在新能源汽車、儲能系統及消費電子產業高速發展的當下,電池作為核心動力源,其生產效率與質量穩定性已成為制約行業發展的關鍵因素。傳統手工或半自動化生產模式因效率低、良品率波動大等問題,正被高度自動化的電池全自動生產線逐步取代。這條集機器人技術、智能檢測與數據驅動管理于一體的生產線,正以“毫米級精度、分鐘級效率”重塑行業格局。
一、工藝流程的自動化重構
電池全自動生產線的核心在于對傳統工藝的顛覆性改造。以鋰電池模組生產為例,生產線從電芯預處理階段即啟動全流程自動化:
電芯檢測與分選:通過高精度視覺檢測系統,對電芯外觀缺陷、內阻值、電壓等參數進行實時篩選,剔除不良品,確保后續裝配質量。
精密堆疊與焊接:六軸機器人以0.02mm的重復定位精度完成電芯堆疊,激光焊接機器人采用硬光路焊接技術,實現焊接電流、電壓的毫秒級動態調整,避免虛焊、過焊等缺陷。
BMS系統集成與測試:通過模塊化設計,生產線可快速切換不同規格的電池管理系統(BMS),并完成線束壓接、絕緣檢測等工序,同時對電池組進行充放電循環測試,確保容量一致性。
智能封裝與追溯:采用全自動熱壓封裝設備,在電芯表面涂覆保護性膠水,并通過激光打碼與RFID技術實現全生命周期數據追溯,每塊電池的制造參數、測試結果均可云端查詢。
二、技術突破驅動產業升級
電池全自動生產線的革新不僅體現在硬件升級,更依托于多項前沿技術的深度融合:
人工智能算法優化:通過機器學習模型對生產數據進行分析,生產線可自主調整焊接參數、優化堆疊路徑,將產品不良率降低至0.1%以下。
柔性化生產設計:采用快換式工裝夾具與模塊化程序,生產線可在15分鐘內完成從圓柱電池到方形電池的工藝切換,滿足多品種、小批量的定制化需求。
綠色制造技術:生產線配備余熱回收系統,將高溫隧道爐的廢氣能量循環利用于電芯干燥環節,能耗較傳統產線降低30%;同時,廢舊電池智能拆解設備可實現95%以上的材料回收率。
三、產業變革中的實踐價值
在新能源汽車領域,某頭部企業通過引入全自動PACK生產線,將電池組產能提升至8萬套/年,生產周期從72小時壓縮至8小時,單車電池成本降低18%。在儲能市場,某企業利用該生產線生產的48V電池組,通過-40℃至85℃溫度循環測試,循環壽命突破8000次,遠超行業標準。這些案例印證了自動化生產線在提升質量、降低成本、縮短交付周期方面的顯著優勢。
四、未來趨勢:智能化與生態化
隨著固態電池、鈉離子電池等新型技術的崛起,電池全自動生產線正朝著更高精度、更柔性化的方向進化。例如,針對固態電池的干法電極工藝,生產線需集成納米級涂布設備與微米級定位系統;而面向鈉離子電池的低成本需求,生產線則需開發高速卷繞與低成本焊接技術。此外,通過與MES、ERP系統的深度集成,生產線將實現從訂單接收、生產排程到物流配送的全流程數字化,構建“零庫存、零浪費”的精益生產模式。
電池全自動生產線不僅是制造業升級的縮影,更是新能源產業高質量發展的基石。在“雙碳”目標驅動下,這條集成了工業4.0精髓的生產線,正以創新技術突破效率瓶頸,以智能管理重塑產業生態,為全球能源轉型注入澎湃動力。
審核編輯 黃宇
-
新能源
+關注
關注
26文章
6038瀏覽量
109070 -
電池
+關注
關注
84文章
10966瀏覽量
133852
發布評論請先 登錄
比斯特 BT-2113:動力儲能電池組全自動生產線出眾的選擇
電池組半自動生產線:效率與精度的平衡藝術
電池自動生產線:推動能源產業變革的關鍵力量
電池組PACK自動化生產線:新能源產業的高效引擎|比斯特自動化
BT-2113-18650 動力儲能電池組全自動生產線之第 5 單元:系統與防護設備保障生產的有序與安全
BT-2113-18650 動力儲能電池組全自動生產線之第 2 單元:關鍵組裝與品質保障
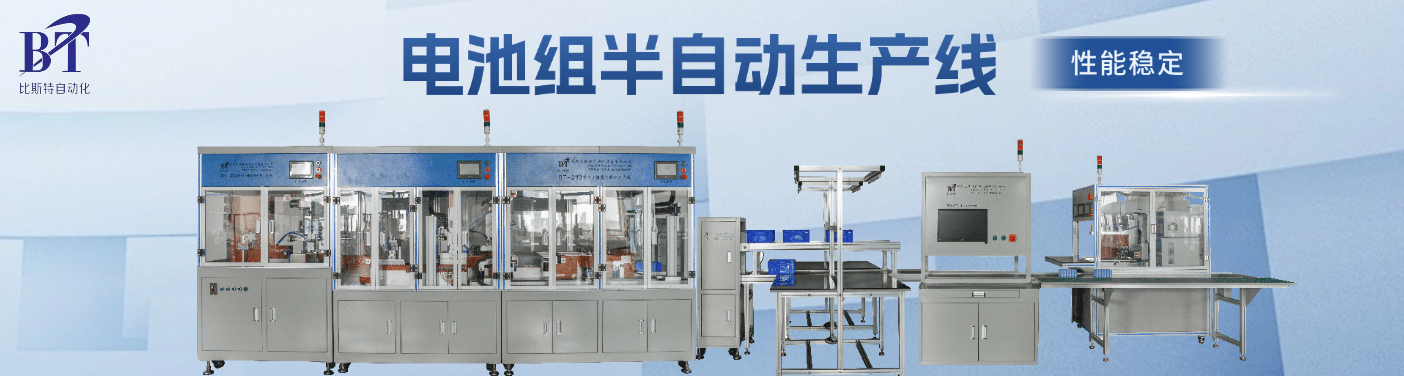
BT-2113-18650 動力儲能電池組全自動生產線之第 1 單元:電芯處理的起點
電池自動生產線:智能制造的典范與未來趨勢
電池組半自動生產線:高效、智能的生產解決方案
電池組PACK自動化生產線:驅動新能源產業的高效引擎
智能引領未來:高效電池自動生產線助力綠色能源發展
比斯特自動化|電池組全自動生產線:推動電池制造行業的革新與效率提升
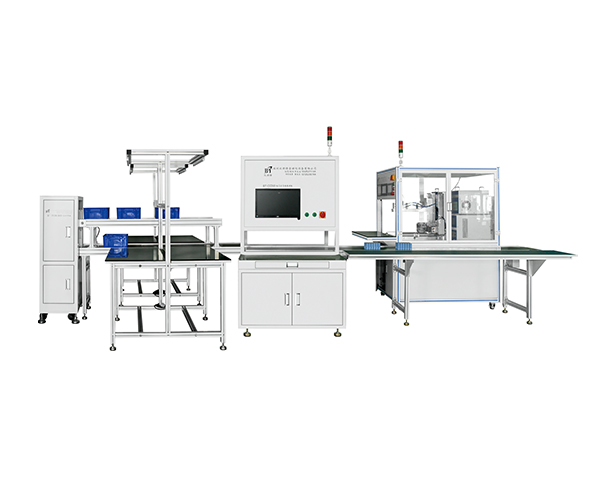
評論