第一節(jié): SMT常用名詞中英文對照表
第二節(jié): SMT簡介
SMT 是Surface mount technology的簡寫,意為表面貼裝技術(shù)。亦即是無需對PCB鉆插裝孔而直接將元器件貼焊到PCB表面規(guī)定位置上的裝聯(lián)技術(shù)。
一、SMT的特點
從上面的定義上,我們知道SMT是從傳統(tǒng)的穿孔插裝技術(shù)(THT)發(fā)展起來的,但又區(qū)別于傳統(tǒng)的THT。那么,SMT與THT比較它有什么優(yōu)點呢?下面就是其最為突出的優(yōu)點:
組裝密度高、電子產(chǎn)品體積小、重量輕,貼片元件的體積和重量只有傳統(tǒng)插裝元件的1/10左右,一般采用SMT之后,電子產(chǎn)品體積縮小40%~60%,重量減輕60%~80%。
可靠性高、抗振能力強。焊點缺陷率低。
高頻特性好。減少了電磁和射頻干擾。
易于實現(xiàn)自動化,提高生產(chǎn)效率。
降低成本達(dá)30%~50%。節(jié)省材料、能源、設(shè)備、人力、時間等。
一、采用表面貼裝技術(shù)(SMT)是電子產(chǎn)品業(yè)的趨勢
我們知道了SMT的優(yōu)點,就要利用這些優(yōu)點來為我們服務(wù),而且隨著電子產(chǎn)品的微型化使得THT無法適應(yīng)產(chǎn)品的工藝要求。因此,SMT是電子裝聯(lián)技術(shù)的發(fā)展趨勢。其表現(xiàn)在:
1. 電子產(chǎn)品追求小型化,使得以前使用的穿孔插件元件已無法適應(yīng)其要求。
2. 電子產(chǎn)品功能更完整,所采用的集成電路(IC)因功能強大使引腳眾多,已無法做成傳統(tǒng)的穿孔元件,特別是大規(guī)模、高集成IC,不得不采用表面貼片元件的封裝。
3. 產(chǎn)品批量化,生產(chǎn)自動化,廠方要以低成本高產(chǎn)量,出產(chǎn)優(yōu)質(zhì)產(chǎn)品以迎合顧客需求及加強市場競爭力。
4. 電子元件的發(fā)展,集成電路(IC)的開發(fā),半導(dǎo)體材料的多元應(yīng)用。
5. 電子產(chǎn)品的高性能及更高裝聯(lián)精度要求。
二、常用術(shù)語解釋
1. 組裝圖:是一種工藝文件,圖上有一些元件的目錄,告訴我們每一程序中所需的元件及元件所插的位置。
2. 軸向引線元件:是一種只有兩個管腳的元,管腳在元件的兩端反向伸出。
3. 徑向引線元件:元件的管腳在元件主體的同一端伸出。
4. 印刷電路板(PCB):沒有插元件的電路板。
5. 成品電路板(PCP):已經(jīng)插好元件的印刷電路板。
6. 單面板:電路板上只有一面用金屬處理。
7. 雙面板:上、下兩面都有線路的電路板。
8. 層板:除上、下兩面都有線路外,在電路板內(nèi)層也有線路的電路板。
9. 焊盤:PCB表面處理加寬局部引線,無絕緣漆覆蓋的部分面積,用來連接元件、明線等等。可以包括元件管腳洞。
10. 元件符號:每種元件,比如說電阻和電容,都有一個元件符號,這些符號通常被標(biāo)在電路板的元件面上。不同種類的元件用不同的字母識別,在同種類的元件中,用不同的數(shù)字從所有其它項目中識別出來。【例:電容的元件符號為C,一塊電路板上有4個電容,可分別表示為C4、C5、C10、C15。】
11. 極性元件:有些元件,插入電路板時必需定向,否則元件就有可能在測試時被融化或發(fā)生爆炸。
12. 極性標(biāo)志:在印刷電路板上,極性元件的位置印有極性符號,以方便正確插入元件。
第一節(jié):SMT工藝介紹
一、工藝流程名稱
1. 表面貼裝組件(SMA)(surfacemount assemblys)采用表面貼裝技術(shù)完成裝聯(lián)的印制板組裝件。
2. 回流焊(reflowsoldering)通過熔化預(yù)先分配到PCB焊盤上的焊膏,實現(xiàn)表面貼裝元器件與PCB焊盤的連接。
3.波峰焊(wave soldering)將溶化的焊料,經(jīng)專用設(shè)備噴流成設(shè)計要求的焊料波峰,使預(yù)先裝有電子元器件的PCB通過焊料波峰,實現(xiàn)元器與PCB焊盤這間的連接。
4. 細(xì)間距 (finepitch)小于0.5mm引腳間距
5. 引腳共面性 (leadcoplanarity )指表面貼裝元器件引腳垂直高度偏差,即引腳的最高腳底與最低引腳底形成的平面這間的垂直距離。其值一般不大于0.1mm。
6. 焊膏 ( solderpaste )由粉末狀焊料合金、焊劑和一些起粘性作用及其他作用的添加劑混合成具有一定粘度和良好觸變性的焊料膏。
7.固化 (curing )在一定的溫度、時間條件下,加熱貼裝了元器件的貼片膠,以使元器件與PCB板暫時固定在一起的工藝過程。
8.貼片膠 或稱紅膠(adhesives)(SMA)固化前具有一定的初粘度有外形,固化后具有足夠的粘接強度的膠體。
9.點膠 ( dispensing )表面貼裝時,往PCB上施加貼片膠的工藝過程。
10. 點膠機 (dispenser )能完成點膠操作的設(shè)備。
11. 貼裝( pickand place )將表面貼裝元器件從供料器中拾取并貼放到PCB規(guī)定位置上的操作。
12. 貼片機 (placement equipment )完成表面貼片裝元器件貼片裝功能的專用工藝設(shè)備。
13. 高速貼片機 (high placement equipment )貼裝速度大于2萬點/小時的貼片機。
14.多功能貼片機( multi-function placement equipment )
15. 用于貼裝體形較大、引線間距較小的表面貼裝器件,貼裝精度要求較高的貼片機。
16.熱風(fēng)回流焊 ( hot air reflow soldering )
17. 以強制循環(huán)流動的熱氣流進(jìn)行加熱的回流焊。
18.貼片檢驗 (placement inspection )
19. 貼片時或完成后,對于有否漏貼、錯位、貼錯、元器件損壞等情況進(jìn)行的質(zhì)量檢驗。
20.鋼網(wǎng)印刷 (metal stencil printing )
21. 使用不銹鋼漏板將焊錫膏印到PCB焊盤上的印刷工藝過程。
22.印刷機 (printer)
23. 在SMT中,用于鋼網(wǎng)印刷的專用設(shè)備。
24.爐后檢驗 (inspection after soldering )
25. 對貼片完成后經(jīng)回流爐焊接或固化的PCBA的質(zhì)量檢驗。
26.爐前檢驗(inspection before soldering )
27. 貼片完成后在回流爐焊接或固化前作貼片質(zhì)量檢驗。
28.返修 (reworking )
29. 為去除PCBA的局部缺陷而進(jìn)行的修復(fù)過程。
30.返修工作臺 ( rework station )
31. 能對有質(zhì)量缺陷的PCBA進(jìn)行返修的專用設(shè)備。
一、表面貼裝方法分類
根據(jù)SMT的工藝制程不同,把SMT分為點膠制程(波峰焊)和錫膏制程(回流焊)。它們的主要區(qū)別為:
貼片前的工藝不同,前者使用貼片膠,后者使用焊錫膏。
貼片后的工藝不同,前者過回流爐只起固定作用、還須過波峰焊,后者過回流爐起焊接作用。
二、根據(jù)SMT的工藝過程則可把其分為以下幾種類型。
第一類:只采用表面貼裝元件的裝配
只有表面貼裝的單面裝配
工序: 絲印錫膏=>貼裝元件=>回流焊接
只有表面貼裝的雙面裝配
工序: 絲印錫膏=>貼裝元件=>回流焊接=>反面=>絲印錫膏=>貼裝元件=>回流焊接
第二類 一面采用表面貼裝元件和另一面采用表面貼元件與穿孔元件混合的裝配
工序: 絲印錫膏(頂面)=>貼裝元件=>回流焊接=>插件機插元件=>反面=>點膠(底面)=>貼裝元件=>烘干膠=>(反面手插大型元件=>)波峰焊接
第三類 頂面采用穿孔元件, 底面采用表面貼裝元件的裝配
工序: 插件機插元件=>反面=>點膠=>貼裝元件=>烘干膠=>反面=>手插插元件=>波峰焊接
四、 SMT的工藝流程
領(lǐng)PCB、貼片元件à貼片程式錄入、道軌調(diào)節(jié)、爐溫調(diào)節(jié) à上料à上PCBà印刷à貼片à檢查à回流à插件機插元件à點膠à貼片à檢查à固化à檢查à包裝à保管
五、各工序的工藝要求與特點:
1. 生產(chǎn)前準(zhǔn)備
清楚產(chǎn)品的型號、PCB的版本號、生產(chǎn)數(shù)量與批號。
清楚元器件的數(shù)量、規(guī)格、代用料。
清楚貼片、點膠、印刷程式的名稱。
有清晰的上料卡(Z表)。
有生產(chǎn)作業(yè)指導(dǎo)書、及清楚指導(dǎo)書內(nèi)容。
2.轉(zhuǎn)機時要求
確認(rèn)機器程式正確。
確認(rèn)每一個Feeder位的元器件與上料卡相對應(yīng)。
確認(rèn)所有軌道寬度和定位針在正確位置。
確認(rèn)所有Feeder正確、牢固地安裝與料臺上。
確認(rèn)所有Feeder的送料間距是否正確。
確認(rèn)機器上板與下板是非順暢。
檢查點膠量及大小、高度、位置是否適合。
檢查印刷錫膏量、高度、位置是否適合。
檢查貼片元件及位置是否正確。
檢查固化或回流后是否產(chǎn)生不良。
3.點膠
點膠工藝主要用于引線元件通孔插裝(THT)與表面貼裝(SMT)共存的貼插混裝工藝。在整個生產(chǎn)工藝流程(見圖)中,我們可以看到,印刷電路板(PCB)其中一面元件從開始進(jìn)行點膠固化后,到了最后才能進(jìn)行波峰焊焊接,這期間間隔時間較長,而且進(jìn)行其他工藝較多,元件的固化就顯得尤為重要。
點膠過程中的工藝控制。生產(chǎn)中易出現(xiàn)以下工藝缺陷:膠點大小不合格、拉絲、膠水浸染焊盤、固化強度不好易掉片等。因此進(jìn)行點膠各項技術(shù)工藝參數(shù)的控制是解決問題的辦法。
4.印刷
在表面貼裝裝配的回流焊接中,錫膏用于表面貼裝元件的引腳或端子與焊盤之間的連接,有許多變量。如錫膏、絲印機、錫膏應(yīng)用方法和印刷工藝過程。在印刷錫膏的過程中,基板放在工作臺上,機械地或真空夾緊定位,用定位銷或視覺來對準(zhǔn),用模板(stencil)進(jìn)行錫膏印刷。
在模板錫膏印刷過程中,印刷機是達(dá)到所希望的印刷品質(zhì)的關(guān)鍵。
在印刷過程中,錫膏是自動分配的,印刷刮板向下壓在模板上,使模板底面接觸到電路板頂面。當(dāng)刮板走過所腐蝕的整個圖形區(qū)域長度時,錫膏通過模板/絲網(wǎng)上的開孔印刷到焊盤上。在錫膏已經(jīng)沉積之后,絲網(wǎng)在刮板之后馬上脫開,回到原地。這個間隔或脫開距離是設(shè)備設(shè)計所定的,大約0.020"~0.040"。
脫開距離與刮板壓力是兩個達(dá)到良好印刷品質(zhì)的與設(shè)備有關(guān)的重要變量。
如果沒有脫開,這個過程叫接觸(on-contact)印刷。當(dāng)使用全金屬模板和刮刀時,使用接觸印刷。非接觸(off-contact)印刷用于柔性的金屬絲網(wǎng)。
在錫膏絲印中有三個關(guān)鍵的要素,我們叫做三個S: Solder paste(錫膏),Stencils (模板),和Squeegees(絲印刮板)。三個要素的正確結(jié)合是持續(xù)的絲印品質(zhì)的關(guān)鍵所在。
刮板(squeegee)
刮板作用,在印刷時,使刮板將錫膏在前面滾動,使其流入模板孔內(nèi), 然后刮去多余錫膏,在PCB焊盤上留下與模板一樣厚的錫膏。
常見有兩種刮板類型:橡膠或聚氨酯(polyurethane)刮板和金屬刮板。
金屬刮板由不銹鋼或黃銅制成,具有平的刀片形狀,使用的印刷角度為30~55°。使用較高的壓力時,它不會從開孔中挖出錫膏,還因為是金屬的,它們不象橡膠刮板那樣容易磨損,因此不需要鋒利。它們比橡膠刮板成本貴得多,并可能引起模板磨損。
橡膠刮板,使用70-90橡膠硬度計(durometer)硬度的刮板。
當(dāng)使用過高的壓力時,滲入到模板底部的錫膏可能造成錫橋,要求頻繁的底部抹擦。甚至可能損壞刮板和模板或絲網(wǎng)。過高的壓力也傾向于從寬的開孔中挖出錫膏,引起焊錫圓角不夠。刮板壓力低造成遺漏和粗糙的邊緣,
刮板的磨損、壓力和硬度決定印刷質(zhì)量,應(yīng)該仔細(xì)監(jiān)測。對可接受的印刷品質(zhì),刮板邊緣應(yīng)該鋒利、平直和直線。
模板(stencil)類型
目前使用的模板主要有不銹鋼模板,其的制作主要有三種工藝:化學(xué)腐蝕、激光切割和電鑄成型。
5. 貼裝
貼裝前應(yīng)進(jìn)行下列項目的檢查:
元器件的可焊性、引線共面性、包裝形式
PCB尺寸、外觀、翹曲、可焊性、阻焊膜(綠油)
料站的元件規(guī)格核對
是否有手補件或臨時不貼件、加貼件
Feeder與元件包裝規(guī)格是否一致。
貼裝時應(yīng)檢查項目:
檢查所貼裝元件是否有偏移等缺陷,對偏移元件進(jìn)行調(diào)校。
檢查貼裝率,并對元件與貼片頭進(jìn)行臨控。
6. 固化、回流
在固化、回流工藝?yán)镒钪饕强刂坪霉袒⒒亓鞯臏囟惹€亦即是固化、回流條件,正確的溫度曲線將保證高品質(zhì)的焊接錫點。在回流爐里,其內(nèi)部對于我們來說是一個黑箱,我們不清楚其內(nèi)部發(fā)生的事情,這樣為我制定工藝帶來重重困難。為克服這個困難,在SMT行業(yè)里普遍采用溫度測試儀得出溫度曲線,再參巧之進(jìn)行更改工藝。
溫度曲線是施加于電路裝配上的溫度對時間的函數(shù),當(dāng)在笛卡爾平面作圖時,回流過程中在任何給定的時間上,代表PCB上一個特定點上的溫度形成一條曲線。
幾個參數(shù)影響曲線的形狀,其中最關(guān)鍵的是傳送帶速度和每個區(qū)的溫度設(shè)定。帶速決定機板暴露在每個區(qū)所設(shè)定的溫度下的持續(xù)時間,增加持續(xù)時間可以允許更多時間使電路裝配接近該區(qū)的溫度設(shè)定。每個區(qū)所花的持續(xù)時間總和決定總共的處理時間。
每個區(qū)的溫度設(shè)定影響PCB的溫度上升速度,高溫在PCB與區(qū)的溫度之間產(chǎn)生一個較大的溫差。增加區(qū)的設(shè)定溫度允許機板更快地達(dá)到給定溫度。因此,必須作出一個圖形來決定PCB的溫度曲線。接下來是這個步驟的輪廓,用以產(chǎn)生和優(yōu)化圖形。
需要下列設(shè)備和輔助工具:溫度曲線儀、熱電偶、將熱電偶附著于PCB的工具和錫膏參數(shù)表。測溫儀一般分為兩類:實時測溫儀,即時傳送溫度/時間數(shù)據(jù)和作出圖形;而另一種測溫儀采樣儲存數(shù)據(jù),然后上載到計算機。
將熱電偶使用高溫焊錫如銀/錫合金,焊點盡量最小附著于PCB,或用少量的熱化合物(也叫熱導(dǎo)膏或熱油脂)斑點覆蓋住熱電偶,再用高溫膠帶(如Kapton)粘住附著于PCB。
附著的位置也要選擇,通常最好是將熱電偶尖附著在PCB焊盤和相應(yīng)的元件引腳或金屬端之間。如圖示
(將熱電偶尖附著在PCB焊盤和相應(yīng)的元件引腳或金屬端之間)
錫膏特性參數(shù)表也是必要的,其應(yīng)包含所希望的溫度曲線持續(xù)時間、錫膏活性溫度、合金熔點和所希望的回流最高溫度。
理想的溫度曲線
理論上理想的曲線由四個部分或區(qū)間組成,前面三個區(qū)加熱、最后一個區(qū)冷卻。爐的溫區(qū)越多,越能使溫度曲線的輪廓達(dá)到更準(zhǔn)確和接近設(shè)定。
(理論上理想的回流曲線由四個區(qū)組成,前面三個區(qū)加熱、最后一個區(qū)冷卻)
預(yù)熱區(qū),用來將PCB的溫度從周圍環(huán)境溫度提升到所須的活性溫度。其溫度以不超過每秒2~5°C速度連續(xù)上升,溫度升得太快會引起某些缺陷,如陶瓷電容的細(xì)微裂紋,而溫度上升太慢,錫膏會感溫過度,沒有足夠的時間使PCB達(dá)到活性溫度。爐的預(yù)熱區(qū)一般占整個加熱通道長度的25~33%。
活性區(qū),有時叫做干燥或浸濕區(qū),這個區(qū)一般占加熱通道的33~50%,有兩個功用,第一是,將PCB在相當(dāng)穩(wěn)定的溫度下感溫,使不同質(zhì)量的元件具有相同溫度,減少它們的相當(dāng)溫差。第二個功能是,允許助焊劑活性化,揮發(fā)性的物質(zhì)從錫膏中揮發(fā)。一般普遍的活性溫度范圍是120~150°C,如果活性區(qū)的溫度設(shè)定太高,助焊劑沒有足夠的時間活性化。因此理想的曲線要求相當(dāng)平穩(wěn)的溫度,這樣使得PCB的溫度在活性區(qū)開始和結(jié)束時是相等的。
回流區(qū),其作用是將PCB裝配的溫度從活性溫度提高到所推薦的峰值溫度。典型的峰值溫度范圍是205~230°C,這個區(qū)的溫度設(shè)定太高會引起PCB的過分卷曲、脫層或燒損,并損害元件的完整性。
理想的冷卻區(qū)曲線應(yīng)該是和回流區(qū)曲線成鏡像關(guān)系。越是靠近這種鏡像關(guān)系,焊點達(dá)到固態(tài)的結(jié)構(gòu)越緊密,得到焊接點的質(zhì)量越高,結(jié)合完整性越好。
實際溫度曲線
當(dāng)我們按一般PCB回流溫度設(shè)定后,給回流爐通電加熱,當(dāng)設(shè)備臨測系統(tǒng)顯示爐內(nèi)溫度達(dá)到穩(wěn)定時,利用溫度測試儀進(jìn)行測試以觀察其溫度曲線是否與我們的預(yù)定曲線相符。否則進(jìn)行各溫區(qū)的溫度重新設(shè)置及爐子參數(shù)調(diào)整,這些參數(shù)包括傳送速度、冷卻風(fēng)扇速度、強制空氣沖擊和惰性氣體流量,以達(dá)到正確的溫度為止。
典型PCB回流區(qū)間溫度設(shè)定
區(qū)間 | 區(qū)間溫度設(shè)定 | 區(qū)間末實際板溫 |
預(yù)熱 | 210°C | 140°C |
活性 | 180°C | 150°C |
回流 | 240°C | 210°C |
以下是一些不良的回流曲線類型:
圖一、預(yù)熱不足或過多的回流曲線
圖二、活性區(qū)溫度太高或太低
圖三、回流太多或不夠
圖四、冷卻過快或不夠
當(dāng)最后的曲線圖盡可能的與所希望的圖形相吻合,應(yīng)該把爐的參數(shù)記錄或儲存以備后用。雖然這個過程開始很慢和費力,但最終可以取得熟練和速度,結(jié)果得到高品質(zhì)的PCB的高效率的生產(chǎn)
7. 回流焊主要缺陷分析:
錫珠(SolderBalls):
原因:
1、絲印孔與焊盤不對位,印刷不精確,使錫膏弄臟PCB。
2、錫膏在氧化環(huán)境中暴露過多、吸空氣中水份太多。
3、加熱不精確,太慢并不均勻。
4、加熱速率太快并預(yù)熱區(qū)間太長。
5、錫膏干得太快。
6、助焊劑活性不夠。
7、太多顆粒小的錫粉。
8、回流過程中助焊劑揮發(fā)性不適當(dāng)。
錫球的工藝認(rèn)可標(biāo)準(zhǔn)是:當(dāng)焊盤或印制導(dǎo)線的之間距離為0.13mm時,錫珠直徑不能超過0.13mm,或者在600mm平方范圍內(nèi)不能出現(xiàn)超過五個錫珠。
錫橋(Bridging):一般來說,造成錫橋的因素就是由于錫膏太稀,包括錫膏內(nèi)金屬或固體含量低、搖溶性低、錫膏容易榨開,錫膏顆粒太大、助焊劑表面張力太小。焊盤上太多錫膏,回流溫度峰值太高等。
開路(Open):
原因:
1、錫膏量不夠。
2、元件引腳的共面性不夠。
3、錫濕不夠(不夠熔化、流動性不好),錫膏太稀引起錫流失。
4、引腳吸錫(象燈芯草一樣)或附近有連線孔。引腳的共面性對密間距和超密間距引腳元件特別重要,一個解決方法是在焊盤上預(yù)先上錫。引腳吸錫可以通過放慢加熱速度和底面加熱多、上面加熱少來防止。也可以用一種浸濕速度較慢、活性溫度高的助焊劑或者用一種Sn/Pb不同比例的阻滯熔化的錫膏來減少引腳吸錫。
8. 檢查、包裝
檢查是為我們客戶(亦是下一工序)提供100%良好品的保障,因此我們必須對每一個PCBA進(jìn)行檢查。
檢查著重項目:
PCBA的版本號是否為更改后的版本。
客戶有否要求元器件使用代用料或指定廠商、牌子的元器件。
IC、二極管、三極管、鉭電容、鋁電容、開關(guān)等有方向的元器件的方向是否正確。
焊接后的缺陷:短路、開路、掉件、假焊
包裝是為把PCBA安全地運送到客戶(下一工序)的手上。要保證運輸途中的PCBA的安全,我們就要有可靠的包裝以進(jìn)行運輸。公司目前所用的包裝工具有:
用膠袋包裝后豎堆放于膠盆
把PCBA使用專用的架(公司定做、設(shè)備專商提供)存放
客戶指定的包裝
不管使用何種包裝均要求對包裝箱作明確的標(biāo)識,該標(biāo)識必須包含下元列內(nèi)容:
產(chǎn)品名稱及型號
產(chǎn)品數(shù)量
生產(chǎn)日期
檢驗人
在SMT貼裝過程中,難免會遇上某些元器件使用人工貼裝的方法,人工貼裝時我們要注意下列事項:
避免將不同的元件混在一起
切勿讓元件受到過度的拉力和壓力
轉(zhuǎn)動元件是應(yīng)夾著主體,不應(yīng)夾著引腳或焊接端
放置元件是應(yīng)使用清潔的鑷子
不使用丟掉或標(biāo)識不明的元器件
使用清潔的元器件
審核編輯 :李倩
-
pcb
+關(guān)注
關(guān)注
4349文章
23393瀏覽量
406299 -
印刷電路板
+關(guān)注
關(guān)注
4文章
822瀏覽量
35853 -
smt
+關(guān)注
關(guān)注
42文章
3012瀏覽量
71204
原文標(biāo)題:【干貨】SMT基礎(chǔ)知識培訓(xùn)教材(2022精華版),你值得擁有!
文章出處:【微信號:SMT頂級人脈圈,微信公眾號:SMT頂級人脈圈】歡迎添加關(guān)注!文章轉(zhuǎn)載請注明出處。
發(fā)布評論請先 登錄
電子元器件及手工焊接
直播回顧 | 核心協(xié)議精講!TSN基礎(chǔ)知識理論培訓(xùn),虹科帶你劃重點!
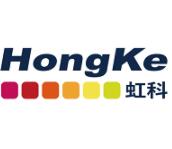
功率器件熱設(shè)計基礎(chǔ)知識
華為-射頻基礎(chǔ)知識培訓(xùn)
TWL6030氣體監(jiān)測基礎(chǔ)知識
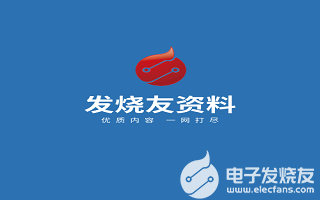
Verilog HDL的基礎(chǔ)知識
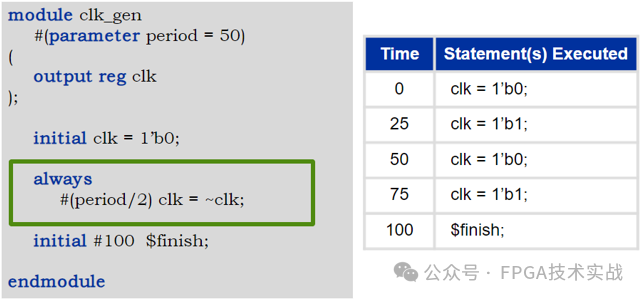
負(fù)載開關(guān)基礎(chǔ)知識
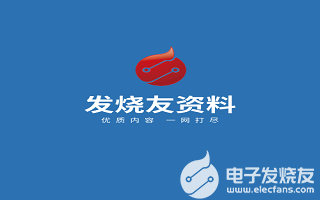
全新的半導(dǎo)體基礎(chǔ)知識
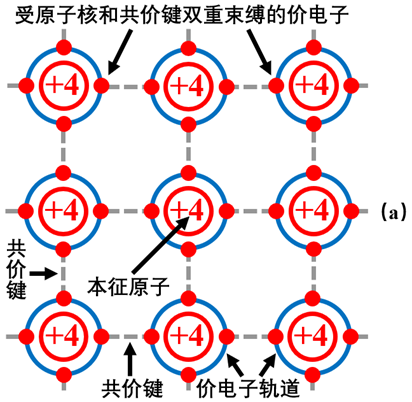
評論