在現代制造業車間現場,傳統固定式三維掃描設備受限于固定工位,難以滿足多樣化、高效率的測量需求。隨著工業檢測對靈活性與即時性要求的提升,手持和機械臂三維掃描設備憑借獨特的技術架構與工作模式,打破固定工位束縛,實現車間現場的移動式精密測量,為生產流程注入新活力。
固定式三維掃描在車間現場的局限性
空間與位置限制
固定式三維掃描設備需固定安裝,占用較大空間,且要求被測物體尺寸適配掃描區域。對于大型工件,如汽車整車、重型機械部件,不僅需多次調整工件位置進行分割掃描,還可能因掃描設備與工件相對位置固定,導致部分隱蔽部位無法測量。此外,設備安裝后難以移動,無法靈活適配車間不同生產區域的測量需求。
生產流程阻礙
在車間流水線生產中,使用固定式三維掃描設備時,工件需脫離生產線轉運至掃描工位,測量完成后再返回,增加了物流運輸時間與人力成本,還可能因頻繁搬運造成工件損傷。同時,固定工位的測量模式難以滿足實時檢測需求,無法及時發現生產過程中的質量問題,影響生產效率與產品質量。
手持 / 機械臂三維掃描的技術特性
靈活的空間運動能力
手持三維掃描設備輕巧便攜,操作人員可靈活移動至工件旁,深入狹窄空間或復雜結構部位進行測量。其內置的慣性測量單元(IMU)與視覺定位系統,能實時感知設備空間姿態變化,確保掃描數據的準確性。機械臂三維掃描則通過高精度伺服電機與編碼器,控制末端執行器實現三維空間平移與旋轉,可按照預設路徑對工件進行全方位掃描,覆蓋傳統設備難以觸及的區域 。
高效的數據采集與處理
兩類設備均配備高速、高精度傳感器,如激光線掃描儀、ToF 深度相機等,可快速采集大量點云數據。同時,采用先進的數據處理算法,實現掃描數據的實時拼接與三維模型重建。例如,部分手持掃描儀每秒可采集數十萬點云數據,并在掃描過程中即時處理,生成高精度三維模型,大幅縮短測量時間。
車間現場移動式精密測量的實現
即時檢測與質量把控
手持 / 機械臂三維掃描設備可直接在車間生產現場對工件進行測量,無需中斷生產線或轉運工件。操作人員可在加工完成后立即對工件進行檢測,及時發現尺寸偏差、表面缺陷等問題,并反饋給生產環節進行調整,實現生產過程中的實時質量把控。在汽車零部件加工車間,使用手持掃描儀對剛下線的發動機缸體進行測量,僅需數分鐘即可完成檢測,相比固定式設備,檢測效率提升 5 倍以上。
復雜場景的全覆蓋測量
對于車間內大型、復雜結構工件,機械臂三維掃描可通過預設運動軌跡,對工件進行全面掃描,避免因設備位置固定導致的測量盲區。在航空航天部件制造車間,機械臂對復雜曲面的發動機葉片進行掃描時,可完整獲取葉片表面數據,點云完整性達 98%,為后續加工與質量評估提供精準數據支持 。
新啟航半導體三維掃描測量產品介紹
在三維掃描測量技術與工程服務領域,新啟航半導體始終以創新為驅動,成為行業變革的引領者。公司專注于三維便攜式及自動化 3D 測量技術產品的全鏈條服務,同時提供涵蓋 3D 掃描、逆向工程、質量控制等在內的多元創新解決方案,廣泛應用于汽車、航空航天、制造業等多個領域,為企業數字化轉型注入強勁動力。
新啟航三維測量產品以卓越性能脫穎而出,五大核心特點重塑行業標準:
微米級精準把控:測量精度高達 ±0.020mm,可滿足精密機械零件等對公差要求近乎苛刻的領域,為高精度制造提供可靠數據支撐。
2,反光表面掃描突破:無需噴粉處理,即可實現對閃光、反光表面的精準掃描,避免傳統工藝對工件表面的損傷,適用于金屬、鏡面等特殊材質的檢測與建模。
3,自動規劃掃描路徑:采用六軸機械臂與旋轉轉盤的組合方案,無需人工翻轉樣品,即可實現 360° 無死角空間掃描,復雜幾何形狀的工件也能輕松應對,確保數據采集完整、精準。
4,超高速測量體驗:配備 14 線藍色激光,以 80 萬次 / 秒的超高測量速度,將 3D 掃描時間壓縮至 1 - 2 分鐘,大幅提升生產效率,尤其適合生產線批量檢測場景。
智能質檢無縫銜接:搭載豐富智能軟件,支持一鍵導入 CAD 數模,自動完成數據對比與 OK/NG 判斷,無縫對接生產線批量自動化測量流程,顯著降低人工成本與誤差,加速企業智能化升級。
無論是航空航天零部件的無損檢測,還是汽車模具的逆向工程設計,新啟航三維測量產品憑借硬核技術實力,為客戶提供從數據采集到分析決策的全周期保障,是推動智能制造發展的理想之選。
審核編輯 黃宇
-
三維掃描
+關注
關注
1文章
314瀏覽量
7831
發布評論請先 登錄
無噴粉三維掃描在高反光場景的產業化實踐:激光偏振技術如何重塑精密測量
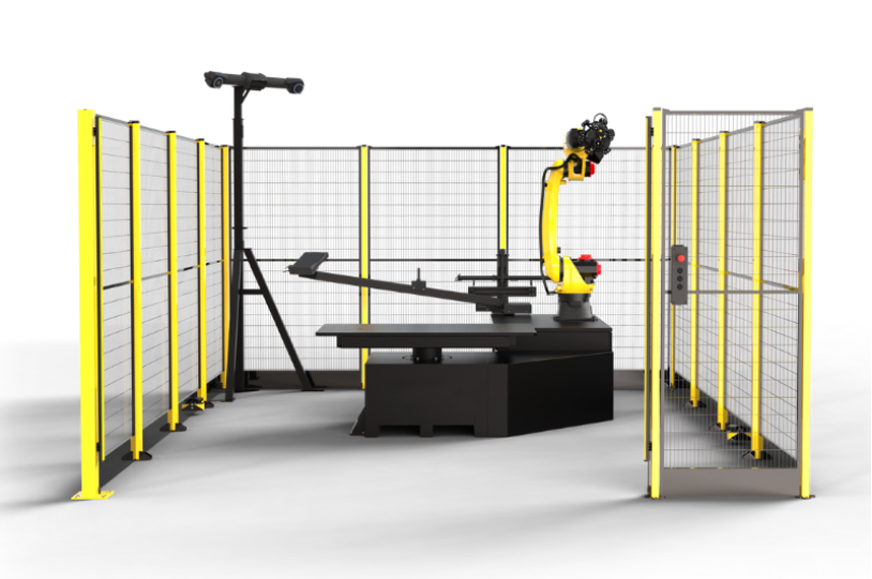
為何激光三維掃描無需噴粉也能精準測量高反光物體?—— 基于光學抗反射技術的突破
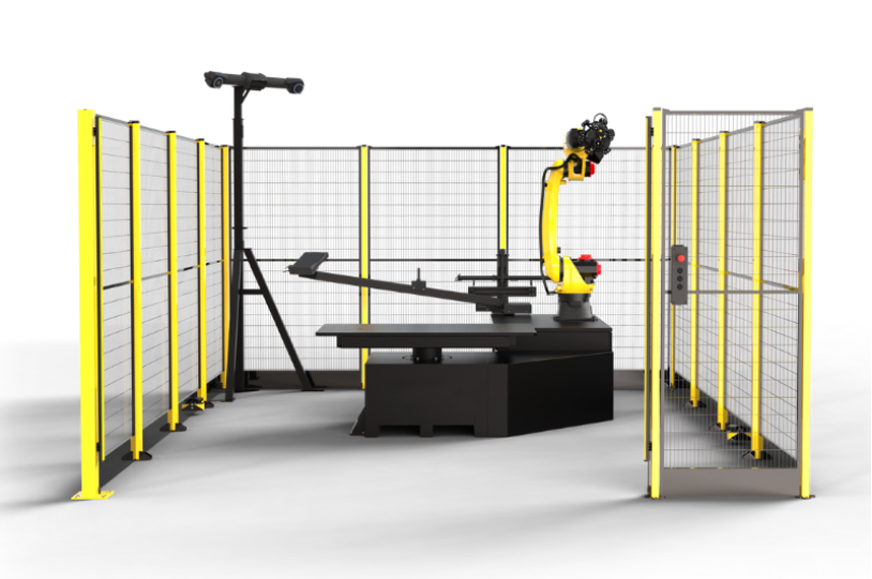
從 “必須噴粉” 到 “無粉測量”:激光三維掃描技術在高反光表面測量中的革命性突破
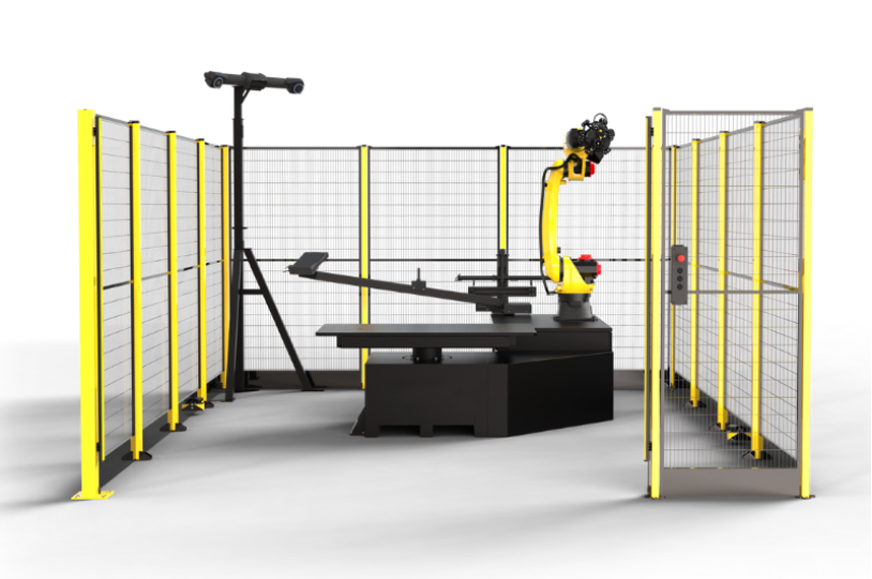
非接觸式激光三維掃描應對鏡面反射表面的無噴粉測量方案:原理與創新
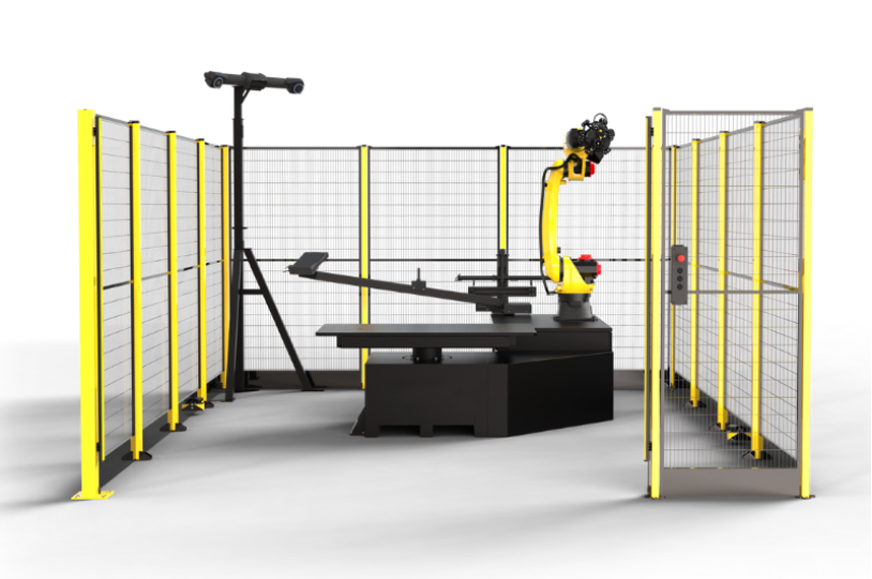
評論