料毫米激光微孔加工的熱力耦合模型利用了COMSOL Multiphysics 中的傳熱 模塊、變形幾何模塊、固體力學(xué)模塊以及熱力耦合模塊等。其中,變形幾何模塊用 來追蹤孔型界面的變化;熱力耦合模塊用來預(yù)測和評估加工過程中的熱應(yīng)力變化。 圖2.6為三層材料的幾何模型示意圖。
2)相變處理及邊界條件
在陶瓷-金屬多層材料毫米激光微孔加工的熱力耦合模型中,采用有效熱容法 對固態(tài)到液態(tài)、液態(tài)到氣態(tài)以及相變過程的潛熱進行描述。材料的有效熱容Cpe可 以表示為3
式中, δm為熔化溫度附近的歸一化函數(shù);H '為平滑單位階躍函數(shù)(赫維賽德階躍函
式中,q 為邊界上的凈熱通量密度,W/m2;p 為物體密度,kg/m3;C, 為物體比熱 容,J/(kg·K);T 、 為氣化溫度,K;L、為氣化潛熱,J/kg。
為了評估和預(yù)測計算域內(nèi)的熱應(yīng)力分布,在模擬中采用了固體力學(xué)和傳熱兩 個物理場耦合的方法進行處理。材料求解區(qū)域和頂面(B?) 以及側(cè)面(B?) 均設(shè)置 為自由變形。樣品底部邊界B? 設(shè)置為固定約束。兩個物理場之間通過溫度場分 布以及材料結(jié)構(gòu)的熱變形相互耦合,并與溫度相關(guān)的材料屬性進行耦合來建立聯(lián) 系。Yilbas6 對激光微孔加工中的熱應(yīng)力進行了研究,其中熱應(yīng)力可以通過加工 區(qū)域的材料應(yīng)變與材料熱膨脹系數(shù)、溫度、應(yīng)力之間的關(guān)系進行表示:
2.模型仿真和實驗結(jié)果對比分析
本節(jié)基于陶瓷-金屬多層材料毫米激光微孔加工的熱力耦合模型,研究脈沖寬 度、激光峰值功率密度兩個激光加工參數(shù)對加工過程中孔型演化以及熱應(yīng)力變化 規(guī)律的影響。由于仿真模型忽略了熔體流動的影響,這里選取峰值功率密度大于 10?W/cm2 的參數(shù)范圍進行相關(guān)模擬,以提高模型的準確性。仿真參數(shù)如表2.2 所示,同時為了驗證該模型,在相同的仿真參數(shù)下進行微孔加工實驗。實驗中采用 同軸輔助氣體一方面有利于防止聚焦系統(tǒng)受到噴濺物的污染;另一方面有利于熔 體從孔腔內(nèi)部排出。
1)激光參數(shù)對微孔形貌的影響
圖2 . 7為5個脈沖作用下微孔加工深度的實驗結(jié)果與仿真結(jié)果對比,其誤差 在10%以內(nèi)。產(chǎn)生這種差異的原因在于實際微孔加工過程中熔體噴射是不可避 免的,并且在孔腔中熔體也會因脈沖寬度作用結(jié)束缺少驅(qū)動力而產(chǎn)生回流,或者因 反沖壓力過大而造成劇烈的噴濺。
在后面的實驗中進 一 步擴展加工參數(shù)的選用范圍,圖2 .8為不同峰值功率密 度下的微孔剖面形貌。當峰值功率密度在10?W/cm2 時,峰值功率密度較低,孔腔 內(nèi)的反沖壓力不足以提供金屬熔體向外排出的動力,引起熔體的二次回流,最終在 孔腔內(nèi)重新凝固,出現(xiàn)加工“停滯現(xiàn)象”,如圖2.8(a) 所示。當峰值功率密度增加時 (約10? W/cm2), 熔體表面溫度隨之升高,孔腔內(nèi)的反沖壓力也會增強,可以有效 地驅(qū)動熔體從孔腔內(nèi)部排出,進而有效抑制或避免加工“停滯現(xiàn)象”的發(fā)生,如 圖 2 . 8(b) 所示。
2)峰值功率密度對界面應(yīng)力和分層裂紋的影響
圖2.9為不同激光參數(shù)下分層裂紋的特征形貌。界面處的分層裂紋主要有 加工區(qū)域裂紋和非加工區(qū)域裂紋兩種。其中,加工區(qū)域裂紋代表界面處的初始 裂紋形核,而非加工區(qū)域裂紋則代表裂紋沿著界面向非加工區(qū)域進一步擴展。 實驗結(jié)果表明,隨著脈沖寬度的增加,當脈沖寬度為0.5ms 和 1ms 時,界面處逐漸產(chǎn)生非加工區(qū)域裂紋。在相同脈沖寬度下,隨著單脈沖能量(峰值功率密度) 的增加,非加工區(qū)域裂紋可以得到一定程度的抑制。當脈沖寬度為0.2ms 時,第 2組實驗參數(shù)下,在分層界面附近未見明顯裂紋現(xiàn)象,并且分層界面處均無非加 工區(qū)域裂紋產(chǎn)生,進一步提高了峰值功率密度,在界面處出現(xiàn)加工區(qū)域裂紋現(xiàn)象 。
實驗研究表明,界面處的裂紋主要是由分層材料之間的熱失配引起的7。為 了分析和理解毫秒激光加工中產(chǎn)生的熱力學(xué)作用,選擇圖2.10(a) 中 A-A 和 B- B 這兩條剖面線位置來評估打孔過程中的熱應(yīng)力變化,其中A-A 和 B-B 剖面線 分別距離孔中心軸線位置0.28mm 和0 . 5mm 。熱應(yīng)力集中易發(fā)生于微孔入口、 TBC/BC/ 基體界面和孔壁位置。另外,如圖2.10(b) 所示,微孔加工區(qū)域的材料形 變位移量較大,這也是這些位置容易萌生裂紋缺陷的原因。
圖2. 11顯示了A-A 和B-B 剖面線位置處每個脈沖結(jié)束時沿深度方向上的 熱應(yīng)力分布。從圖中可以明顯看出,在TBC/BC 界面附近(距離表面約270μm) 存 在著明顯的熱應(yīng)力突變。
圖2.12為在模擬中采用的TBC、BC以及基體的彈性模量。當界面附近的材 料與激光相互作用時,由于TBC 和BC 處的彈性模量和熱膨脹系數(shù)存在明顯差異, 不同材料對加工產(chǎn)生的熱效應(yīng)將產(chǎn)生不同的響應(yīng)。分層界面巨大的熱應(yīng)力差異引 起該位置附近產(chǎn)生不 一 致的熱變形,因此也容易誘發(fā)裂紋。同樣地,在 BC/ 基 體 界 面(距材料表面約400μm)也可以發(fā)現(xiàn)另一種熱應(yīng)力突變,但它的變化不如 TBC/ BC界面附近劇烈。這主要是由于BC 與基體材料物理特性非常接近。在相同的脈沖寬度(0.2ms) 作用下,隨著激光峰值功率密度的增加,界面熱應(yīng)力值也隨之增 加,在BC/ 基體界面附近的熱應(yīng)力也會大幅增加,如圖2.11(c) 所示。對比實驗結(jié) 果[圖2.9(b) 和(c)] 可以發(fā)現(xiàn),在高峰值功率密度下,材料界面在加工過程中將承 受更高的界面熱應(yīng)力,當其超過材料界面處的安全閾值時,界面發(fā)生破壞,進而產(chǎn) 生加工區(qū)域裂紋。
3)脈沖寬度對界面熱應(yīng)力和分層裂紋的影響
脈沖寬度對界面熱應(yīng)力的形成和擴展有著不可忽視的作用。在相同的單脈沖 能量下,隨著脈沖寬度的增加,產(chǎn)生的界面熱應(yīng)力會進一步增強,如圖2.11(e) 所 示 ,TBC/BC 界面附近的熱應(yīng)力差高達1.5×10?Pa 。如圖2 . 11(e) 和圖2.11(f 所 示,在距孔中心軸線0.28mm(A-A) 和0.5mm(B-B) 處,脈沖寬度為0.5ms 時產(chǎn)生 的界面熱應(yīng)力都遠大于在脈沖寬度為0.2ms 時產(chǎn)生的界面熱應(yīng)力。這表明,在較大 脈沖寬度下,在遠離鉆孔區(qū)域的界面位置仍將產(chǎn)生較高的熱應(yīng)力,這可能為裂紋擴展 提供一定的條件。可以預(yù)見,當使用較大脈沖寬度時,裂紋會沿著界面延伸形成嚴重 的非加工區(qū)域裂紋[圖2.9(g)、圖2 .9(h) 和圖2.9(i)]。
圖2.13描繪了脈沖周期下不同界面處熱應(yīng)力的變化規(guī)律。在微孔加工過程 中,激光脈沖周期性作用于材料。由于脈沖寬度在數(shù)值上遠小于脈沖周期,這里對 橫坐標進行了處理,以便于對比分析。在脈沖周期作用下,多層材料界面處將產(chǎn)生 相應(yīng)的熱應(yīng)力振蕩。在較大脈沖寬度下,一方面,在每個脈沖周期作用下界面處都 將產(chǎn)生更高的熱應(yīng)力;另一方面,TBC/BC 和 BC/ 基體界面在每個脈沖周期作用下 都會經(jīng)歷更加劇烈的熱應(yīng)力升(向上箭頭)和熱應(yīng)力降(向下箭頭)。例如,在第4個脈沖周期時,脈沖寬度為0.5ms 時的熱應(yīng)力升量和熱應(yīng)力降量約為脈沖寬度為 0.2ms 時的3倍。這意味著在較大脈沖寬度下,分層界面處將產(chǎn)生更強的周期性 熱應(yīng)力振蕩,經(jīng)受更劇烈的熱應(yīng)力沖擊,并且很容易產(chǎn)生裂紋使其進一步沿著界面 方 向 擴 展 。
-
耦合
+關(guān)注
關(guān)注
13文章
596瀏覽量
101665 -
模型
+關(guān)注
關(guān)注
1文章
3519瀏覽量
50418 -
仿真分析
+關(guān)注
關(guān)注
3文章
108瀏覽量
33934 -
激光加工
+關(guān)注
關(guān)注
0文章
96瀏覽量
12074
原文標題:毫秒激光加工陶瓷-金屬多層材料的仿真分析
文章出處:【微信號:深圳市賽姆烯金科技有限公司,微信公眾號:深圳市賽姆烯金科技有限公司】歡迎添加關(guān)注!文章轉(zhuǎn)載請注明出處。
發(fā)布評論請先 登錄
激光技術(shù)在材料加工領(lǐng)域的發(fā)展及應(yīng)用
激光剝離技術(shù)
金屬材料的工藝性能和切削加工性能
金屬材料水切割加工,數(shù)控水切割加工
電路板環(huán)氧樹脂基復(fù)合材料的微小孔加工技術(shù)
激光技術(shù)也應(yīng)用于多層印刷線路板的生產(chǎn)中
多層陶瓷電容漏電的原因
水切割,金屬板材水刀切割加工
先進結(jié)構(gòu)陶瓷與金屬材料釬焊連接技術(shù)的研究進展
金屬陶瓷材料傳熱特性研究
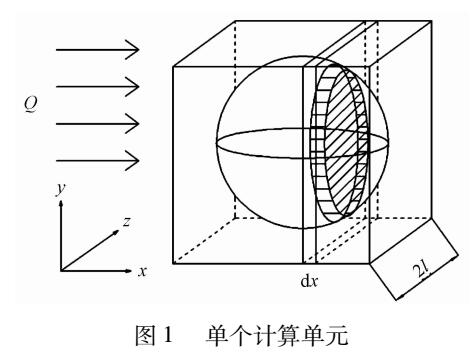
陶瓷基板激光加工成功的五個關(guān)鍵性問題
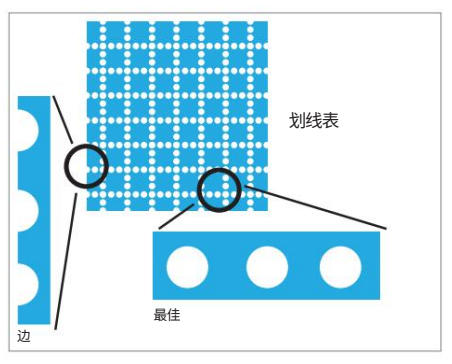
激光材料之王:為何陶瓷成首選?
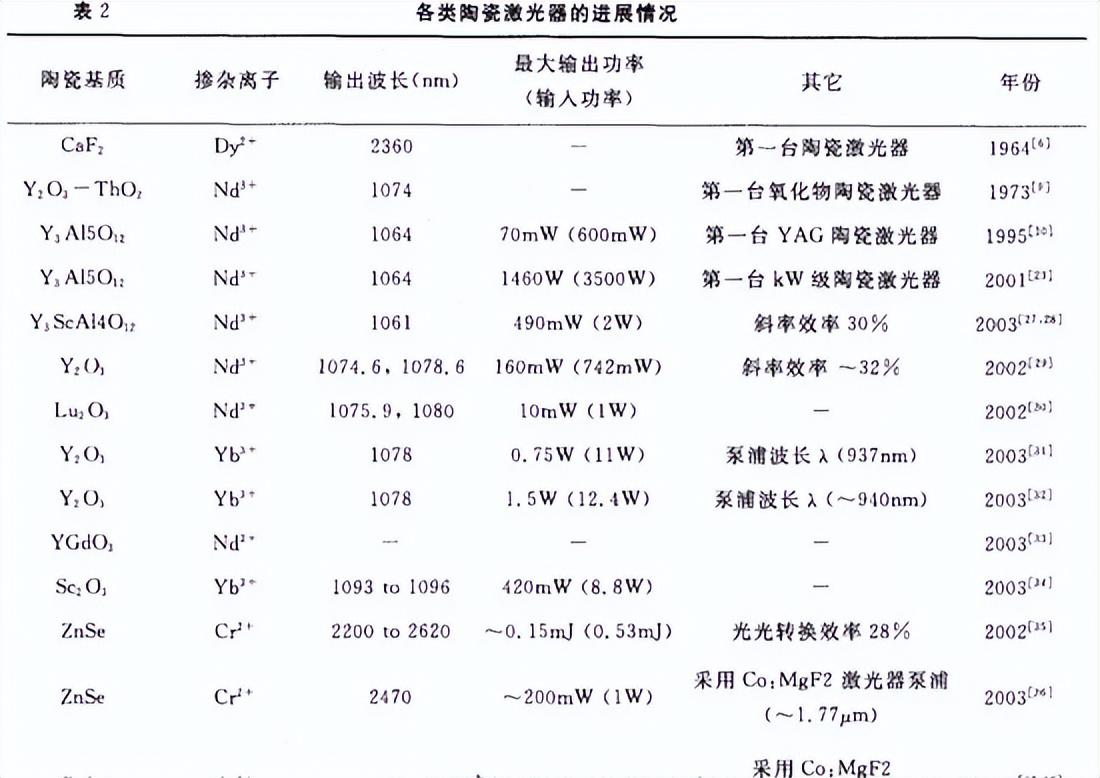
評論