來源:《航空制造技術》2014年07期,作者:王榮橋、胡殿印、申秀麗、樊江
航空發動機是典型的多學科交叉、多部件強耦合的復雜工程系統,在高溫、高壓、高轉速、多場載荷/環境下工作,又要滿足推力大、重量輕、壽命長、高可靠性等極高使用要求,是一種極限產品,研制難度巨大。轉子結構作為航空發動機的核心部件,其結構完整性和可靠性是航空發動機設計的最薄弱環節,是制約發動機研發的瓶頸。
一方面,結構系統經受嚴酷且復雜多變的氣動、機械和熱載荷,同時力學(氣-熱-固)與材料、工藝等學科相互作用和制約;另一方面,結構壽命表現出很大的分散性,而安全飛行又要求低的失效概率。這時,傳統的確定性設計技術面臨諸多挑戰,概率設計作為一種精細設計手段,可以量化風險,在滿足可靠性要求的前提下能夠減輕重量、降低成本,是解決先進航空發動機研制瓶頸的最有潛力的關鍵技術之一。
發動機結構設計發展
航空發動機結構設計經歷了靜強度設計、安全壽命設計、確定性損傷容限設計與結構概率設計的發展過程。
靜強度設計的主要出發點是結構在給定設計載荷作用下不發生破壞;經使用載荷作用,卸載后沒有可見的永久變形。在過去相當長時間內,由于發動機載荷較小,結構的應力水平很低,對結構壽命的要求也不高,靜強度設計能夠滿足設計要求。
1954年英國“彗星”號噴氣式客機連續發生爆炸墜海事故,事故原因是由于飛機機身金屬結構出現疲勞效應而產生的斷裂破壞所造成的。這說明,按照靜強度設計結構件,并不能保證其使用安全,在結構設計中必須考慮安全使用壽命問題。在事故發生之后,航空發動機結構設計開始采用了安全壽命方法。
安全壽命設計的前提是假設結構是無缺陷的連續均勻體。由于材料具有一定的分散性,工程中結構設計往往通過試驗確定結構的平均壽命,并結合經驗給定一個較大的分散系數,進而得到結構的許用壽命。
英國國防部標準(DEF STAN 00-971)中要求,取可靠度為99.87%(即-3σ)的曲線作為安全壽命對應的S-N曲線。美國航空渦輪噴氣和渦輪風扇發動機通用規范(MIL-E-5007D)中規定:發動機典型結構采用安全壽命設計,材料容許的強度與壽命特性以-3σ為基礎,相應的置信度為95%,見圖1。
民機方面,美國聯邦航空局(FAA)頒布的適航條款FAR33.14,要求壓氣機、渦輪盤等轉子件的壽命制定采用安全壽命設計方法;歐洲聯合航空局的適航規章JAR-E也規定發動機轉子件要通過安全壽命方法來確定壽命。
安全壽命設計方法考慮了發動機結構材料力學性能的分散性,并從概率角度制定了很高的可靠度,以確保結構服役過程中的安全性。然而實際結構中必然含有夾雜物、孔洞(裂紋)、空穴等初始缺陷,因此,安全壽命設計方法并不保證結構安全可靠;
另外,安全壽命設計是一種非常保守的設計方法,在目前采用的95%置信度及99.87%可靠度情況下,可能出現1000個結構中只要1個出現規定的裂紋,其它999個也被認為達到了疲勞壽命,從而退出服役,造成了極大的浪費。據估計,采用安全壽命方法設計的輪盤在報廢后仍有超過80%的盤具有10倍甚至更多的壽命,因此需要發展更經濟的設計和評估方法。
確定性損傷容限設計可解決發動機結構設計中的安全性和經濟性問題。該方法與安全壽命設計法不同,假設材料存在缺陷或微小裂紋,并且在疲勞載荷作用下會逐漸擴展,最終導致結構的失效。確定性損傷容限設計依據結構的使用條件、材料性能和維修要求確定結構的檢修周期和最大的裂紋容許尺寸,把結構材料缺陷和損傷擴展控制在合理的范圍之內[7],有效地提高了發動機結構使用維護的經濟性。
美空軍發動機結構完整性大綱(MIL-STD-1783)中明確指出,對發動機斷裂關鍵件應進行損傷容限設計、試驗和控制,以確定結構的檢修周期。然而,確定性損傷容限設計方法難以準確考慮各隨機因素對壽命分散性的影響,不能準確預估結構的失效概率以及輸入參數的靈敏度。
上述發動機結構設計過程中所研究和建立的準則、規律及方法均是確定性的,即材料性能、制造工藝、任務用法以及其他參數使用確定值,不能準確預估結構的疲勞壽命,因而難于在結構重量、使用壽命及設計準則等方面進行優化和平衡,也無法給出定量的可靠性指標。帶可靠度的壽命要求是現代發動機設計的顯著特點,而結構概率設計是保證結構可靠性的重要設計手段。
結構概率設計方法認為,作用于結構的真實外載荷及結構的真實承載能力,都是概率意義上的量,設計時不可能予以精確的值,稱為隨機變量或隨機過程,它服從一定的分布。以此為出發點進行結構設計[10],能夠更好符合客觀實際。美國在綜合高性能渦輪發動機技術計劃(IHPTET)研究中,提出了概率設計方法并建立了轉子系統的概率設計系統(PDS),使結構設計儲備降到可接受的可靠度水平,并保證安全性和工作能力的相對平衡,見圖2。
繼IHPTET計劃后,推出的多用途經濟可承受先進渦輪發動機計劃(VAATE)將葉片的概率高循環疲勞(Probabilistic High Cycle Fatigue)作為關鍵技術之一。美國的發動機結構完整性大綱(MIL-HDBK-1783B)中也指出,用概率設計裕度代替傳統的安全系數或確定性裕度能更準確地表示構件響應的變化。美國FAA推動了結構概率設計在民用航空領域的應用,以適航條款FAR33.70替代FAR33.14,即針對發動機壽命限制件進行概率損傷容限設計,通過與設計目標風險比較,確定其失效風險等級。
為滿足先進航空發動機性能要求,越來越多的新材料如粉末合金、金屬間化合物、陶瓷材料、復合材料等不斷出現。這些材料在某些性能如強度、應力、密度等方面較傳統金屬合金有明顯的改善,但是其材料屬性存在許多不確定性因素和新的失效模式,采用確定性設計方法將產生較大的偏差。因而,對新材料、新結構、新工藝體系下的發動機典型結構更需要采用概率設計方法。
發動機典型結構概率設計關鍵技術
1. 隨機因素概率模型
(1)載荷分散性
航空發動機尤其是軍用發動機要完成巡航、簡單特技、復雜特技、編隊、攻截擊等大量的飛行任務,導致發動機結構的工作載荷,如機械載荷、氣動載荷、溫度載荷存在很大分散性。發動機載荷概率模型的建立需結合載荷譜處理技術,研究發動機載荷譜與結構載荷譜等損傷轉換原則,通過發動機外場飛行載荷譜、試車譜的收集和處理,獲得發動機典型結構的載荷隨時間的變化規律,并利用統計理論建立發動機典型結構的工作載荷概率統計特征。
(2)材料分散性
發動機結構材料在制備過程中的差異性導致材料力學性能參數(例如彈性模型、泊松比、應力-應變曲線等)存在分散性;同時,發動機典型結構由于加工工藝復雜性造成結構不同部位材料性能也存在顯著差別。因而,需要結合材料標準試件、結構不同部位特征模擬件試驗數據建立經試驗驗證的概率模型。
例如,對材料循環應力-應變關系的分散性處理,可將應變分解為彈性應變分量和塑性應變分量,分別建立彈性應變分量、塑性應變分量與應力的線性方程,并對上述方程進行隨機化處理,通過回歸方法建立循環應力-應變的概率型,見圖3。
(3)工藝分散性
工藝分散性是指由于材料制備、加工手段、檢測技術等隨機因素引起的結構分散性。
初始缺陷隨機性。針對鍛壓、鑄造、熱等靜壓等材料制備方法,導致材料內部的夾雜、孔洞、空穴等初始缺陷的數量、位置、尺寸均具有隨機性,見圖4。因此,需要發展表面/亞表面/內部缺陷的等效損傷表征方法,并建立發動機典型結構分區域的缺陷概率模型。
幾何尺寸隨機性。機械加工工藝不穩定造成發動機典型結構的幾何尺寸具有隨機性。為此,需要通過靈敏度分析確定發動機典型結構的關鍵幾何尺寸參數,并對關鍵幾何尺寸進行統計,建立其概率分布特征。
殘余應力隨機性。發動機結構表面處理技術(如噴丸強化、激光強化)、熱處理技術(如固溶、時效)和其他工藝(如線性摩擦焊、電子束焊接)等加工工藝不穩定性,導致結構表面、內部存在隨機的殘余應力。殘余應力的概率模型需經由數值模 擬、工藝檢測與數理統計結合進行系統研究。
缺陷檢測技術隨機性。不同檢測技術導致最小可檢缺陷的尺寸、位置等均具有隨機性,引入缺陷檢出概率(Probability of Detection,POD)來描述這種隨機性。通過制備包含足夠缺陷種類、尺寸、位置的損傷試件,開展缺陷的檢測試驗并建立檢測數據的數學模型,統計處理獲得檢測技術的POD曲線。
2. 發動機典型結構
發動機典型結構(如渦輪盤葉結構)承受氣-熱-固多場復雜交變的載荷/環境,其失效模式多為復合疲勞失效,如疲勞-蠕變、熱機械疲勞、高低周復合疲勞等。因此,建立在試驗基礎上的復雜載荷/環境下發動機典型結構復合疲勞失效概率模型成為發動機結構概率設計的關鍵技術。需要通過理論研究與試驗驗證緊密結合,揭示復雜載荷/環境下發動機典型結構復合失效模式機理并發展相應的復合疲勞壽命預測方法,結合載荷、材料、工藝分散性,建立經試驗驗證的發動機典型結構復合疲勞失效概率模型。
北京航空航天大學結構強度及多學科優化課題組以WP7發動機高壓渦輪盤(材料為GH33)為對象,研究并發展一套從材料特性到設計應用全過程的、包含裂紋形成和裂紋擴展兩個損傷階段的、經過試驗驗證的渦輪盤疲勞-蠕變耦合失效模式的概率模型和設計方法(圖5) 。
3. 結構概率響應分析技術
發動機典型結構概率設計涉及的學科多、結構復雜,直接采用數值方法進行結構失效概率/可靠度求解將導致計算時間過長。因此,建立結構概率響應分析方法是發動機典型結構概率設計的一個關鍵技術。
目前,多采用響應面與蒙特卡羅法相結合的技術進行結構概率響應分析,制定出一套適合發動機典型結構的高效率高精度概率響應分析方法,以解決結構概率分析中海量計算量等問題。可采用拉丁超立方法、擬蒙特卡羅法、拉丁重心抽樣、重要抽樣等抽樣方法;可選取神經網絡、Kriging模型、支持向量機等近似建模方法(圖6)。
4. 隨機因素靈敏度分析
通過隨機因素的靈敏度分析,一方面可確定影響結構壽命分散性的主要因素,為發動機典型結構概率設計提供設計依據;另一方面,可將結構概率設計中靈敏度指標低的隨機變量處理成確定性參數,從而節省計算時間,提高求解效率;集中研究主要隨機因素的分散性對于提高結構失效概率/可靠度的求解精度較其他因素更直接、顯著。
5. 發動機典型結構概率設計系統
針對我國航空發動機材料工藝體系,建立具有自主知識產權的航空發動機典型結構概率設計平臺也是發動機結構概率設計的關鍵技術。發動機結構概率設計平臺的實現需要進行大量的迭代計算,每一次計算過程中幾何模型的變化都會引起網格、邊界條件等分析數據隨之變化。因而,幾何模型和分析模型之間的連接技術、網格自動重構和自動加載等技術是需要解決的技術難點。
例如,北京航空航天大學結構強度及多學科優化課題組利用虛擬塊代替復雜幾何結構建立靈活的多塊網格,引入隨動點的約束實現優化迭代中幾何結構的網格重構,解決了渦輪葉片多學科優化(MDO)過程中高精度網格問題,見圖7。
北京航空航天大學結構強度及多學科優化課題組在國防973計劃支持下,在渦輪盤確定性設計流程的基礎上,提出并建立了渦輪盤概率設計流程,初步建立了國內第一個渦輪盤結構概率設計系統(TPDS)。包含載荷譜處理、隨機變量處理、幾何建模、失效模式分析和設計決策等主要功能,并集成了如UG、ANSYS、MATLAB等商業軟件,見圖8。
需深化研究的幾個方面
發動機典型結構概率設計技術成為解決先進發動機研發瓶頸的最有潛力關鍵技術之一,在國內正逐漸用于先進航空發動機關鍵件的研制,局部得到了應用,效果初顯。在下一步發展中,下列研究工作需要深化和加強。
1. 材料-工藝-結構概率一體化設計
結構設計、材料、工藝融合迭代是提高先進航空發動機研制水平的根本路徑。發動機結構概率設計技術的有效應用更是離不開材料、工藝的一體化考慮。因此,發動機結構概率設計需要從設計源頭出發,揭示典型結構制造敏感參數對發動機結構可靠性的影響機制與規律調控,形成融合制造敏感參數的發動機典型結構概率設計方法,從而建立發動機材料-工藝-結構概率一體化設計理論與方法。
2. 基于可靠性的多學科優化設計
航空發動機結構設計涉及氣動、材料、傳熱、結構、強度等諸多學科,學科之間相互耦合,單個學科上的概率設計并不能保證設計出來的結構滿足使用可靠性要求[37-38]。未來的發動機結構設計將以多學科耦合設計為基礎,多學科優化和概率設計相結合,充分考慮各種不確定性因素對結構性能指標的影響,發展完善基于可靠性的多學科優化設計方法,得到多學科、多目標的平衡折衷[39],解決我國先進航空發動機典型結構的設計瓶頸。
3. 發動機典型結構概率設計
發動機典型結構大多存在多種失效模式,且失效模式之間是相關的。失效相關性主要有兩種:一是共因失效相關性,如溫度是高溫疲勞、高低周復合疲勞等典型失效模式的共同因素;二是耦合失效相關性,如疲勞-蠕變、高低周疲勞、熱機械疲勞等耦合失效模式。在發動機典型結構概率設計中,也需建立考慮失效相關的結構概率分析模型和處理方法。
4. 結構概率設計數據庫的建立
制約結構概率設計技術在先進航空發動機研制中推廣應用的核心因素是缺乏材料、工藝和使用中數據的長期積累和有效管理。同時,發動機典型結構的概率設計方法包括其中用到的隨機因素概率模型、失效模式概率模型等必須經過大量的試驗驗證才能實現有效的工程應用。因而,必須發展和建立發動機典型結構概率設計數據庫,不斷積累寶貴數據,并與發動機概率設計平臺有機融合使用,為發動機結構概率設計提供數據支撐。
結束語
發動機結構概率設計可量化風險,在滿足可靠性要求的情況下減輕重量,是解決先進航空發動機研發瓶頸的最有潛力的關鍵技術之一。結構概率設計正逐漸用于我國先進航空發動機關鍵件的研制,局部得到了應用,效果初顯。結構概率設計與材料工藝、多學科優化相結合是未來的發展方向。
《航空制造技術》2014年07期
作者本人免費下載|收藏|投稿|?論文排版
-
發動機
+關注
關注
33文章
2529瀏覽量
70587 -
材料
+關注
關注
3文章
1319瀏覽量
27712 -
航空發動機
+關注
關注
0文章
62瀏覽量
11192
原文標題:北航:航空發動機典型結構材料-工藝-結構概率設計技術
文章出處:【微信號:AMTBBS,微信公眾號:世界先進制造技術論壇】歡迎添加關注!文章轉載請注明出處。
發布評論請先 登錄
航空發動機噴嘴流量分布實驗裝置的研究
基于多元聯合熵的航空發動機性能分析
基于多元聯合熵的航空發動機性能分析
航空發動機試車臺噪聲聲功率譜技術研究
航空發動機控制系統
基于PC104的航空發動機試車參數檢測系統研究[圖]
中國為何做不出航空發動機?
航空發動機反推力裝置有哪些
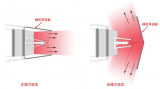
我國航空發動機如何突破技術瓶頸?
航空發動機噴流噪聲近場測試研究
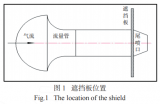
航空發動機的關鍵材料有哪些
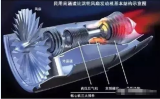
航空發動機研制中數值仿真技術的戰略地位及國內外發展概覽
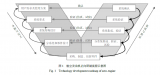
評論