在工業生產和機械設計中,電機作為動力源的核心部件,其輸出方式的選擇直接影響整個系統的性能表現。關于電機帶負載時采用直接軸連接還是齒輪傳動更有利于輸出力或力矩的問題,需要從傳動原理、機械特性、應用場景等多個維度進行綜合分析。
從物理原理來看,直接軸連接實現了電機與負載的剛性耦合,其最大優勢在于能量傳遞的高效性。當電機通過聯軸器或法蘭直接驅動負載時,理論上可達到接近100%的傳動效率(實際約為95%-98%),這意味著幾乎所有的電機輸出功率都能轉化為負載的機械功。這種連接方式特別適合需要高轉速、低扭矩的應用場景,如離心泵、風扇等流體機械。但直接連接的致命缺陷在于"硬碰硬"的特性——負載的任何波動都會直接反饋到電機轉子,這不僅可能引起電機過載,還會導致整個傳動系統承受巨大的機械應力。某機床制造商的技術報告顯示,在未使用減速裝置的情況下,直接連接的伺服電機在切削突變時電流波動幅度可達額定值的300%,嚴重影響電機壽命。
齒輪傳動則通過機械杠桿原理改變了力的傳遞特性。根據齒輪減速比公式(i=Z2/Z1,其中Z為齒數),當采用減速齒輪箱時,輸出轉速降低的同時扭矩會呈比例放大。例如3K行星減速機技術資料顯示,其三級減速裝置可將扭矩提升至輸入值的125倍,而轉速相應降低為1/125。這種特性使齒輪傳動在起重機、輸送機等需要大啟動扭矩的設備中具有不可替代的優勢。但齒輪傳動也不可避免地存在效率損失,普通圓柱齒輪傳動效率約為90-98%,蝸輪蝸桿傳動則可能低至60-80%,這意味著部分電機功率會轉化為齒輪嚙合面的熱量損耗。
從動態響應特性分析,直接軸連接系統具有更優的瞬態性能。由于省去了中間傳動環節,系統的轉動慣量顯著降低,這使得數控機床等高精度設備能實現毫秒級的響應速度。某半導體設備制造商的測試數據顯示,直驅式直線電機相較齒輪傳動定位時間縮短了40%,重復定位精度提高至±0.1μm。而齒輪傳動由于存在齒隙(Backlash),在頻繁啟停或換向時會產生明顯的滯后現象。現代精密減速機雖通過預緊結構將齒隙控制在1弧分以內,但仍無法完全消除這一固有缺陷。
在系統可靠性方面,兩種方式各有千秋。直接連接結構簡單、故障點少,但電機軸承需要承受全部負載力矩。某造紙機械的故障統計表明,直連式傳動中電機軸承損壞占總故障的65%。齒輪傳動雖然分擔了電機負荷,但齒輪磨損、潤滑失效等問題也不容忽視。重載齒輪箱的維護手冊顯示,齒面點蝕和斷齒占齒輪故障的78%,且隨著使用時間增長,傳動效率會以每年0.5%-1%的速度遞減。
從能效經濟性角度考量,選擇傳動方式需要綜合計算全生命周期成本。直接連接雖然初始投資低,但在大負載場合需要選用更大功率的電機,導致電力消耗顯著增加。某物流分揀系統的能效評估報告指出,改用精密減速機后,電機功率從7.5kW降至3kW,年節電達2.1萬度。而齒輪傳動雖然節省了電機容量,但高精度減速器的購置成本和定期更換潤滑油的維護成本也需要納入計算。
現代工業實踐中,兩種傳動方式的界限正在模糊。磁齒輪、諧波減速器等新型傳動裝置的出現,結合了直驅的高效和齒輪變速的優勢。某工業機器人制造商的技術白皮書披露,采用磁齒輪耦合的關節模組既實現了10:1的減速比,又保持了95%以上的傳動效率,同時徹底消除了機械磨損問題。這種融合創新或許代表著未來傳動技術的發展方向。
綜上所述,電機輸出方式的選擇不存在絕對優劣,而應該基于具體應用需求進行系統設計。當追求動態響應和傳動效率時,直接軸連接更具優勢;而在需要放大扭矩、降低轉速的場合,齒輪傳動仍是不可替代的解決方案。工程師需要綜合考慮負載特性、工作制式、精度要求、維護條件等多重因素,有時甚至需要采用混合傳動方案來達到最優的系統性能。隨著新材料和智能控制技術的發展,傳統傳動方式正在經歷革命性的變革,這為機械系統設計提供了更廣闊的可能性空間。
審核編輯 黃宇
-
負載
+關注
關注
2文章
619瀏覽量
35285 -
電機
+關注
關注
143文章
9318瀏覽量
149735
發布評論請先 登錄
嵌入式力矩電機的設計方法研究
伺服電機編碼器與轉子磁極相位對齊方法
直流力矩電動機性能特點詳解
MCSDK5.4.4 FOC電流閉環運行電機偶發停轉的原因?
用PWM控制SCR,調節負載輸出電壓的實驗中,斬波后的負載電壓波形偏離0V-x軸100v是怎么回事?
減速機的工作原理具體是如何實現的?
伺服電機編碼器與轉子磁極相位對齊方法
交流PLC能否直接帶負載的探討
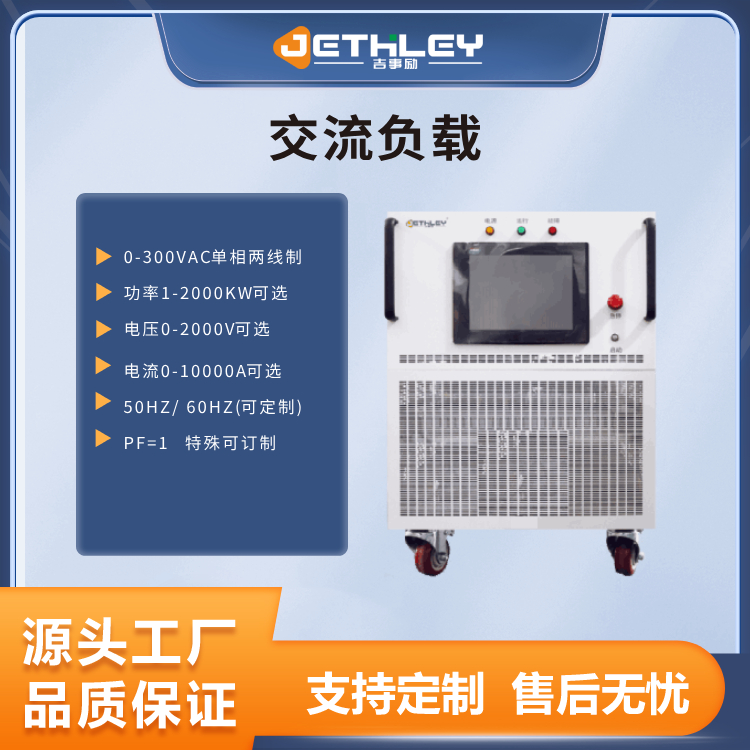
評論