共讀好書
王磊,金祖?zhèn)ィ瑓鞘烤辏櫼X晶晶,曹純紅
(中科芯集成電路有限公司)
摘要:
基于焊點(diǎn)預(yù)測仿真軟件 Surface Evolver 對不同焊盤設(shè)計(jì)的球柵陣列( BGA ) 封裝焊點(diǎn)的回流形態(tài)進(jìn)行預(yù)測。模擬不同回流焊的冷卻速率與焊盤設(shè)計(jì)對焊點(diǎn)的殘余應(yīng)力和基板翹曲的影響。根據(jù)正交試驗(yàn)和灰色關(guān)聯(lián)分析法對結(jié)果進(jìn)行分析優(yōu)化。結(jié)果表明,優(yōu)化后的焊點(diǎn)芯片側(cè)的殘余應(yīng)力降低了 17.9%,PCB 側(cè)的殘余應(yīng)力降低了 17.1%,其翹曲值為 68.867 μm。
1 引言
隨著封裝技術(shù)的發(fā)展,芯片封裝逐漸向復(fù)雜、高密度的 2.5D、3D 封裝發(fā)展。系統(tǒng)級封裝(SiP)在傳統(tǒng)封裝的基礎(chǔ)上,提升功能密度,縮短互連長度,進(jìn)行系統(tǒng)重構(gòu),在一定程度上緩解了芯片集成的壓力。然而隨著集成度的增加,芯片的尺寸、引腳數(shù)量都在增加,設(shè)計(jì)難度提高,工藝成品良率降低,導(dǎo)致潛在的工藝制程風(fēng)險(xiǎn)增加 [1-2] 。球柵陣列(BGA)封裝的焊點(diǎn)在保證SiP 互連電性能的前提下,也承擔(dān)著機(jī)械可靠性的功能。由于焊點(diǎn)、基板、PCB 這一互連結(jié)構(gòu)之間的熱膨脹系數(shù)(CTE)存在差異,工藝過程中的熱應(yīng)力會(huì)導(dǎo)致BGA焊點(diǎn)產(chǎn)生較大的殘余應(yīng)力以及基板翹曲等問題 [3] 。
對此,胡少華 [4] 研究了在不同回流冷卻速率下焊點(diǎn)結(jié)構(gòu)對封裝殘余應(yīng)力的影響。田文超等 [5] 研究了陶瓷封裝陣列焊點(diǎn)的結(jié)構(gòu)參數(shù)對焊點(diǎn)回流焊應(yīng)力應(yīng)變的影響。GE 和 NJOKU 等 [6-7] 研究了焊點(diǎn)高度對芯片長期可靠性的影響。張浩敏等 [8] 研究了殘余應(yīng)力對 BGA焊點(diǎn)可靠性的影響。以上研究結(jié)果表明,焊點(diǎn)高度、焊盤直徑、回流冷卻速率對焊點(diǎn)的殘余應(yīng)力均有顯著影響,同時(shí)較大的殘余應(yīng)力容易導(dǎo)致器件的焊盤坑裂。
本文針對不同的焊盤設(shè)計(jì)參數(shù),采用 SurfaceEvolver 軟件對 BGA 焊點(diǎn)進(jìn)行形態(tài)預(yù)測。同時(shí)以 40×40 面陣列 BGA 焊點(diǎn)的 SiP 封裝為研究對象,分析其芯片側(cè)、PCB 側(cè)的焊盤設(shè)計(jì)與回流冷卻速率對焊點(diǎn)回流殘余應(yīng)力以及基板翹曲的影響。用正交試驗(yàn)和灰色關(guān)聯(lián)法進(jìn)行優(yōu)化設(shè)計(jì),找出最優(yōu)參數(shù)組合進(jìn)行驗(yàn)證,為提高大尺寸陣列 SiP 封裝的設(shè)計(jì)優(yōu)化提供數(shù)據(jù)參考。
2 SiP 封裝模型建立
2.1 BGA 焊點(diǎn)形態(tài)預(yù)測
根據(jù)熱力學(xué)基本定律,自然界中任何封閉系統(tǒng)的存在總符合能量最小原理。因此在回流穩(wěn)態(tài)后,熔融的 BGA 焊點(diǎn)(液相)與對流熱空氣(氣相)和上下基板焊盤(固相)組成的系統(tǒng)處于能量最小的狀態(tài)。單個(gè)BGA 焊點(diǎn)的系統(tǒng)能量 E 是表面勢能 E S 、焊點(diǎn)自身重力勢能 E G 和外力作用勢能 E f 之和,即
式中 v 為焊點(diǎn)表面張力,A 為焊點(diǎn)的自由表面積,d 為BGA 焊點(diǎn)密度,g 為重力加速度,z 為焊點(diǎn)高度坐標(biāo),V為焊點(diǎn)體積,F(xiàn) 為作用在 BGA 焊點(diǎn)上的壓力,h 為焊點(diǎn)高度。
表面勢能總和 I 以泛函數(shù)形態(tài)描述為:
式中 λ 是拉格朗日乘子,V 0 為焊點(diǎn)的初始體積。式(5)中被積函數(shù)滿足歐拉-拉格朗日方程時(shí),可得泛函極值,利用變分問題的數(shù)值解法可求解釬料的平衡形態(tài) [9] 。
根據(jù)上述模型,采用 Surface Evolver 求解出焊點(diǎn)穩(wěn)態(tài)形貌。本文采用 SAC305 無鉛焊點(diǎn)材料,其密度為7.3 g/cm 3 。BGA 的焊點(diǎn)間距為 1 mm 時(shí),植球直徑為0.6mm,芯片側(cè)與PCB側(cè)的焊盤直徑分別選擇 0.4mm、0.45 mm、0.5 mm 和 0.55 mm。
考慮到不同尺寸的焊盤在同一工藝下的錫量存在差異,最終形貌的焊點(diǎn)尺寸會(huì)不同。根據(jù) IPC-7525A漏模板設(shè)計(jì)標(biāo)準(zhǔn)選擇 BGA 鋼網(wǎng)開孔比例以及錫膏厚度,避免選擇較大數(shù)值(容易導(dǎo)致實(shí)際表面貼裝過程中的焊接異常)。選擇厚度為 0.13 mm 的鋼網(wǎng),開孔面積為 90%的 BGA 焊盤,樹脂的質(zhì)量分?jǐn)?shù)為 50%的錫膏,計(jì)算出不同焊盤設(shè)計(jì)條件下的焊點(diǎn)體積。當(dāng)焊點(diǎn)體積和焊盤尺寸固定時(shí),不同高度下的焊點(diǎn)系統(tǒng)能量與焊點(diǎn)高度的關(guān)系如圖 1 所示,其整體呈拋物線變化,選取不同參數(shù)組合下焊點(diǎn)系統(tǒng)能量曲線最低點(diǎn)時(shí)的平衡焊點(diǎn)高度 H,焊點(diǎn)形態(tài)的預(yù)測尺寸如表 1 所示。根據(jù)其尺寸參數(shù)擬合出的焊點(diǎn)穩(wěn)態(tài)形貌如圖 2 所示。
2.2 仿真模型
參考陣列為 40×40、pin 間距為 1 mm 的 SiP 芯片封裝結(jié)構(gòu),芯片基板尺寸為 41 mm×41 mm×1 mm,建立有限元分析模型,將模型簡化為 1/4 模型進(jìn)行仿真計(jì)算,SiP 封裝模型與有限元網(wǎng)格劃分如圖 3 所示。焊點(diǎn)采用無鉛焊料,對局部焊點(diǎn)加密網(wǎng)格,采用 Anand
黏塑性網(wǎng)格單元,SiP 封裝模型的材料參數(shù)如表 2 所示,其中 x、y、z 表示坐標(biāo)軸,xy、yz、xz 表示 2 個(gè)坐標(biāo)軸形成的面 [10-11] 。BGA 焊點(diǎn)的黏塑性參數(shù)如表 3 所示 [12] 。
3 殘余應(yīng)力與翹曲仿真
在 ANSYS workbench 仿真模塊中建立回流焊仿真分析模型。考慮到在回流冷卻過程中,焊點(diǎn)從液態(tài)逐漸固化,其應(yīng)力會(huì)隨溫度變化。為了參考不同參數(shù)組合條件下殘余應(yīng)力和翹曲的變化,以 150 ℃作為零應(yīng)力參考溫度,設(shè)置環(huán)境溫度為 25 ℃。芯片側(cè)焊盤直徑為 0.4 mm,PCB 側(cè)焊盤直徑為 0.4 mm,在冷卻速率為 1 ℃·s -1 的條件下,SiP 基板的形變分布與 z 軸對角線的翹曲值如圖 4(a)(b)所示。由于 PCB 在 z 軸方向的 CTE 大于 BT 基板,在回流冷卻過程中,PCB 的收縮比例較大,產(chǎn)生的應(yīng)力差使芯片基板向 PCB 側(cè)彎曲變形,最終呈現(xiàn)出哭臉型(芯片邊緣低于中心)翹曲,其翹曲值為 68.668 μm。此時(shí)四角位置的形變量最大。
芯片側(cè)焊點(diǎn)的殘余應(yīng)力為 106.42 MPa,如圖 4(c)所示。PCB 側(cè)焊點(diǎn)的殘余應(yīng)力為 78.21 MPa,如圖 4(d) 所示。芯片側(cè)焊點(diǎn)的殘余應(yīng)力大于 PCB 側(cè)焊點(diǎn)。
4 正交試驗(yàn)分析
4.1 確立變量因素與優(yōu)化目標(biāo)
將 BGA 焊點(diǎn)在回流過程中的殘余應(yīng)力以及翹曲值作為優(yōu)化目標(biāo),選取BGA焊點(diǎn)芯片側(cè)的焊盤直徑D 1 、PCB 側(cè)的焊盤直徑 D 2 以及冷卻速率 S 作為設(shè)計(jì)變量。
4.2 正交試驗(yàn)設(shè)計(jì)
為了得出回流冷卻過程中 BGA 焊點(diǎn)殘余應(yīng)力與翹曲值的最優(yōu)組合,需要進(jìn)行大量的組合試驗(yàn)。為了減少試驗(yàn)的工作量,同時(shí)得到各影響因子的影響程度,采用正交試驗(yàn)法來優(yōu)化分析方案。每個(gè)因素選取 4個(gè)水平,利用芯片側(cè)焊盤直徑和 PCB 側(cè)焊盤直徑的組合在表 1 里找到其焊點(diǎn)的體積和高度,據(jù)此設(shè)計(jì)出回流冷卻因素水平(見表 4)。
采用 L 16 (4 3 )正交表,再結(jié)合表 1 的焊點(diǎn)形態(tài)預(yù)測尺寸建立仿真模型,計(jì)算出回流冷卻過程中焊點(diǎn)的殘余應(yīng)力以及基板翹曲值。得到的 16 組回流冷卻正交試驗(yàn)結(jié)果如表 5 所示。
5 殘余應(yīng)力與翹曲的灰色關(guān)聯(lián)分析
由于 L 16 (4 3 )正交表的試驗(yàn)設(shè)計(jì)只確定了 16 組已知的白色系統(tǒng)組合,仍然有 48 組黑色系統(tǒng)組合未知,這就構(gòu)成了已知和未知的灰色系統(tǒng)。對于雙優(yōu)化目標(biāo)的水平組合,常規(guī)的試驗(yàn)設(shè)計(jì)優(yōu)化分析無法滿足,因此引入灰色關(guān)聯(lián)分析法。2 個(gè)目標(biāo)隨不同因素水平變化的關(guān)聯(lián)性量度稱為關(guān)聯(lián)度。當(dāng) 2 個(gè)因素的變化區(qū)域一致時(shí)關(guān)聯(lián)度高,反之則低,因此灰色關(guān)聯(lián)分析方法會(huì)根據(jù)不同因素水平之間的灰色關(guān)聯(lián)度來衡量其數(shù)值關(guān)系 [13] 。
5.1 殘余應(yīng)力與翹曲的灰色關(guān)聯(lián)系數(shù)
由于系統(tǒng)中數(shù)值的物理意義不同,為防止小數(shù)值序列被大數(shù)值掩蓋,統(tǒng)一對序列進(jìn)行規(guī)范化處理。常見的處理方法有均值化法、初值化法和極差變換法,此處采用極差變換法對殘余應(yīng)力和翹曲值進(jìn)行規(guī)范化處理。參考序列和規(guī)范化序列分辨系數(shù)取一般值 0.5進(jìn)行灰色關(guān)聯(lián)系數(shù)計(jì)算。灰色關(guān)聯(lián)系數(shù)越大,表明殘余應(yīng)力與翹曲值貼合程度越大 [9] 。
5.2 殘余應(yīng)力與翹曲最優(yōu)解的確定
在回流冷卻過程中,優(yōu)化 BGA 焊點(diǎn)的殘余應(yīng)力與 BT 基板的翹曲值有助于提高芯片的可靠性,其中焊點(diǎn)的殘余應(yīng)力值與基板的翹曲值越小越好,但 2 個(gè)目標(biāo)優(yōu)化的權(quán)重比是個(gè)主觀因子,長期可靠性條件下的殘余應(yīng)力權(quán)重大于翹曲值,工藝管控中的翹曲值權(quán)重大于殘余應(yīng)力,因此 2 種不同類型的關(guān)聯(lián)度如表 6所示。
確定 BGA 最優(yōu)參數(shù)組合前需計(jì)算出不同參數(shù)水平的平均關(guān)聯(lián)度,灰色關(guān)聯(lián)度的定義表明,平均關(guān)聯(lián)度越大越接近最優(yōu)解,通過計(jì)算得出目標(biāo)函數(shù)的平均關(guān)聯(lián)度 [9] 。其中殘余應(yīng)力權(quán)重大于翹曲值的目標(biāo)函數(shù)的平均關(guān)聯(lián)度如表 7 所示,其最優(yōu)參數(shù)組合為D 14 D 21 S 1 ,即芯片側(cè)焊盤直徑 D 1 選第 4 組數(shù)據(jù) 0.55 mm,PCB 側(cè)焊盤直徑 D 2 選第 1 組數(shù)據(jù) 0.4 mm,冷卻速率 S選第 1 組數(shù)據(jù) 1 ℃·s -1 。翹曲值權(quán)重大于殘余應(yīng)力的平均關(guān)聯(lián)度如表 8 所示,可以得出最優(yōu)參數(shù)組合為D 11 D 21 S 1 ,即芯片側(cè)焊盤直徑 D 1 為 0.4 mm,PCB 側(cè)焊盤直徑 D 2 為 0.4 mm,冷卻速率 S 為1 ℃·s -1 。
5.3 焊點(diǎn)殘余應(yīng)力與翹曲的最優(yōu)參數(shù)組合仿真驗(yàn)證
已經(jīng)分析得出翹曲值權(quán)重大于殘余應(yīng)力的最優(yōu)參數(shù)組合為 D 11 D 21 S 1 (仿真結(jié)果見圖 4),殘余應(yīng)力權(quán)重大于翹曲值的最優(yōu)參數(shù)組合為 D 14 D 21 S 1 ,為了驗(yàn)證灰色關(guān)聯(lián)分析的準(zhǔn)確性,采用 D 14 D 21 S 1 的參數(shù)組合進(jìn)行仿真驗(yàn)證。參數(shù)組合 D 14 D 21 S 1 的仿真結(jié)果如圖 5 所示,其芯片側(cè)殘余應(yīng)力為 87.757 MPa,PCB 側(cè)殘余應(yīng)力為65.622 MPa,基板翹曲值為 70.226 μm。
5.4 焊點(diǎn)殘余應(yīng)力與翹曲優(yōu)化綜合仿真驗(yàn)證
殘余應(yīng)力權(quán)重大于翹曲值時(shí)的參數(shù)組合 D 14 D 21 S 1有一定的降低殘余應(yīng)力的效果,但同時(shí)翹曲值會(huì)增加。同理參數(shù)組合 D 11 D 21 S 1 的翹曲值權(quán)重大于殘余應(yīng)力,會(huì)導(dǎo)致其殘余應(yīng)力增加,翹曲值降低。綜合 2 種組合結(jié)果,修改芯片側(cè)和 PCB 側(cè)的焊盤尺寸有助于優(yōu)化殘余應(yīng)力和翹曲值。
若同時(shí)優(yōu)化 2 種參數(shù),可將其組合,以 D 11 D 21 S 1 組合為主降低翹曲值,四角位置殘余應(yīng)力較大的焊點(diǎn)均采用非功能焊點(diǎn),采用 D 14 D 21 S 1 組合的焊點(diǎn)尺寸參數(shù)。綜合 2 種參數(shù)優(yōu)化后的回流降溫仿真結(jié)果如圖 6 所示,其翹曲值為 68.867 μm,芯片側(cè)殘余應(yīng)力為87.303 MPa,比初始值下降了 17.9%,PCB 側(cè)殘余應(yīng)力為 64.853 MPa,比初始值下降了 17.1%。相比 D 11 D 21 S 1組合,其翹曲值比初始值 68.668 μm 略大,但殘余應(yīng)力明顯降低,該組合綜合考慮了翹曲值與殘余應(yīng)力,實(shí)現(xiàn)了設(shè)計(jì)優(yōu)化。
6 結(jié)論
本文通過仿真軟件 Surface Evolver 對不同焊盤設(shè)計(jì)的 BGA 焊點(diǎn)的回流形態(tài)進(jìn)行預(yù)測,研究了焊盤設(shè)計(jì)與冷卻速率對焊點(diǎn)的殘余應(yīng)力和基板翹曲值的影響,總結(jié)出以下結(jié)論:
(1)可通過灰度分析法分析回流降溫速率,回流降溫速率的增加對基板翹曲和焊點(diǎn)殘余應(yīng)力有一定的優(yōu)化作用,可以指導(dǎo)工藝進(jìn)行參數(shù)調(diào)整;
(2)調(diào)整芯片和 PCB 的焊盤設(shè)計(jì)可以優(yōu)化基板翹曲和焊點(diǎn)殘余應(yīng)力,可以通過設(shè)計(jì)降低工藝中的翹曲不良,減少殘余應(yīng)力引起的焊點(diǎn)早期失效;
(3)不同產(chǎn)品對于翹曲和殘余應(yīng)力的要求不同,可以有針對性地進(jìn)行芯片側(cè)和 PCB 側(cè)的焊盤設(shè)計(jì)來降低翹曲和殘余應(yīng)力或者對兩者進(jìn)行綜合優(yōu)化。
審核編輯 黃宇
-
芯片
+關(guān)注
關(guān)注
459文章
52090瀏覽量
435323 -
SiP
+關(guān)注
關(guān)注
5文章
522瀏覽量
106082 -
封裝
+關(guān)注
關(guān)注
128文章
8446瀏覽量
144681 -
焊點(diǎn)
+關(guān)注
關(guān)注
0文章
136瀏覽量
13007
發(fā)布評論請先 登錄
一種低翹曲扇出重構(gòu)方案
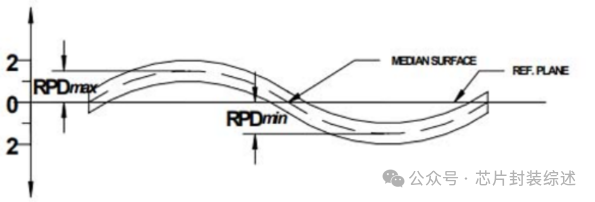
芯片封裝中的焊點(diǎn)圖案設(shè)計(jì)
SIP封裝技術(shù):引領(lǐng)電子封裝新革命!
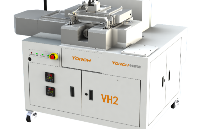
BGA封裝器件焊點(diǎn)抗剪強(qiáng)度測試全解析,應(yīng)用推拉力機(jī)
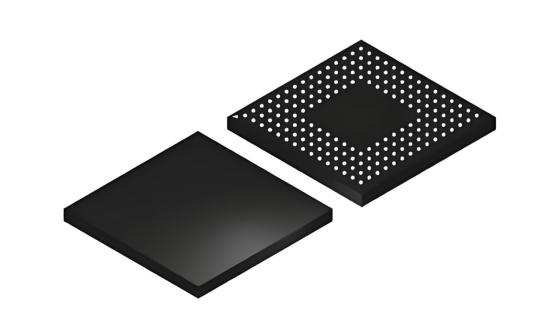
線路板PCB工藝中的翹曲問題產(chǎn)生的原因
QFN封裝中焊點(diǎn)形成的過程
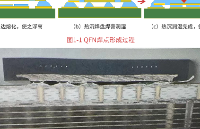
焊接應(yīng)力是什么?6種方法輕松去除
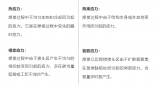
深入剖析:封裝工藝對硅片翹曲的復(fù)雜影響
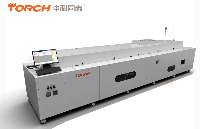
系統(tǒng)級封裝(SiP)技術(shù)介紹
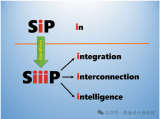
2.5D封裝的熱力挑戰(zhàn)
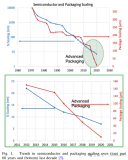
PCB板彎板翹的原因及改善措施
機(jī)械應(yīng)力和熱應(yīng)力下的BGA焊點(diǎn)可靠性
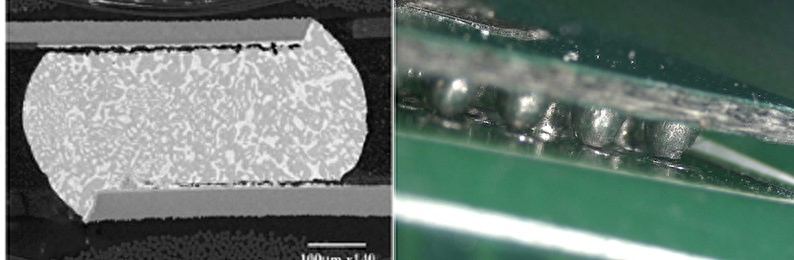
電子制造中的翹曲難題:PCB板整平方法綜述
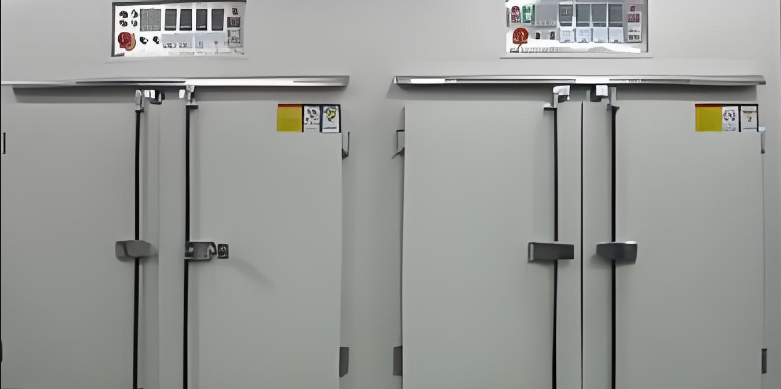
評論