在工程機械行業的裝配車間,曾經戴著老花鏡、拿著游標卡尺反復測量液壓閥體尺寸的質檢老師傅,見證了質檢方式的巨大轉變。如今,一組高速運轉的攝像頭和智能算法,徹底改寫了持續半個世紀的質檢模式。當全球知名重工企業宣布智能工廠質檢準確率達到 99.98% 時,我們看到了傳統制造業數字化轉型的強大力量。
一、比 “火眼金睛” 更厲害的智能視覺
在直徑 2 米的齒輪箱檢測工位,32 組工業相機以每分鐘 2000 次的速度進行高速掃描。這些相機就像 “超級眼睛”,配備的微距鏡頭能捕捉到 0.02mm 級的加工瑕疵,精度相當于人類頭發絲的四分之一 。而且,多光譜成像技術讓它們不僅能發現表面缺陷,還能 “看穿” 金屬內部的結構性損傷。
深度學習算法經過百萬級缺陷樣本的 “訓練”,已經能夠準確區分 27 類常見機加工缺陷。在法蘭盤檢測環節,AI 系統僅需 0.8 秒就能完成過去人工需要 15 分鐘的檢測流程,還能發現人工難以察覺的漸變式磨損。可以說,智能視覺突破了肉眼的極限,讓微小瑕疵無所遁形。
二、智能質檢系統的三次 “進化”
動態學習:快速適應新材料
當新型復合材料應用到生產中,質檢系統展現出強大的學習能力。它通過動態學習機制,在 48 小時內就完成了材料特性的自主學習。借助遷移學習技術,原有模型在新材質上的識別準確率,一周內從 82% 提升至 98.5%。這徹底改變了傳統視覺檢測需要反復調整參數的麻煩,讓質檢系統能夠快速適應新變化。
多模態數據融合:全方位精準判斷
在焊接質量檢測單元,智能質檢系統不再只依靠視覺。它同步分析熱成像數據、聲波震動信號和視覺特征,通過多維度數據交叉驗證,將虛警率控制在 0.15% 以下。這種綜合判斷能力,能準確識別出肉眼不可見的虛焊問題,大大提高了檢測的準確性。
預測性質量干預:提前避免損失
在數控機床加工環節,系統實時采集振動數據和刀具溫度信息。憑借這些數據,它能在產品出現瑕疵前 3 - 5 分鐘發出預警。這種預防性質檢模式,將次品率從 0.7% 降至 0.05%,每年為企業避免上千萬元的材料損耗,實實在在地節省了成本。
三、智能質檢的四大 “高光時刻”
復雜曲面檢測:難題迎刃而解
液壓缸體的異形曲面檢測曾是個大難題。研發團隊開發的曲面展開算法和三維點云重構技術,把復雜曲面轉化為二維平面進行檢測,使曲面瑕疵識別率從 68% 提升至 99.2%,讓復雜形狀的產品檢測不再困難。
微小部件批量檢測:效率大飛躍
在標準件檢測線上,微型視覺模組配合震動供料系統,每分鐘能自動篩檢 600 個螺栓。圖像拼接技術的應用,讓螺紋檢測效率提升 40 倍,人力成本降低 90%,實現了微小部件的高效檢測。
夜間生產:品質始終如一
引入紅外增強視覺系統后,即使在昏暗環境下,檢測準確率也能從白天 92% 的波動區間,穩定在夜間 98.5% 以上,保證了工廠 24 小時生產的品質都在線。
供應鏈質量協同:上下游共贏
將檢測標準數字化后,上游供應商可以實時獲取質量反饋。某鑄造廠接入系統后,毛坯件合格率三個月內從 85% 提升至 97%,來料檢驗時間也縮短了 40%,實現了供應鏈的質量協同提升。
四、人機協作:打造質檢 “夢之隊”
在智能工廠的 “質檢指揮中心”,經驗豐富的老師傅們轉型成為 AI 訓練師。他們通過標注特殊案例、優化檢測邏輯,幫助質檢系統不斷提升智能水平。這種 “人類經驗 + 機器智能” 的協作模式,讓質檢系統每月能迭代升級 2 - 3 個版本,實現了優勢互補。
五、更智能的質量管理
隨著 5G 技術的應用,分布式質檢節點實現了云端算力共享。通過邊緣計算設備,核心算法下沉到車間層級,檢測響應時間縮短至 50 毫秒。質量數據區塊鏈系統的建立,讓每個零部件的檢測記錄都可追溯、不可篡改,為質量管理提供了更可靠的保障。
當最后一臺傳統檢測設備被移出車間,“質量是生命線” 的標語有了新的含義。這場始于視覺革命的質檢變革,正在重塑現代制造業的質量管理體系。從精確測量到預測維護,從單點檢測到全鏈協同,智能制造時代的質量管控已經突破物理邊界,一個數據驅動的品質新生態正在形成。
-
設備管理
+關注
關注
0文章
142瀏覽量
9473 -
智能制造
+關注
關注
48文章
5816瀏覽量
77443 -
智能工廠
+關注
關注
3文章
1063瀏覽量
43056 -
數字化工廠
+關注
關注
1文章
70瀏覽量
6379 -
智能車間
+關注
關注
0文章
14瀏覽量
3119
發布評論請先 登錄
廣電計量出席人工智能賦能先進制造業技術論壇
AI和ML如何重塑電子制造業
自動點焊機批發廠商:引領制造業智能化轉型的隱形冠軍
安寶特方案:AR助力制造業安全巡檢智能化革命!

AR助力制造業安全巡檢智能化革命!
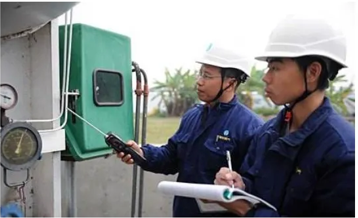
智能工廠 VS 傳統工廠:制造業的“新舊對決”
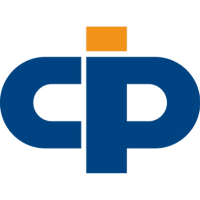
智慧工廠:制造業數字化轉型的新引擎
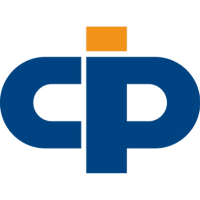
評論