在自動駕駛與電動化技術的驅動下,光電半導體器件(如激光雷達、車用 LED、光傳感器等)已成為汽車感知環境的核心組件。然而,車輛在行駛中面臨的機械應力——包括高頻振動、路面沖擊、組裝應力等——可能引發器件焊點斷裂、結構變形甚至功能失效。
AEC-Q102 認證體系中的機械可靠性測試,正是通過模擬全生命周期機械負載,為汽車光電器件構建起一道“物理防線”。
機械可靠性測試的核心邏輯與技術標準
機械可靠性測試的核心目標在于驗證器件在極端物理應力下的結構完整性與功能穩定性。AEC-Q102 標準依據汽車電子委員會(AEC)的技術規范,結合 ISO 16750 等車輛環境測試標準,制定了以下關鍵測試項目:
1.振動測試
振動測試是模擬車輛行駛中發動機震動、路面顛簸等持續振動環境的重要環節。其技術參數如下:
頻率范圍:10Hz 至 2000Hz,覆蓋車輛常見振動頻譜,能夠全面評估器件在不同頻率振動下的響應情況。
加速度:20G,相當于重型卡車行駛于崎嶇路面的沖擊強度,確保測試強度足以反映實際使用中的極端情況。
持續時間:XYZ 軸向各振動 24 小時,總時長 72 小時,通過長時間多軸向振動,充分考驗器件的耐久性。
振動測試的失效判據是器件在振動后需滿足電氣性能偏差≤5%,光學輸出波動≤3%,且無可見結構損傷。這意味著器件在經歷如此高強度的振動后,仍需保持良好的電氣和光學性能,結構上也不能出現任何損傷,從而保證其在車輛行駛過程中的可靠性和穩定性。
2.機械沖擊測試
機械沖擊測試則是模擬車輛碰撞、急剎車或跌落導致的瞬時沖擊。其技術參數如下:
沖擊波形:半正弦波,能夠有效模擬瞬間能量釋放的實際情況,使測試結果更接近真實場景。
峰值加速度:50G,相當于車輛以 30km/h 速度撞擊障礙物的沖擊力,這一高加速度的沖擊能夠充分考驗器件在極端沖擊條件下的承受能力。
持續時間:11ms,對應沖擊能量傳遞時間,確保測試能夠準確反映器件在瞬間沖擊下的響應情況。
沖擊次數:XYZ 正負方向各 3 次,共 18 次,多方向多次沖擊能夠全面評估器件在不同方向上的抗沖擊性能。
機械沖擊測試的失效判據是器件在沖擊后不得出現封裝開裂、焊點脫落或光學性能突變。封裝開裂和焊點脫落可能導致器件內部元件暴露或連接失效,而光學性能突變則會影響器件的正常功能。通過這些嚴格的失效判據,確保器件在經歷機械沖擊后仍能保持良好的結構完整性和功能穩定性,從而保障其在車輛行駛過程中的可靠性和安全性。
測試的實施與結果分析
在實施機械可靠性測試時,需要嚴格按照標準規定的測試條件和步驟進行操作,確保測試結果的準確性和可靠性。測試過程中,要對器件的各項性能指標進行實時監測和記錄,以便及時發現潛在問題。測試完成后,對測試結果進行詳細分析,評估器件在不同機械應力下的表現,確定其是否滿足 AEC-Q102 認證體系的要求。
從實驗室到道路的驗證
雖然實驗室中的機械可靠性測試能夠為汽車光電器件提供嚴格的驗證,但實際道路環境更為復雜多變。因此,在實驗室測試合格后,還需要將器件安裝到車輛上進行道路測試,進一步驗證其在實際使用環境中的可靠性和穩定性。通過在不同路況、不同氣候條件下的長期道路測試,收集大量實際數據,對實驗室測試結果進行補充和驗證,確保器件在各種復雜條件下都能正常工作,從而為汽車的安全行駛提供可靠的保障。
總結
汽車光電半導體的機械可靠性測試是一個從實驗室到道路的系統性過程,通過嚴格的測試標準和詳細的測試流程,確保器件在各種機械應力下的可靠性和穩定性,為自動駕駛和電動化技術的發展提供堅實的基礎。
-
光電半導體
+關注
關注
0文章
20瀏覽量
9140 -
器件
+關注
關注
4文章
336瀏覽量
28343 -
AEC
+關注
關注
0文章
357瀏覽量
15176
發布評論請先 登錄
車電零部件可靠性驗證(AEC-Q)
度亙核芯VCSEL產品-東方紅通過AEC-Q102車規認證
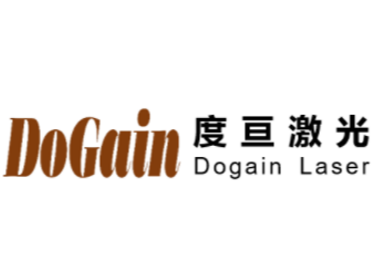
瑞豐光電Mini背光全系列通過AEC-Q102車規級認證
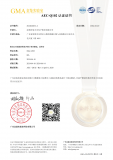
汽車電子元件的可靠性保障:AEC-Q102認證
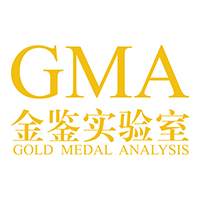
AEC-Q102之凝露試驗

板彎曲試驗在AEC-Q102的重要性
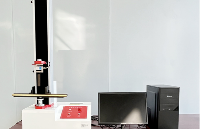
AEC-Q102之推拉力測試
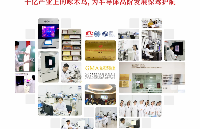
詳細解析AEC-Q102認證
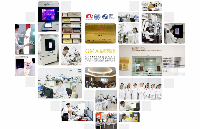
評論