降低廢氣排放是推動全球所有發動機制造商進行深入開發的動力,而提高噴油壓力則為顯著降低廢氣排放提供了可能。本文所介紹的Opel公司的試驗研究成果表明,噴油壓力提高到50 MPa幾乎能在整個發動機特性曲線場中實現顯著降低顆粒數排放的目標。
1提高噴油壓力的效果
在直噴式汽油機上,除了氣態排放物之外,排放的顆粒數(PN)也是一項重要的課題。近年來的研究表明,直噴式汽油機的噴油壓力已持續提高到目前的20~35 MPa。將噴油壓力提升到更高的數值將為降低廢氣排放帶來更大的提升潛力,但是燃油系統的部件及其在發動機和汽車上的集成已被發展到了技術極限,并對未來的開發提出了新的挑戰。
2燃油的霧化和蒸發
根據圖1所示的作用鏈,提高噴油壓力對燃油噴束效果的提升是非常顯著的。不斷提高的噴油壓力使從噴嘴頂端噴孔噴出的燃油噴束的出口速度更大,因此燃燒室中空氣與燃油噴束之間產生了更強烈的剪切力,引起的更大擾動產生了液相與氣相之間更為強烈的相互作用,從而改善了燃油的霧化效果。
圖1 提高噴油壓力對燃油霧化和
混合氣準備的效果
特別是大油滴的良好霧化對油滴尺寸譜和蒸發特性是非常有利的。霧化性能試驗已表明,更高的燃油噴束動量加大了其在燃燒室中的貫穿距(圖2上圖),但是在已有的燃油質量情況下不斷縮短的噴油時間補償了這類負面影響(圖2下圖)。
圖2 噴油時間恒定(上圖)和
噴油質量恒定(下圖)時
在20 MPa、32 MPa和50 MPa
噴油壓力下的燃油噴束投影圖
除了改善燃油霧化效果之外,更為強烈的渦流加快了周圍空氣與噴束錐體中飽和燃油蒸氣的混合,而且加速了剩余油滴的蒸發。圖3所示的噴束計算流體力學(CFD)模擬表明了油滴直徑減小與改善混合的綜合效果。噴油壓力的提高明顯改善了油滴的蒸發速率,再加上噴油時間縮短使得燃燒室壁面的潤濕現象得以顯著減少。
圖3 在20、35和50 MPa噴油壓力下
單個噴束在噴霧罐靜止空氣(25 ℃)
中蒸發燃油蒸發份額隨時間變化的CFD模擬
提高噴油壓力的另一個效果是因為更大的動量使得燃油噴束更為穩定,因此其受進氣流的影響較小。圖4示出了在進氣階段期間不同噴油壓力下的燃油噴射照片,其清晰地表明了這種效果。
圖4 在20MPa(左)、35 MPa(中)
和50 MPa(右)不同噴油壓力下的
燃油噴射狀況
3殘留在噴油嘴尖端上的燃油
通過在霧化和蒸發方面產生的有利效果,提高噴油壓力還可在噴油器關閉過程期間及后續工作過程中具備更多的優勢。在噴油器關閉時刻液相階段更大的動量使得更多的燃油脫離噴嘴尖端,并且還能減少燃油回流到噴嘴尖端,因此噴油器關閉過程結束后殘留在噴嘴尖端的燃油很少。此外,噴嘴內部更大的燃油動量使得噴嘴中的死容積易于排空而使燃油沿著噴油器針閥與閥座之間的密封面噴出。這兩種效果共同使得碳煙顆粒形成數量顯著減少,以此緩解了“噴嘴尖端積炭”現象,其效果如圖5所示。
圖5 在20MPa(左)、35 MPa(中)和
50 MPa(右)噴油壓力下
因“噴嘴尖端積炭”產生的類似火焰的發光現象
4壓力的產生
不言而喻,改善混合氣準備和降低顆粒數排放并非是無償的。為使有效體積流量Qe提高壓力Δp所必需的液壓功率Phyd可表達為Phyd = Qe×Δp,此外在最終的燃油泵功率估算中還需計入容積效率(ηV)和液壓機械損失(ηhm):Ppunp = Phyd/(ηV×ηhm)。因為燃油泵功率直接由發動機提供,提高噴油壓力會降低發動機的輸出功率。
在發動機額定功率(85 kW)的運行工況點(5 000 r/min)噴油壓力從35 MPa提高到50 MPa的情況下,額外的燃油泵傳動功率會使燃油耗增大約0.3%。在低部分負荷范圍(2 000r/min,0.2 MPa)內,額外燃油泵傳動功率約為30 W,那么在該運行工況點下燃油耗會增大約0.9%。
除了燃油泵在凸輪軸上消耗的扭矩平均值之外,燃油泵循環期間的最高值也是一個重要參數,其對燃油泵的傳動方案具有決定性的影響。對于給定的凸輪廓線與燃油泵柱塞直徑相組合,最大扭矩幾乎是與燃油泵輸出壓力成正比的,但是對于采用特定傳動方案的具體應用場合,柱塞直徑與凸輪升程能被優化到輸出所容許的最大扭矩。
5采用3缸1.0L基礎發動機作為試驗載體
本試驗研究項目在兩種不同的發動機方案上進行,其中一種發動機采用中置噴油器(CI),而另一種發動機則采用側置噴油器(SI)。這兩種發動機以3缸1.0 L-SGE(小型汽油機)增壓發動機(表1)為基礎,這種發動機被搭載于Adam、Corsa和Astra轎車系列,并多次在其他研究項目中用于試驗,其中CI發動機是一種量產機型,僅對其噴油系統進行了調整,下文將對此作詳細介紹。
針對SI發動機的調整首先需將噴油器安裝在兩個進氣門之間的側面位置,并相應匹配設計了燃油噴束,而火花塞則布置于燃燒室頂部空間的中間位置,此外進氣道和活塞設計需與燃燒過程相匹配。
表1 1.0 L-SGE 基礎發動機特性數據
1.0 L-Ecotech 渦輪增壓直噴式汽油機 | |
項目 | 參數 |
氣門傳動機構 | 4氣門,雙頂置凸輪軸,進排氣門可變氣門定時, |
排量/L | 0.999 |
最大扭矩/(N·m) | 165(1 800~4 500 r/min) |
最大功率/kW | 85(5 000~6 000 r/min) |
缸徑/mm | 74.0 |
行程/mm | 77.4 |
6噴油系統
用于SI和CI發動機的噴油系統及相關部件如圖6所示。這兩種噴油系統除了與用途密切相關的燃油噴束設計之外,所采用的噴油器是同一種,其分別與各自的燃燒室幾何形狀和進氣道流動狀況相匹配。
圖6 CI(左)和SI(右)噴油系統及其相關部件:油泵(a)、滾輪挺柱(b)、凸輪軸(c)、共軌(d)、PRV(e)、噴油器(f)、火花塞(g)和燃油噴束(h)
大陸公司的GHPi燃油泵能提供高達50 MPa的噴油壓力,它是由凸輪軸驅動的柴油泵的一種高級優質改型泵。因為該類燃油泵結構包含將多余燃油排入低壓側的非整體式閥門,并將一個外部的壓力調節閥(PRV)集成到系統中,燃油泵、燃油共軌、PRV和噴油器之間的所有連接管都是通過螺母緊固金屬密封的標準柴油管。
為了承受住不斷提高的液力負荷以及確保在系統壓力高于35 MPa的情況下使結構保持完善,為此應用了量產的鍛鋼柴油共軌,并且在共軌中插裝了進出油隔板,以便減小系統中的壓力波動。由大陸公司生產的測量范圍高達60 MPa的傳感器能有效測量系統燃油壓力。
所應用的大陸公司的XL5-35HP噴油器可通過各自的導管與燃油共軌相連接,以便能應用于CI和SI發動機。這些電磁閥式噴油器目前以用于3缸和4缸量產發動機的XL5-35HP噴油嘴為基礎,噴油壓力高達50 MPa的噴油器由針閥傳動機構的“隨意升程”方案進行控制。根據伯努利定律,該類噴油器的穩態流量相比量產方案已有所減小,在規定的噴射持續期情況下,50 MPa時的噴油質量與目前用于35 MPa-SGE發動機的噴油器相同。
7系統集成的挑戰
為了提高未來投產后的耐久性,系統中的一些部件需得以進一步開發,以確保對現有設計、制造和維修保養等方面的影響降至最小。
在噴油壓力提高后燃油泵及其由滾輪挺柱和凸輪軸的傳動需考慮到某些方面,為實現更高的噴油壓力必然會增大滾輪挺柱和凸輪之間的表面壓力,并在氣門傳動機構中產生了更大力矩。避免氣門傳動機構出現問題的一種可能性是將燃油泵位置移至附加的傳動軸上,但是該類措施可能會引起結構空間方面的問題并導致發動機整機質量的增加。
若能減小燃油泵柱塞力的話,則在噴油壓力提高的情況下使燃油泵的安裝位置依然保持在氣門傳動機構上。柱塞直徑從8 mm減小到6.5 mm就能使50 MPa與35 MPa時的柱塞力相近,而通過將柱塞升程從4 mm增大到6 mm即可使最大供油量保持不變。因為平均驅動扭矩會隨柱塞升程的增大而隨之提升,同時已附帶調整了凸輪廓線,以便將扭矩峰值降至最低。
在燃油共軌內部,逐漸提高的燃油壓力所產生的應力已達到了焊接材料的強度極限,因而要求其使用鍛鋼共軌。生產工藝的變化對生產布局、儲備時間和生產廠址的靈活性有較大的影響,因此需在開發過程中予以考慮,同時鍛鋼共軌也帶來了允差方面的優勢以及具有例如提高剛度等方面的設計特點,以此會對噪聲和振動的開發產生正面效果。
系統燃油壓力提升后需重點注意高壓回路的密封。當今常用的O形圈密封僅是用于最高壓力為35 MPa條件下的一種技術方案,而眾所周知的柴油機所使用的螺母緊固金屬密封可承受超過200 MPa的壓力負荷,因此該類密封方案未來也可應用于直噴式汽油機。
8提高噴油壓力對顆粒排放及尺寸的影響
上文所述的效果能顯著降低顆粒數排放。圖7示出了具有代表性的2 000 r/min和0.7 MPa(pme)運行工況點的情況。左圖示出的是采用先進的AVL 489顆粒計數器采集的顆粒數排放與燃油壓力的關系。顯然,采用35 MPa的噴油壓力就能使顆粒數排放顯著降低,而將噴油壓力進一步提高到50 MPa即可繼續獲得顯著的提升潛力。
圖7 提高噴油壓力對顆粒數排放(左)及其顆粒尺寸分布(右)的影響
噴油壓力從20 MPa提高到50 MPa對顆粒尺寸分布的影響如圖7右圖所示。該類數據是采用供燃燒分析使用的能識別最小顆粒尺寸為5 nm的DMS 500快速顆粒分析儀采集的,并統一以20 MPa曲線的最大值為基準來計算相對顆粒濃度。除了由曲線下方面積所表示的顆粒數總體減少之外,從這張圖線中曲線形狀所示的濃度即可清楚地看出提高噴油壓力的第二種效果。從20 MPa開始,該數據顯示出了一種具有25 nm和100 nm的雙峰分布模式。100 nm的范圍會隨著噴油壓力的提高明顯減小,以此可燃混合氣準備的改善(見圖4)和“噴嘴尖端積炭”的減少(見圖5)大幅減少了大顆粒的形成,這對于減少排放的顆粒質量有明顯的效果,同時尺寸在25 nm左右的顆粒數也有所減少,該現象表明全范圍內低至5 nm顆粒尺寸的數目均有所減少。
9穩態運行工況點和燃油耗影響
基于針對噴油始點(SOI)優化的標定,兩種發動機的整個特性曲線場可在所有的穩態運行工況點進行35 MPa和50 MPa顆粒數的排放性試驗。圖8中的試驗結果表明了提高噴油壓力以降低顆粒數排放的效果,其中上圖為SI發動機的試驗結果,下圖為CI發動機的試驗結果。噴油壓力提高到50 MPa后幾乎可在整個特性曲線場中顯著降低顆粒數排放,其中每種情況下降低顆粒數排放的峰值約在60%,即使在高轉速高負荷情況下其優勢也是較為顯著的,僅在低轉速低負荷的小范圍內提高噴油壓力后并未顯示出在顆粒數排放方面的優勢,因為在該范圍內于35 MPa時的廢氣排放已處于較低的水平。
圖8 SI和CI發動機噴油壓力從35 MPa提高到
50 MPa后穩態運行條件下顆粒數排放的降低
總體而言,提高噴油壓力對有效比燃油耗(BSFC)的影響通常較小,它處于燃油效率的測量精度范圍內,各種運行工況點的最大有效比燃油耗缺陷局部大約會超過1%,這些精度范圍處于較高負荷直至全負荷。在這次試驗中尚未發現在穩態運行條件下出現明顯的燃油耗缺陷。
10總結
本文詳細分析了增壓直噴式汽油機噴油壓力提高到50 MPa后的運行效果,針對技術挑戰的分析概括了開發過程中所需采取的相關步驟,而在量產開發方面并未遇到技術挑戰,但是尚無法排除在發動機設計方面會有所調整。
噴油器采用側置或中置的發動機試驗研究均表明,噴油壓力從35 MPa提高到50 MPa在降低炭煙顆粒排放方面具有顯著的效果,兩種噴油器位置在某些運行工況點的顆粒數排放的降低幅度均可降低超過60%,而通過減少大顆粒的形成數量還能降低顆粒排放,除此之外尚存的問題是燃油耗隨之提升,該現象歸因于噴油壓力提高后混合氣準備過程的改善以及由此提高的燃油效率,其補償了燃油泵驅動功率的增加。
目前市場上所使用的35 MPa噴油系統已充分利用了提高噴油壓力以降低顆粒數排放的大部分開發潛力。正如本文所述,更高的噴油壓力還可大幅降低顆粒數排放。當前,發動機技術的發展受到電氣化和汽油顆粒捕集器的影響,但卻會因此提高成本和復雜性,但是目前采用50 MPa燃油系統并非用作改善成本效益的解決方案而是用于降低顆粒數排放。法規邊界條件的進一步嚴格化與發動機廢氣后處理的復雜化可能會成為日后發展的焦點所在,而對原始廢氣中顆粒數與整機技術費用之間進行的權衡表明,未來有必要進一步提高噴油壓力。
好文推薦
輪邊電驅動 ——提高空間利用效率和行駛動力性之路
在著火運轉汽油機上測量活塞裙部幾何形狀對摩擦功率的影響
用于自動駕駛的方向盤造型改良方案
日本近年柴油機發展現狀研究綜述
用于48V汽車電路的電輔助渦輪增壓器
用于高效電動車的創新的高速動力傳動系統方案
點擊公眾號首頁菜單“搜索”中的“歷史信息”即可查閱更多“好文推薦”哦O(∩_∩)O
原文標題:好文推薦 | 直噴式汽油機噴油壓力提高到50MPa的相關研究
文章出處:【微信公眾號:汽車與新動力】歡迎添加關注!文章轉載請注明出處。
-
功率
+關注
關注
14文章
2101瀏覽量
71193 -
柴油機
+關注
關注
1文章
173瀏覽量
26689 -
汽油機
+關注
關注
0文章
58瀏覽量
11694
發布評論請先 登錄
怎么設計基于FPGA的電控汽油機噴油脈寬處理系統?
運用CPLD器件和AT89C52實現汽油機點火參數測量儀的設計
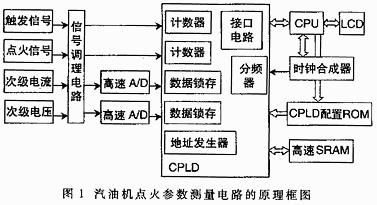
評論