我們?nèi)A林科納通過光學(xué)反射光譜半實時地原位監(jiān)測用有機堿性溶液的濕法蝕刻,以實現(xiàn)用于線波導(dǎo)的氫化非晶硅(a-Si:H)膜的高分辨率厚度控制。由a-Si:H的本征各向同性結(jié)構(gòu)產(chǎn)生的各向同性蝕刻導(dǎo)致表面粗糙度<1nm的均勻蝕刻。適度的蝕刻速率使得能夠在室溫下以≤1nm的分辨率進行精確的終點檢測。由蝕刻的A-Si:H薄膜制成的線波導(dǎo)具有1.2dB/cm的低傳播損耗,這幾乎相當(dāng)于未蝕刻的線波導(dǎo)。
用硅材料制成的光波導(dǎo)部分取代全球金屬布線,有望在大規(guī)模集成器件中實現(xiàn)更快的信號傳輸和更大的節(jié)能。硅材料由于其高折射率和互補金屬氧化物半導(dǎo)體(CMOS)工藝兼容性,使得能夠低成本制造尺寸與布線電路相當(dāng)?shù)某⌒?a href="http://www.asorrir.com/v/tag/4854/" target="_blank">光學(xué)電路。在硅材料中,氫化非晶硅(a-Si:H)是一個很有前途的例子,因為它允許通過低溫等離子體增強化學(xué)氣相沉積(PECVD)在現(xiàn)有的電層上連續(xù)形成硅波導(dǎo)。到目前為止,一些小組已經(jīng)使用a-Si:H材料制造了高質(zhì)量的線波導(dǎo)。
然而,用于生長a-Si:H膜的PECVD工藝通常在膜厚度上產(chǎn)生65%的偏差。對于厚度為200nm的膜,該偏差對應(yīng)于610nm,這對于許多器件應(yīng)用,尤其是那些對波長敏感的器件應(yīng)用是不可接受的。因此,在PECVD之后需要額外的工藝來提供具有納米級分辨率的精確厚度控制?;瘜W(xué)機械拋光(CMP)已被用于調(diào)整a-Si:H膜的厚度。1-3然而,通常很難高精度地檢測CMP的終點。在這封信中,作為CMP的替代方法,我們報告了濕蝕刻方法與半實時光學(xué)厚度監(jiān)測器相結(jié)合的實用性,以提供分辨率為~1nm的精細厚度控制。這種方法不會顯著增加沉積態(tài)a-Si:H膜的表面粗糙度,從而能夠制造出具有低傳播損耗of~1dB/cm的線波導(dǎo)。
使用原子力顯微鏡的輕敲模式評估室溫下蝕刻前后的表面粗糙度。8蝕刻前膜的均方根表面粗糙度為0.739nm,蝕刻后膜的均均方根表面粗度為0.891nm,蝕刻在220nm的膜厚度處停止。因此,即使在通過蝕刻去除約100nm的膜之后,表面粗糙度也僅略有增加。對于薄膜上的幾個點獲得了一致的結(jié)果。
總之,我們?nèi)A林科納為了實現(xiàn)PECVD沉積a-Si:H薄膜的高分辨率厚度控制,開發(fā)了一種使用TMAH溶液和光學(xué)反射光譜半實時原位厚度監(jiān)測的濕法蝕刻方法。由于室溫下~4nm/min的適度蝕刻速率和~2s的測量響應(yīng)時間相結(jié)合,蝕刻終點可以控制在≤1nm的分辨率。即使在通過蝕刻去除約100nm的膜之后,膜的表面粗糙度也僅略有增加。由蝕刻的a-Si:H膜制成的線波導(dǎo)的傳播損耗幾乎等于未蝕刻的線波導(dǎo),并且是迄今為止報道的最低的。所開發(fā)的蝕刻方法可用于生產(chǎn)低傳播損耗波導(dǎo)器件,并且與CMOS工藝具有良好的兼容性。
為更好的服務(wù)客戶,華林科納特別成立了監(jiān)理團隊,團隊成員擁有多年半導(dǎo)體行業(yè)項目實施、監(jiān)督、控制、檢查經(jīng)驗,可對項目建設(shè)全過程或分階段進行專業(yè)化管理與服務(wù),實現(xiàn)高質(zhì)量監(jiān)理,降本增效。利用仿真技術(shù)可對未來可能發(fā)生的情況進行系統(tǒng)的、科學(xué)的、合理的推算,有效避免造成人力、物力的浪費,助科研人員和技術(shù)工作者做出正確的決策,助力工程師應(yīng)對物理機械設(shè)計和耐受性制造中遇到的難題。
審核編輯 黃宇
-
半導(dǎo)體
+關(guān)注
關(guān)注
335文章
28509瀏覽量
231795 -
監(jiān)測
+關(guān)注
關(guān)注
2文章
3870瀏覽量
45307 -
蝕刻
+關(guān)注
關(guān)注
10文章
424瀏覽量
15921 -
波導(dǎo)
+關(guān)注
關(guān)注
3文章
98瀏覽量
19079 -
光波導(dǎo)
+關(guān)注
關(guān)注
4文章
49瀏覽量
10378
發(fā)布評論請先 登錄
雷尼紹測頭為什么具有各向同性
濕蝕刻
《炬豐科技-半導(dǎo)體工藝》CMOS 單元工藝
《炬豐科技-半導(dǎo)體工藝》GaN晶體蝕刻的幾何方面和光子應(yīng)用
用各向異性濕法蝕刻技術(shù)制作的低損耗硅波導(dǎo)
晶圓濕式用于硅蝕刻浴晶圓蝕刻
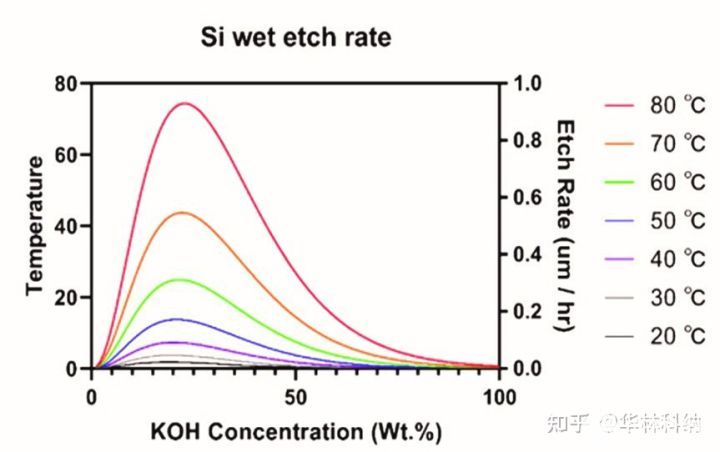
各向同性和各向異性工藝如何用于改善硅濕蝕刻

晶圓濕式用于硅蝕刻浴晶圓蝕刻
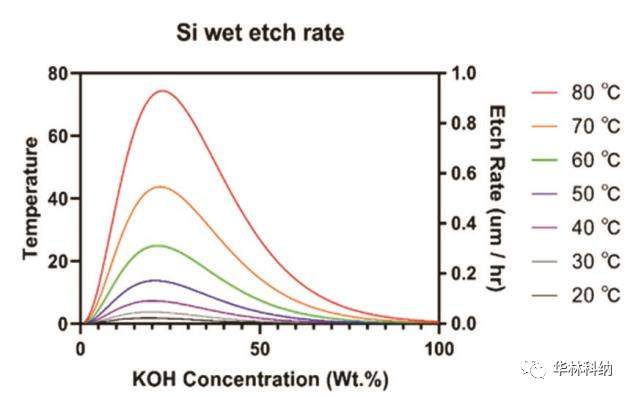
通過光敏抗蝕劑的濕蝕刻劑滲透
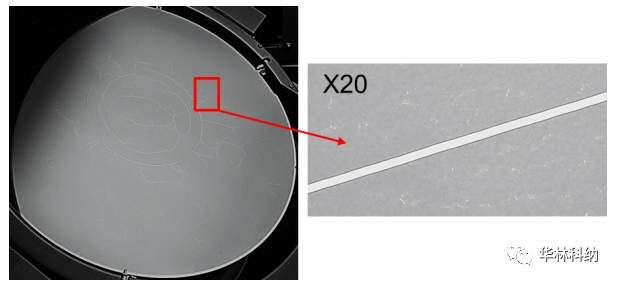
用于硅片減薄的濕法蝕刻工藝控制
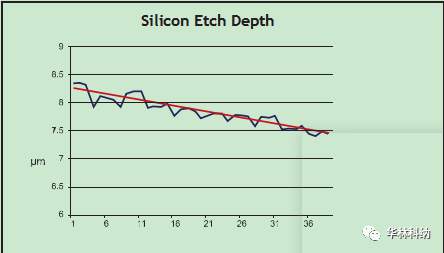
通過光敏抗蝕劑的濕蝕刻劑滲透研究
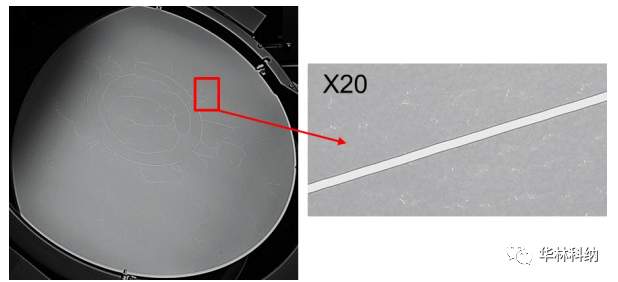
常見的各向同性濕法刻蝕的實際應(yīng)用
鍺化硅(SiGe)和硅(Si)之間的各向同性和選擇性蝕刻機制
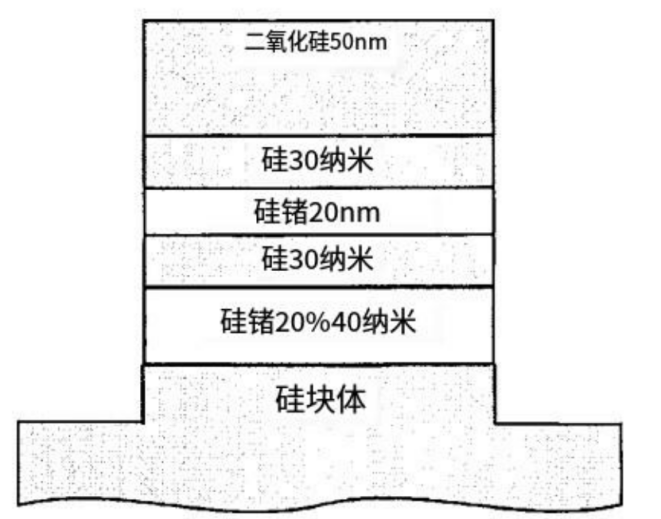
評論