來源:學習那些事
引線鍵合技術的發(fā)展瓶頸
電氣性能制約隨著片外數(shù)據(jù)傳輸速率持續(xù)提升及鍵合節(jié)距不斷縮小,引線鍵合技術暴露出電感與串擾兩大核心問題。高頻信號傳輸時,引線電感產生的感抗會阻礙信號快速通過,而相鄰引線間的串擾則造成信號干擾,這些問題嚴重限制了其在高速電子系統(tǒng)中的應用場景。
高密度互連局限現(xiàn)代硅芯片集成度呈指數(shù)級增長,對互連密度提出更高要求。傳統(tǒng)引線鍵合因物理結構限制,難以在有限空間內實現(xiàn)高密度布線,無法滿足部分高端芯片對引腳數(shù)量與間距的嚴苛需求,成為芯片性能提升的關鍵瓶頸。例如,在高性能計算領域,隨著數(shù)據(jù)處理量的爆發(fā)式增長,芯片需要集成更多的功能單元,這就要求更多的引腳來實現(xiàn)信號傳輸與電源供應。然而,傳統(tǒng)引線鍵合技術在引腳數(shù)量擴展和間距縮小方面面臨著物理極限,無法滿足高端芯片日益增長的需求,嚴重制約了芯片性能的進一步提升。
功率承載能力不足當前芯片發(fā)展趨勢呈現(xiàn) “高功率、低電壓、小節(jié)距” 特征:工作電壓已降至 1V 甚至更低,而功率消耗卻持續(xù)攀升。有預測顯示,單顆高性能芯片未來電流需求將超 100A。若采用傳統(tǒng) 25μm 線徑的引線鍵合,需數(shù)百根引線并行分擔電流,這對鍵合工藝精度、可靠性及空間布局均構成巨大挑戰(zhàn)。
焊盤與陣列互連困境I/O 焊盤節(jié)距的不斷縮短與外圍焊盤數(shù)量激增,使得單排外圍鍵合模式逼近技術極限。根據(jù) ITRSP預測,在確保高鍵合良率與載流能力的前提下,單排鍵合最小節(jié)距約為 20-25μm。盡管現(xiàn)代自動鍵合機可實現(xiàn)深度超 4μm 的多排面陣列鍵合,但由此引入的串擾問題嚴重影響信號完整性,制約整體性能表現(xiàn)。長期來看,突破 I/O 互連限制需轉向倒裝芯片(如 C4、微焊球、導電聚合物等)或新型技術。
倒裝芯片
1.焊球倒裝
技術起源與定義焊球倒裝技術(又稱 C4,可控塌陷芯片連接;或 FC,倒裝芯片)是目前替代引線鍵合的主流先進互連方案,由 IBM 于 20 世紀 60 年代中期首創(chuàng)。其核心原理是將芯片翻轉,通過焊料凸點與基板直接互連,顛覆傳統(tǒng)引線鍵合的 “垂直連接” 模式。
2.性能優(yōu)勢解析
電氣性能卓越:單個互連引線電感低至 0.05-0.1nH,相較 25μm 線徑引線的 1nH/m 電感值大幅降低,顯著提升高頻信號傳輸能力,同時有效抑制串擾與同步開關噪聲。
封裝密度領先:在密封陶瓷基板封裝中,Si 芯片可實現(xiàn) 125μm(5mil)高度的緊密堆疊;采用環(huán)氧樹脂底部填充的層壓基板(如 PCB)時,芯片間隔約 0.5mm(20mil),為高密度集成提供可能。
散熱與成本考量:焊料凸點可傳導部分熱量至封裝體,但高運算速率器件產生的大量熱量仍需從裸芯片背面(面朝上)導出。硅脂或聚合物散熱方案雖成本較低,但需定制導熱片 / 棒及昂貴封裝體,且 I/O 焊盤需圍繞植球芯片設計,導致前期投入高、量產成本難控。近年倒裝芯片在 PCB 基板的應用中,通過底部填充聚合物緩解熱膨脹系數(shù)(CTE)失配問題,降低封裝成本,但散熱能力有所折損。
工藝創(chuàng)新與優(yōu)化:為進一步降本增效,業(yè)界探索新工藝:在現(xiàn)有 Al 焊盤周邊采用熱超聲球形鍵合技術(省去引線)直接形成凸點,并結合導熱聚合物或微球材料,簡化流程的同時提升散熱性能。
應用演進與趨勢 :早期倒裝芯片推廣受阻,因需重新設計面陣列 I/O 焊盤,且傳統(tǒng)封裝難以適配。雖有程序可將外圍焊盤轉為面陣列格式,但此類過渡設計存在熱傳導效率低、串擾大等問題。隨著移動電話等便攜式終端對 “小體積、高頻性能、高集成度” 的需求爆發(fā),越來越多芯片直接采用原生面陣列倒裝設計。當前該技術增速遠超引線鍵合,長期來看有望成為多領域互連首選方案。
球凸點 / 柱凸點倒裝技術
技術應用規(guī)模與優(yōu)勢:近年來,球凸點 / 柱凸點倒裝技術的應用呈現(xiàn)迅猛增長態(tài)勢。每年全球數(shù)十億個聲表面波(SAW)濾波器及數(shù)億個集成電路(IC)都采用該技術實現(xiàn)互連。其核心競爭力在于工藝兼容性 —— 借助球形鍵合機,能夠將金(Au)或銅(Cu)材質的倒裝凸點,直接鍵合到按常規(guī)引線鍵合設計的現(xiàn)有晶圓或芯片上。這意味著無需對原有芯片布局進行大模修改,大幅降低了從傳統(tǒng)引線鍵合向倒裝工藝轉型的成本與技術門檻。
設備與工藝配套發(fā)展:市場需求的激增促使自動鍵合設備制造商紛紛推出專用的球凸點鍵合機。此類設備具備強大的批量處理能力,可在整片晶圓上快速完成數(shù)萬個凸點的鍵合作業(yè)。完成凸點鍵合的晶圓經切割后,即可進入芯片倒裝環(huán)節(jié),通常會采用導電環(huán)氧樹脂或其他鍵合方法實現(xiàn)芯片與基板的連接。
載帶自動鍵合(TAB)技術
1.技術原理與結構基礎
TAB 技術誕生于 20 世紀 60 年代,其核心組件為矩形(帶狀、鍍錫處理)的銅梁引線,這些引線通過聚酰亞胺等薄聚合物載帶固定。行業(yè)標準中,載帶寬度通常為 35mm。在實際工藝里,銅梁引線會通過焊接(合金化)的方式,與芯片外圍預先植有金(Au)凸點的焊盤相連。不過需注意,無論是 TAB 還是引線鍵合技術,均難以適配倒裝芯片的面陣列鍵合需求。下圖為典型的TAB封裝結構
2.多樣化鍵合方式
凸點鍵合:可利用熱超聲工藝,將 TAB 引線與預植的球形或柱狀凸點實現(xiàn)可靠連接;
無凸點鍵合:經改裝的自動引線鍵合機,能直接將 TAB 引線鍵合到普通焊盤上(即無凸點 TAB 工藝)
激光焊接: 借助激光能量,可精準地將 TAB 引線焊接到凸點表面,進一步提升鍵合精度。
3.性能與成本特性
性能優(yōu)勢:矩形引線在高頻環(huán)境下的阻抗低于傳統(tǒng)圓引線;在早期(截至約1990 年),其可實現(xiàn)的鍵合節(jié)距比楔形、球形鍵合更小;雙層金屬結構的 TAB,相比引線鍵合,能進一步降低電感與串擾。
成本局限:TAB 載帶材料本身價格高昂,且定制掩模成本不菲。芯片或封裝焊盤位置哪怕出現(xiàn)微小變動,都需更換新的載帶與掩模。此外,TAB 技術的間距通常較大,難以實現(xiàn)芯片疊放,散熱多依賴裸芯片背面(倒裝 - TAB 因引線短、電感低稍作例外,但仍需從芯片背面散熱,不同于倒裝芯片通過焊料凸點散熱)。在大功率應用場景下,還需搭配昂貴的封裝體。圖示為較老的TAB載帶(12mm和35mm)和焊接到基板上的TAB芯片照片。
4.應用現(xiàn)狀與趨勢
在過去,TAB 技術在交付昂貴的系統(tǒng)級封裝(SIP)或其他多芯片封裝前,具備可測試性與芯片老練的顯著優(yōu)勢。但隨著已知良品裸芯片(KGD)及預測試芯片尺寸封裝的廣泛應用,這一優(yōu)勢正逐漸減弱。由于載帶定制成本高且缺乏靈活性,TAB 已不再適用于主流芯片封裝。不過,作為一項仍具經濟效益的技術,TAB 仍在特定領域(如對成本敏感度低、對高頻性能要求嚴苛的特殊芯片)持續(xù)尋找應用空間。
-
封裝
+關注
關注
128文章
8526瀏覽量
144828 -
倒裝芯片
+關注
關注
1文章
102瀏覽量
16529 -
引線鍵合
+關注
關注
2文章
26瀏覽量
8396
原文標題:引線鍵合替代技術
文章出處:【微信號:深圳市賽姆烯金科技有限公司,微信公眾號:深圳市賽姆烯金科技有限公司】歡迎添加關注!文章轉載請注明出處。
發(fā)布評論請先 登錄
有償求助本科畢業(yè)設計指導|引線鍵合|封裝工藝
混合電路內引線鍵合可靠性研究
集成電路封裝中的引線鍵合技術

LED引線鍵合工藝評價
引線鍵合工藝流程講解
引線鍵合是什么?引線鍵合的具體方法
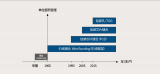
什么是引線鍵合?引線鍵合的演變
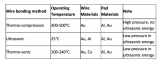
引線鍵合技術:微電子封裝的隱形力量,你了解多少?
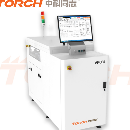
帶你一文了解什么是引線鍵合(WireBonding)技術?
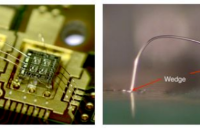
什么是引線鍵合?芯片引線鍵合保護膠用什么比較好?
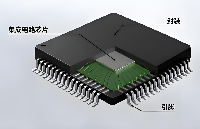
評論