在新能源汽車、儲能電站與消費電子產業需求井噴的背景下,電池組制造正經歷從全手工到全自動化的范式轉型。而半自動生產線憑借其靈活性與經濟性的雙重優勢,成為眾多中小型電池廠商突破產能瓶頸、控制設備投入的核心解決方案。這條由人工與機械臂共舞的產線,正在重構電池制造的「黃金平衡點」。
一、產線架構:模塊化設計下的「人機共生」
一條典型的電池組半自動生產線由電芯分選、模組堆疊、極耳焊接、絕緣封裝、綜合檢測五大核心工站構成,每個工站均采用「自動化設備+人工干預」的協同模式:
電芯分選工站:機械臂搭載激光測厚儀與內阻測試儀,以0.01mm精度完成電芯厚度、電壓、內阻的快速分檔,人工則負責將分選后的電芯按批次碼放入料盤。該工站自動化率達85%,但保留人工抽檢環節,使分選良率穩定在99.6%以上。
模組堆疊工站:六軸機械臂通過視覺定位系統,以±0.1mm誤差將電芯堆疊成模組,但極耳對齊與端板固定仍由工人完成。這種「粗定位自動化+精校準人工化」的組合,使模組堆疊效率較純手工提升300%,設備成本僅為全自動線的1/3。
激光焊接工站:機器人完成極耳與匯流排的焊接路徑規劃,但焊接參數(功率、速度、離焦量)需人工根據材料特性實時微調。這種「工藝留白」設計,使產線可兼容磷酸鐵鋰、三元鋰、鈉離子等不同體系電池,換型時間控制在4小時內。
二、核心工藝:精度與容錯的動態博弈
在電池組制造的「毫米級戰場」上,半自動生產線通過三大技術策略實現效率與安全的平衡:
智能輔助裝配:
在模組堆疊環節,工人佩戴AR眼鏡可實時獲取3D裝配指引,系統通過力反饋手套監測施力角度,當扭矩偏差超過±5%時自動報警。某儲能電池廠應用該技術后,模組絕緣故障率從1.2%降至0.3%。
動態過程監控:
焊接工站配備多光譜成像儀,同步監測等離子體形態與熔池溫度。當檢測到飛濺異常時,系統自動暫停并推送解決方案(如調整保護氣流量),使虛焊率控制在0.002%以內,較傳統產線降低兩個數量級。
分級檢測體系:
產線末端設置「在線電性能檢測+離線安全測試」雙保險。自動化設備完成充放電循環、內阻一致性等常規檢測后,人工使用紅外熱成像儀對電池組進行「熱點掃描」,確保熱失控風險識別率100%。
柔性生產:應對市場波動的「敏捷基因」
相比全自動線的「剛性架構」,半自動產線展現出三大適應性優勢:
產能彈性調節:通過增減人工工位數量,可在8小時內實現50%-150%的產能波動。
工藝快速迭代:當客戶提出電池組結構變更(如增加液冷板)時,僅需調整機械臂夾爪與焊接程序,無需大規模改造產線。某無人機電池廠商通過此模式,將新品導入周期從3個月壓縮至15天。
技能沉淀機制:新員工經3周培訓即可掌握關鍵工序操作,而老員工積累的工藝經驗(如焊接手勢優化)可通過數字化工卡系統傳承,避免全自動線「黑箱操作」導致的技術斷層。
審核編輯 黃宇
-
電池組
+關注
關注
5文章
340瀏覽量
26035 -
半自動
+關注
關注
0文章
10瀏覽量
10637
發布評論請先 登錄
BT-1221B儲能/動力電池組半自動生產線:賦能新能源
電池全自動生產線:驅動新能源產業升級的核心引擎
18650動力電池組PACK生產線:半自動化生產的卓越之選
電池自動生產線:驅動新能源時代的智能引擎
電池自動生產線:推動能源產業變革的關鍵力量
BT-2113-18650 動力儲能電池組全自動生產線之第 5 單元:系統與防護設備保障生產的有序與安全
BT-2113-18650 動力儲能電池組全自動生產線之第 2 單元:關鍵組裝與品質保障
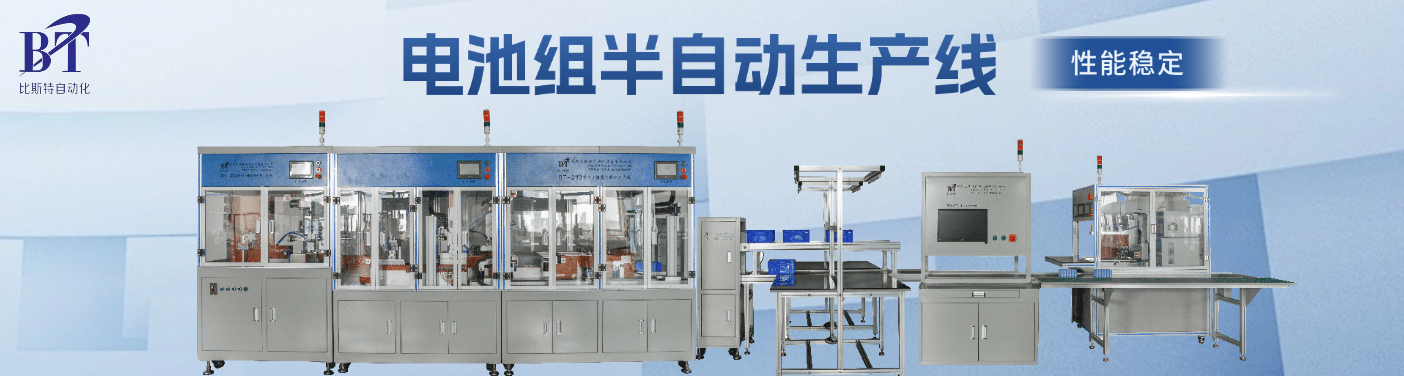
BT-2113-18650 動力儲能電池組全自動生產線之第 1 單元:電芯處理的起點
電池自動生產線:智能制造的典范與未來趨勢
電池組半自動生產線:高效、智能的生產解決方案
電池自動生產線:智能制造的典范
智能引領未來:高效電池自動生產線助力綠色能源發展
比斯特自動化|電池組全自動生產線:推動電池制造行業的革新與效率提升
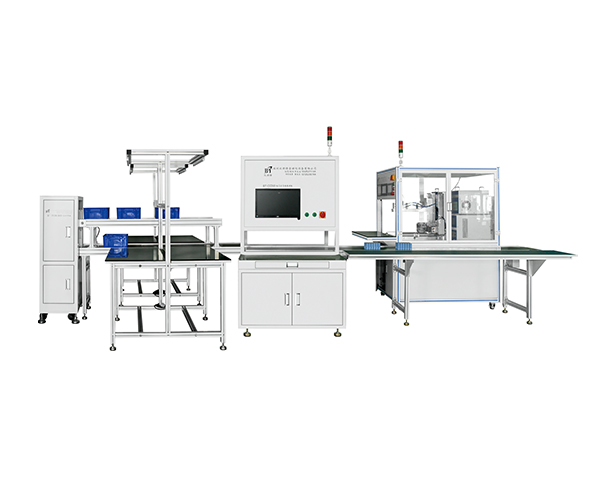
評論