根據J.D.Power的一份報告,車載音頻、通信、娛樂和導航(ACEN)類是質量投訴中問題最多的領域。作為回應,近年來汽車主機廠開始要求電子元件要使用18年零故障。其原因之一是,如果汽車一再出現故障,消費者就不太可能購買同一品牌的汽車。隨著汽車中芯片和電子元件數量的迅速增加,這一問題也變得更為嚴重。
前不久,小鵬汽車因錫須召回13399輛G3汽車,將免費更換逆變器;前后腳,特斯拉新車Model 3因逆變器故障而“死機”,卻還一度嘴硬。這不禁讓人想起了半導體器件的可靠性及其相關的一些問題:生命周期、老化失效、零缺陷等。
小鵬和特斯拉可能殊途同歸
小鵬汽車的問題很明白:逆變器直流母線電容上連接銅排螺絲的鍍錫端子錫須可能會造成高壓直流電正負極間短路,導致逆變器無高壓電供應。當這種情況發生時,如果車輛處于停車狀態,可能無法再次啟動;如果車輛處于行駛狀態,可能導致車輛失去動力,存在安全隱患。
錫須,也叫晶須,是電子產品中一種常見現象。它是一種頭發狀晶體,可以從焊錫表面自然生長出來,最常見的金屬是錫、鎘、鋅、銻、銦等。錫須是錫表面生長的錫晶體,它會導致電子短路,并引起焊點的機械破壞。
特斯拉故障現象和小鵬類似,問題或許差不多,應給予足夠的重視。專家指出,一些看似不起眼的缺陷卻有可能是一種致命缺陷。一些潛在缺陷可能永遠不會導致故障,而其他不太明顯的缺陷可能在某種環境條件或過度振動下會變成更嚴重的問題,小鵬汽車的召回介紹為了解決這個問題。
潛在缺陷與致命缺陷
對于汽車來說,雖然人們正在努力防止和發現這類缺陷,在出現問題時及時加以處理更不失為一種亡羊補牢的做法。因此,除了使器件更可靠外,還必須更容易更換。
汽車零故障何以保證?
ISO 26262的基本要求之一是能夠“優雅地”失效。這要么需要一個冗余系統,使電子設備的成本增加一倍,要么需要能夠利用不是為特定工作設計的其他電路。因此,盡管信息娛樂系統的設計可能不會被認為對安全至關重要,但在緊急情況下,其性能可能必須與關鍵系統一樣好。
然而,這帶來了一個潛在的問題。根據J.D.Power的一份報告,車載音頻、通信、娛樂和導航(ACEN)類是質量投訴中問題最多的領域。作為回應,近年來汽車主機廠開始要求電子元件要使用18年零故障。其原因之一是,如果汽車一再出現故障,消費者就不太可能購買同一品牌的汽車。隨著汽車中芯片和電子元件數量的迅速增加,這一問題也變得更為嚴重。奧迪報告說,其高端車型中有大約有7000個半導體器件,每天生產大約4000輛汽車。每百萬分之一故障相當于每天有24輛有缺陷的汽車。對寶馬來說,這相當于54輛有缺陷的汽車,因為寶馬使用了大約一半的電子元件,但每天生產10000輛汽車。
這還只是個開始,因為汽車中電子內容的數量正在上升。電子組件很快就會占到汽車成本的35%。普華永道認為,隨著自動駕駛的到來,到2030年將占汽車成本的50%。想一想,汽車今天在這里,明天在那里,惡劣的環境是一個問題。
1995年,汽車市場將成熟節點的半導體用在收音機或電動窗等相對簡單的系統。現在,汽車需要有絕對最新的技術來提供ADAS傳感器所需的所有功能。汽車行業已經無法使用已知故障模式和問題的五年前的技術。他們現在正處于最前沿,沒有人知道這些技術到底有多穩定,也不知道會出現什么問題。
如何量化和發現致命缺陷
汽車中有大量的變量,在先進節點設計芯片時也是如此,包括工藝變化到微小缺陷。關鍵是要理解并量化這些變量,然后利用積累的所有知識,能夠預測缺陷并發現致命缺陷。
從芯片的生命周期中收集數據并將其插入反饋回路是可靠性和功能安全性的關鍵。對于功能安全,在測量老化時,可以在某個時間點得出結論,器件已經老化到不再安全的程度。然后可以說這輛車需要在故障發生之前進行預防性維護。
在過去,可靠性通常被認為是制造過程的一部分。芯片要在烤箱中烘烤一段時間,或經過仔細監測的振動,以確定器件何時會出現故障。雖然在制造之前可以模擬不同的場景,但芯片仍然可能會失效,但缺陷率會降低,這取決于對各種工藝的控制有多嚴格,以及可以增加多少裕度來提供某種類型的失效接管。這在今天的ECC(錯誤檢查和糾正)內存中是很常用的方法。
不過,傳統汽車時代的一些假設正在被打破,老化就是其中之一。當汽車停駐并關閉引擎時,汽車電子設備不會停止老化。即使是在車庫里,自動駕駛汽車也永遠不會“熄火”。它可能仍然與手機通信、更新軟件,在后臺做自我檢查。
芯片能維持的使用壽命因終端市場、器件是否用于安全或任務關鍵型應用,甚至是否可以輕松更換或遠程修復而大相徑庭。
不同行業芯片的預期壽命估計
加速老化測試是模擬產品在現實使用條件下各種因素對產品產生老化的加強實驗過程。一個加速因素是溫度,另一個因素是電壓。如果一個器件在12V(汽車電池正常電壓)下工作,那么在24年的時候,這個器件已難以工作。不同的參數,如濕度、電壓、溫度、機械沖擊,這些都是加速系數。老化可以模擬器件壽命。
現在的問題是,如何加速它的壽命?當然,需要模擬的是器件在車里大約20年的壽命。如果希望在一個月內看到一個故障,那么就要使用許多組件;如果想看到20年內的一次故障,可以添加更多的組件,然后就可以得到更多的運行時間。如果想模擬一臺設備在20年內出現故障,可以拿1000臺設備運行一個小時,即1000工作小時數。使用更多組件就可以更快地測試壽命,因為真正想要的是演示運行小時數內有多少故障。這就是所謂的FIT(失效率),在109小時內出現一次故障即為1 FIT。
值得一提的是,不同汽車級別在時間質量指標上有不同的失效率。消費類級別的質量水平為100 FIT,而安全關鍵應用(如汽車中控制電池充電的電子器件)可能是0.1 FIT。所以必須根據器件的分類來模擬生存期。為了計算不同的加速系數所產生的影響,可以使用阿倫尼烏斯(Arrhenius)方程。
功能安全與可靠性
毋庸諱言,汽車電子的可靠性和功能安全性之間關系緊密。功能安全的重點是避免傷害,而可靠性是說汽車能否工作,而不需要修理。但是隨著自動駕駛的增加,兩者會有很多重疊。
如果石頭擊中傳感器會發生什么?除了自身的可靠性之外,我們還必須考慮自動駕駛汽車的功能安全性,其中一些標準是ISO 26262推動的。這是在設計階段很多工作的核心。只要芯片安全地失效,芯片失效也沒關系。這是功能安全的重點。在一輛自動駕駛汽車里,無論是芯片故障還是雷擊,不撞車都是至關重要的。當然,可靠性也很重要。最好芯片不出故障,這既是功能安全的需要,也是質量的需要。
失效對于汽車行業至關重要,而失效的機會很多。要想以可控的方式重復這一過程,并在生產線內部、工廠之間或不同供應商之間找到問題的根本原因,對可靠性是一個重大挑戰。無論你在做什么,都必須是可重復的,而且你必須能夠信任它。這使得這些公司的運營方式發生了重大轉變。
汽車電子的可靠性要求是由汽車電子委員會(AEC)定義和分級的,AEC Q-100/200是汽車IC應力測試的標準。熱、濕度和振動都是可能破壞芯片的風險因素,但材料、設計和制造工藝也會使芯片或多或少地受到風險因素的影響。這會變得復雜,細節也很重要。
在整個開發和鑒定過程中,需要明智地使用熱機械建模。例如,聚合物材料在長時間高溫下會發生永久性變化。取決于環境,這可能包括材料氧化以及導致脆化的機械性能變化。濕度也會導致片芯鈍化層和基板焊接掩模界面的附著力喪失。
冗余需要適度
冗余通常是實現航空可靠性的方法,但這會增加開支和重量。但對于汽車來說,冗余需要局限于車輛內的特定系統,因為汽車沒有那種奢侈,主機廠只是想省下每一分錢。
在汽車里,冗余是需要平衡的。隨著SoC應用的擴大,冗余有多種形式。這些技術是在更高層次上復制一些CPU或一些功能較差的塊,并確保兩者獲得相同的輸出,如果兩者中的任何一個顯示不一致的內容,則標記為一個問題。這允許在操作過程中進行某種程度的自我測試。這種方法很昂貴,因為復制了整個塊或處理器。
其他冗余設計更為精確。例如在內存寄存器級別,就像邏輯設計中的觸發器,在這里可以找到一些起關鍵作用的寄存器。要么用一個更大裕量的器件來替換它,要么加入三重模塊冗余。因此,從降低成本角度看,它是細粒度、粗粒度和各種其他技術的一種平衡。
這還取決于這些芯片是如何使用的,它們是否是復雜系統的重要組成部分,以及持續監控和反饋的成本是否可以分攤到整個系統價格中。這不是一個簡單的等式,也沒有簡單的答案,特別是在先進節點,額外的電路會增加功耗并降低性能。
先進節點的尷尬境地
高級駕駛員輔助系統(ADAS)和向完全自動駕駛方向發展正在采用最新節點的半導體制造工藝,而可靠性成為汽車行業最關心的問題。雖然成熟的節點仍然是主流,但汽車芯片已經發展成為大型復雜的SoC。其中包括集成到異構封裝和配置中的先進節點器件,這些封裝和配置還未經嘗試。過去,電子控制單元通常只有一個處理器或存儲器單元。情況不再如此,從驗證到各種類型的測試,包括符合性測試,都變得更加嚴格。
一些汽車芯片變得越來越復雜和小巧玲瓏。車輛的中央邏輯尤其如此,它需要管理所有其他系統以避免車輛出現故障。目前的設計使用的是7nm和5nm邏輯,這已是芯片制造的前沿,但這些器件必須能夠承受惡劣的環境,并且比消費芯片正常工作至少要長10年。一個節點的一種工藝是否存在問題,通常需要五到六年的時間才能知道。采用5nm到7nm技術,我們不知道會有什么變化。因此,最近NXP、高通將5nm芯片引入汽車既是在挑戰誘惑,也要面對巨大的挑戰。
回顧一下,前不久智能手機5nm芯片無一幸免被曝實際功耗不低,發熱未減。在封裝和測試方面,許多人都體驗到汽車出現故障的地方之一是標準塑料或陶瓷,其選擇主要基于成本。這表明,芯片公司的專業知識仍然存在差距,一些公司從未涉足汽車領域,而汽車供應商和主機廠對先進節點芯片設計和制造中的一些問題沒有經驗。
盡管主機廠和Tier 1的要求很嚴格,但一定程度的失效是不可避免的。電子設備會因各種原因而磨損,芯片可能由于一個設計缺陷,也可能由于芯片蝕刻時困在薄膜中的塵埃顆粒或氣流問題而出現問題。何況有大量的研究表明,當一個雜散α粒子擊中一個7nm晶體管時會發生災難性的后果。
要控制這樣的問題,需要在系統和電路兩個層面都有深入的了解,但目前還沒有足夠的數據能夠就問題可能在哪里爆發以及為什么爆發得出好的結論。
數據與可靠性息息相關
從汽車上收集有用的數據,并將其發送到反饋回路中,將成為汽車行業未來5到10年內一項常規性的工作。主機廠、芯片設計公司、半導體公司都需要通過正反饋回路來獲得更詳細的分析,因此,我們可以對所使用的設計技術和庫進行適當的調整。
實現這一功能的關鍵要素之一是從汽車中傳輸最少的數據量。這意味著汽車本身必須能夠整理出相關的數據和事件。管理所有這些數據至關重要,要考慮太多的數據以及如何以一種干凈的方式將其組合在一起。對于不同類型的工具,或者不同類型的傳感器,盡管其在物理上不同,來自不同的供應商,但在邏輯上是相同的。通過識別所有不同數據源中語義相似的內容,就可以更輕松地將其轉換為一種格式,然后提取出一些有用的結果。
關鍵在于理解什么對可靠性更重要,而這本身就是一項復雜的任務。簡單說,從汽車中收集有價值的信息非常重要。雖然這很難量化,但不能一直發送所有的數據。找到重要的數據意味著汽車或器件要有分析能力,從而最大限度地減少傳輸到云端的數據。
在車輛部署到現場之前,我們必須確保已經采取了所有的可靠性和安全措施。通過組合從生命周期不同階段提取的UCT(通用芯片遙測)數據,并用額外的數據源對其進行擴充,價值鏈上的制造商就可以將質量提高10倍,防止質量流失或“受傷”。這是通過高度先進的異常檢測方法,剔除未檢測到的缺陷,而不影響良率來實現的。即使在表征和鑒定過程中,也應對性能極限進行調整和優化,以確保足夠的可靠性裕度。
例如,Synopsys將分析引擎與嵌入芯片中的傳感器和監視器相連,利用反饋回路將芯片設計和生產各個階段的豐富數據集輸入分析引擎中。
嵌入芯片中的傳感器和監視器將豐富數據集輸入分析引擎
數據的所有權有助于實現反饋回路和生命周期管理。從汽車內部芯片的深處收集數據正在解決這個問題。如今,數據正從汽車中收集起來,并在主機廠內部共享。隨著時間的推移,根據地區、合法性、收集數據的程度以及保護數據的能力,數據所有權將成為整個設計生命周期中進行更深入分析的一個加速器。
長期可靠性是一個系統工程
針對汽車電子行業,專注于可靠性和芯片長期健康的工具和生態系統開始聯合起來。從芯片生命周期(設計、驗證、測試、制造和現場操作)收集的數據將成為實現新一代汽車的壽命、可靠性、功能安全性和安全的關鍵。
在一個平臺上擁有足夠數量的有用數據意味著主機廠及其供應鏈可以對其進行分析并據此采取行動,有可能提前預測故障,以便在設計、制造和現場操作中做出改變。
這是一個完整的生態系統,在可靠性和硅設計方面,許多事情需要共同努力才能形成一個積極的反饋回路。
隨著自動駕駛的發展,需要收集、關聯和結構化數據,以便在驗證、測試、量產和現場監測過程中對其進行評估和操作。數據需要清理、轉換成一致的格式并進行分析。盡管反饋回路中的這些步驟對某些市場來說并不完全是新的,但它代表了汽車行業的一個重大轉變。多年來,汽車行業一直在相對緩慢的手動水平上工作。現在的挑戰是使從設計到制造及其他方面的整個供應鏈現代化,并比以往任何時候都更快地從更多來源提供更詳細的信息。
主機廠正在尋找可擴展的方法來支持先進軟件技術不斷增長的性能曲線,同時保持先進節點的電子可靠性。但他們需要的是數據,以了解何時以及如何發生故障,并在故障安全機制中平衡可用性和安全性。這是一種權衡,完美并不存在。但我們正努力通過獲得這些系統健康狀況的準確可見性來改變這一等式。
改造一個龐大的全球供應鏈需要時間,它將影響從原材料采購到最終測試等各個階段。面對自動駕駛技術和通信標準的廣度和深度,一兩家公司聯合起來為汽車提供一個整體的端到端解決方案是不可能的。只有生態系統中不同的人一起協作,利用云計算和基礎設施處理,將制造和測試分析的優勢應用于雷達、激光雷達和I/O,才能實現真正的汽車安全。
責任編輯:haq
-
芯片
+關注
關注
460文章
52505瀏覽量
440796 -
汽車電子
+關注
關注
3037文章
8344瀏覽量
170155
發布評論請先 登錄
可靠性測試包括哪些測試和設備?
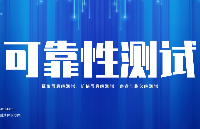
靈動微電子助力汽車芯片可靠性提升
提供半導體工藝可靠性測試-WLR晶圓可靠性測試
電機微機控制系統可靠性分析
保障汽車安全:PCBA可靠性提升的關鍵要素
電路可靠性設計與工程計算技能概述
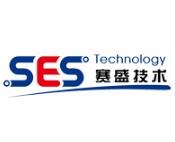
從AEC-Q100看車規芯片的可靠性設計要點
芯片可靠性測試:性能的關鍵
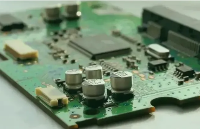
汽車車燈檢測與可靠性驗證
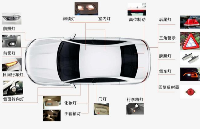
評論