隨著電子技術的迅速發展以及對便攜式產品需求的增加,隨身攜帶的醫療器械以及緊湊型和無線設備在醫院、醫療保健中心和急救車輛中變得越來越普遍。像這樣的小尺寸產品基于緊湊的PCB,其緊密間隔的數字和模擬電路彼此相鄰。
由于產品功能增加,緊湊型醫療電子設備的復雜性大大增加了PCB層數。隨著技術的進步,這些小型設備現在比其臺式機前身執行更多的電子功能。因此,執行信號路由的層數正在增加,以及其他功能。較新的緊湊型醫療設備通常需要包含10-12個PCB層的PCB,有時甚至更多。
設備萎縮
隨著設備大小的減小,層和路由變得更加復雜。有源器件的尺寸正在縮小,并采用先進的封裝,如球柵陣列(BGA)、四方扁平封裝(QFP)和芯片級封裝(CSP),增加了與小尺寸PCB相關的復雜性和難度。更多細間距BGA正被用于緊湊型醫療設備。MicroBGA 器件的間距范圍從 0.5 mm 到 0.3 mm 不等,這使得組裝過程極具挑戰性。
電阻器和電容器等無源器件也在不斷縮小。五年前,1206 和 0805 封裝類型被頻繁使用。如今,??s 0402 和 0201 封裝的物理尺寸是早期設備封裝的一半到四分之一。這些較小的封裝可實現更小的布局,但通過昂貴的拾取和放置、表面貼裝生產線和其他輔助返工站,使組裝變得困難,并且需要相當的精度。
一次通過產生預期
考慮到令人生畏的產品挑戰,PCB設計、制造和組裝過程變得非常復雜。因此,審慎的醫療電子OEM必須仔細審查一次通過的產量,以確定有多少產品通過。同樣,電子制造服務(EMS)提供商團隊必須接受第一次就正確進行設計,制造和組裝的口號。
一次通過良率對于緊湊型醫療電子設備的設計和組裝更為重要,原因很簡單,它們比大型產品更難制造和返工。一次通過良率過程在組裝和測試完成后進行。評估測試覆蓋率以確定故障率并執行故障分析。第一遍良率必須確保創建和應用正確的熱曲線,元件極性準確,不使用缺失或錯誤的元件,分配足夠的焊膏,并使用正確的助焊劑。
通常,原型水平的一次通過率應為75%或更高。然而,當涉及生命關鍵型產品時,醫療OEM廠商需要90%的一次通過率。這意味著經驗豐富的EMS提供商必須制定一個流程來定期審查設計和裝配數據,并進行必要的改進,以創造90%或更高的高一次通過率。
“一次通過產量”指標表示 EMS 提供商的 ??s 設計和裝配程序有多嚴格,以及為確保產品可靠性而實施的檢查和平衡的效率。
設計注意事項
醫療產品的裝配設計 (DFA) 在很大程度上依賴于多個團隊的互動。分配給給定PCB項目的設計,制造,裝配和組件采購團隊必須精確調整到項目的“??s”規范。設計工程師必須充分了解某些裝配方面,同樣,裝配工程師必須詳細了解項目‘??s設計的復雜性,例如自動放置和檢查問題以及返工要求。
這些團隊一起工作可以在根本原因級別處理和解決大多數問題。例如,如果設計團隊指定了一個組件,其延長的交貨時間為 12 周或更長時間,則采購團隊可以標記此問題并建議隨時可用的替換組件。
高效的DFA需要解決以下注意事項:
應在PCB布局階段全面部署足夠的測試點,以便在飛針或ICT測試或直接探測期間完全訪問和覆蓋。醫療設備測試需要多個冗余測試點來精確捕獲數據。如果需要,測試工程師通過訪問兩個或三個測試節點點來檢查此覆蓋范圍。
在制造電路板時,重要的是要考慮鑲板而不是一次制造一塊電路板。當電路板尺寸相對較小時尤其如此,例如30平方英寸或更小。這種鑲板(如圖 2 所示)提高了制造和裝配速度,從而降低了 OEM 成本。
在布局階段放置元件時,如果可能的話,謹慎的做法是使用電路板的一側而不是使用兩側。僅在一側使用組件可降低裝配和測試階段的非經常性工程成本。它還加快了拾取和放置機器上的組件放置,并減少了ICT或飛針的組件測試時間,從而節省了OEM的金錢和時間。僅將組件放置在頂部還可以減少返工、質量控制和調試時間,所有這些都可以降低裝配成本。
在PCB設計階段,出于DFA考慮,所有機械因素都應牢記在心,例如為PCB設計至少兩個(如果不是三個)安裝孔。此外,應設計每個有源元件的基準標記,并在電路板上的絲印上明確定義極化元件上的極性。這種做法消除了在組件放置、測試和調試階段可能出現的混淆,從而降低了生產成本。
在設計階段指定組件的硬件工程師應盡可能多地使用經過時間測試和驗證的組件。使用這些組件可減少調試和測試時間,并使醫療產品更加可靠和可預測。有效的DFA還要求使用常用的組件,其規格和功能已經在眾多其他系統應用中一次又一次地得到驗證。
另一個主要考慮因素涉及仔細監控與設備相關的特征和物理公差。以醫療產品的PCB制造過程中用于鉆孔的鉆機為例。鉆入PCB的鉆頭可以蜿蜒或徘徊。DFA要求在這方面保持嚴格的公差,特別是如果設計了更小的孔尺寸,例如8密耳或更小。此外,保持多個對稱組件的正確對齊也至關重要。如果涉及模塊化設計,則必須保持所有模塊相同,以便當IC放置在一個模塊中時,相似的IC將相同地放置在第二,第三,第四和后續編號模塊中。這對于小型且人口稠密的醫療產品尤其重要。
同樣,電阻和電容器網絡必須以類似的方式放置,以減少SMT機器編程和放置時間。在某些情況下,PCB可能大小不一或形狀奇特。因此,在DFA中一開始就明確了這一特定功能,以便在裝配過程中使用所需的夾具時,預先指定其局限性,以使裝配過程順利,更可預測和高效。
最后,設計、制造和裝配說明方面的詳細文檔是DFA的一個重要方面。這種嚴格的程序可確保在制造和裝配過程中正確執行設計的所有元素。如果涉及多個供應商,則準備充分的說明尤其重要;設計布局可以由一家公司執行,PCB制造可以由另一家公司執行,第三家公司進行組裝階段,第四家公司進行返工和測試。
混合信號設計
為了解決緊湊型醫療產品上混合信號設計的DFA問題,應確定明確定義和明確的策略,以便:
降低信噪比
根據元件位置正確定義電源和接地信號以及平面
屏蔽來自模擬段的高速數字信號
如果在布局時沒有采用這些DFA策略,則產品可能會產生不可接受的噪音水平,并需要重新設計,從而花費更多的時間,資源和金錢。
每個混合信號板設計都是不同的,需要專業混合信號設計人員和緊湊型醫療設備OEM之間的交互式設計談判。在PCB布局上設計混合信號元件時,某些考慮因素對于實現最佳性能至關重要。
混合信號設計非常困難,因為與數字元件相比,ADI器件具有不同的特性,例如不同的額定功率、電流和電壓標注、散熱要求和信號速度。因此,識別某些有問題的區域,然后在混合信號醫療設計中正確實施解決方案非常重要。
糟糕,更好,最好的布局
圖 3
混合信號電路的PCB放置是更重要的DFA點之一。首先,觀察錯誤的方法。如圖3a所示,模擬和數字接地層之間的中間存在分離,表現為L形或S形圖,走線穿過該分離。這是一個糟糕的布局,因為平面分離中的跡線不連續性和缺乏返回路徑會導致噪聲和交叉擾動。
缺少的是位于跡線下方的相應實體平面,以允許該跡線上的連續阻抗。此外,從模擬平面到數字平面的跡線交叉會阻止這些特定跡線的良好返回路徑。一個好的DFA設計應該在模擬和數字接地層之間保持分離平面的明顯分離,并在模擬分割平面下保持模擬跡線,在數字分割平面下保持數字跡線。否則,電路板上會產生噪聲并發出信號惡化。
理想情況下,電路板的模擬部分必須在放置、布線和平面創建方面完全隔離。此外,模擬走線應僅在其模擬基準電源或接地層以下運行。相反,數字走線應運行在具有相應電源和接地層的數字部分下,如圖3b所示。這樣可以保持阻抗恒定,并為信號提供良好的返回路徑。
然而,在某些情況下,由于PCB空間的機械和/或空間限制,完全的模擬和數字分離是不可能的。這里最好的方法是在單獨的層上運行模擬和數字跡線。如果各層之間沒有平面分隔,則經驗法則是垂直運行它們以保持信號真實性。但它們永遠不應該彼此平行運行。
圖 5
圖3c顯示了以模數轉換器(ADC)IC為例的最佳貼裝方法。IC的一側將模擬引腳正好放在模擬平面的頂部,而另一側的數字引腳正好位于數字平面上。
當分離與本ADC IC示例一樣精確和理想時,器件級的混合信號電路分離需要仔細的設計技術。以封裝在BGA中的混合信號器件為例。器件中的模擬和數字電路以約15密耳寬的間隙隔離,因此所有模擬信號和跡線都在模擬側,其對應的數字部分位于數字側。
堅固的設計
對更堅固性、高質量、更高可靠性和更好良率的需求都與緊湊型醫療電子設備有關。ISO 9001:2000 和 ISO 13485 等 ISO 標準為 EMS 公司提供了額外的資格,以符合這些要求,并允許他們向醫療產品 OEM 保證高標準的產品質量。這些產品制造不需要這些ISO標準;但是,它們可以為醫療設備OEM提供更大的產品質量和可靠性保證。
雖然遵循這些標準很重要,但通過關注DFA過程的細節來超越標準,對緊湊型設備設計的成功產生了最終的影響。嚴格的DFA方法可以節省成本和空間,從而為生命攸關的產品提供堅固的PCB設計。
審核編輯:郭婷
-
電路板
+關注
關注
140文章
5133瀏覽量
102622 -
PCB
+關注
關注
1文章
2097瀏覽量
13204
發布評論請先 登錄
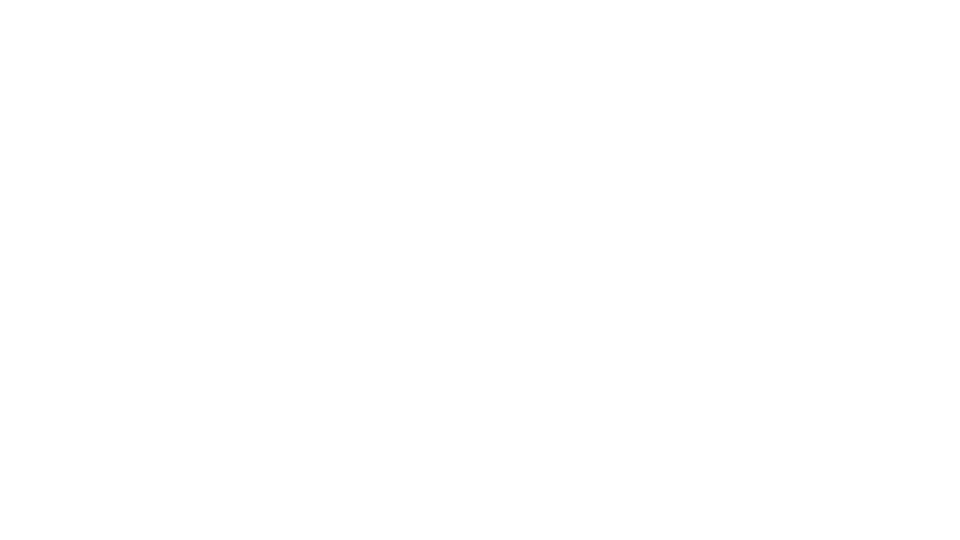
電子產品設計與調試
氣體腐蝕對電子產品的危害與應對
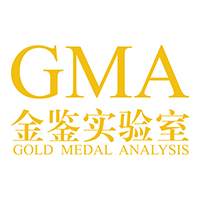
SMT技術:電子產品微型化的推動者
揭秘PoP封裝技術,如何引領電子產品的未來?
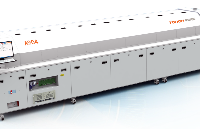
評論