在工業自動化領域,線性模組作為精密傳動系統的核心部件,其加減速時間的設定直接影響設備性能與壽命。通過對運動控制原理的深入分析可以發現,加減速時間的限定是機械結構強度、電機特性、運動精度、能耗管理等多重因素綜合博弈的結果。
一、機械系統承受能力的物理限制
線性模組的機械結構對加速度存在剛性約束。以絲杠傳動模組為例,當加速度超過3m/s2時,滾珠絲杠副的接觸應力會急劇增加。實驗數據表明,加速度每提升0.5m/s2,滾珠與軌道間的赫茲接觸應力將增加約15%,長期運行可能導致軌道表面出現剝落。同步帶傳動模組同樣面臨類似問題,過大的加速度會使皮帶齒形產生彈性變形,當變形量超過齒距的2%時就會引發跳齒現象。機械部件的固有頻率也是關鍵因素,當加減速時間過短導致激勵頻率接近系統固有頻率時,會產生共振現象。某品牌直線電機模組的測試報告顯示,當加速度時間小于50ms時,模組振動幅度會驟增300%,嚴重影響定位精度。
伺服電機的轉矩-轉速特性曲線決定了其動態響應能力。在加速階段,電機需要提供超過穩態轉矩數倍的峰值轉矩。某400W伺服電機在0.2秒內加速至3000rpm時,瞬時電流可達額定值的5倍,這要求驅動器必須具備足夠的過載能力。永磁同步電機的退磁曲線顯示,當繞組溫度超過130℃時,每升高10℃磁鋼的磁通密度會衰減0.5%,過短的加減速時間導致的持續大電流會使電機面臨不可逆退磁風險。步進電機系統更易受此影響,過快的加速會導致轉矩不足而失步,某42步進電機的實測數據顯示,當加速時間小于100ms時,失步概率會從1%飆升至25%。
三、運動控制精度的技術要求
精密定位場景對加減速曲線有嚴苛要求。在S型加減速算法中,加加速度(Jerk)的限定值直接影響運動平穩性。半導體設備常用的0.1μm級模組通常將Jerk控制在5000mm/s3以內,若加速時間縮短50%,引起的振動誤差會擴大8倍。輪廓控制場景下,多軸聯動的同步誤差與加減速時間直接相關。某五軸加工中心的測試表明,當各軸加速時間差異超過20ms時,空間軌跡誤差會達到15μm,遠超精密加工要求的5μm閾值。
四、能量管理與熱平衡考量
頻繁啟停的工況下,加減速時間設定直接影響系統能效。動能公式E=1/2mv2顯示,相同速度下縮短加速時間意味著功率需求呈平方關系增長。某汽車焊接生產線實測數據顯示,將加速時間從0.5秒壓縮至0.3秒,雖然節拍時間減少8%,但能耗卻增加40%。再生制動過程同樣需要合理的時間分配,當減速時間小于驅動器電容放電常數時,80%的制動能量將轉化為熱量。某品牌驅動器的熱成像圖顯示,連續短時間制動會使IGBT模塊溫度在10分鐘內上升至警戒值。
五、安全標準與壽命預測
ISO 13849標準對工業設備的啟停沖擊有明確規定:人體可接觸的模組其加速度不得超過2.5m/s2。在協作機器人應用場景中,過短的加減速時間會導致碰撞力超標,某六軸協作機器人的測試報告指出,當加速時間小于0.15秒時,末端沖擊力會突破150N的安全閾值。軸承的L10壽命計算模型表明,載荷波動幅度增加20%,預期壽命將縮短30%。某線性導軌的加速壽命試驗證實,采用0.1秒加速比0.3秒加速的樣本,在相同循環次數下磨損量增加2.7倍。
六、不同應用場景的參數優化
3C行業的高速貼裝設備通常采用50-100ms的加速時間,配合運動控制器的前瞻算法實現0.02mm的重復定位精度。而機床行業的重載模組則需要300-500ms的加速時間,以確保在移動數百公斤負載時的穩定性。新興的磁懸浮模組通過無接觸傳動特性,可將加速時間壓縮至傳統模組的1/10,但相應的控制復雜度呈指數級上升。
線性模組加減速時間的設定本質上是系統級優化的過程,需要結合具體工藝要求,在機械極限、控制精度、能效比等維度尋找最佳平衡點。隨著材料科學和控制算法的發展,新型直線電機模組已實現μs級的加速度調節精度,這為突破傳統加減速限制提供了新的技術路徑。未來通過數字孿生技術的實時仿真,有望實現動態自適應的加減速策略,進一步釋放線性模組的性能潛力。
審核編輯 黃宇
-
電機
+關注
關注
143文章
9236瀏覽量
148203 -
伺服電機
+關注
關注
87文章
2099瀏覽量
59094
發布評論請先 登錄
如何避免變頻器受負載沖擊?
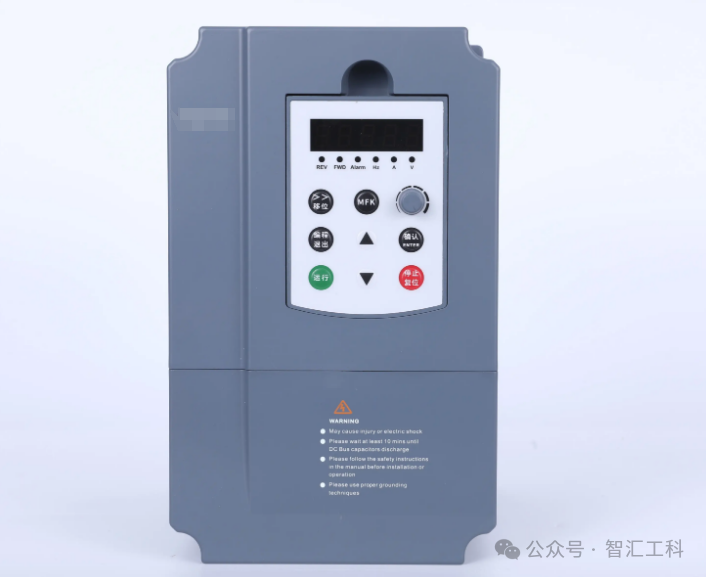
變頻器控制電機需要設置哪些參數
減速機的工作原理具體是如何實現的?
諧波減速器工作原理 諧波減速器與齒輪減速器的區別
諧波減速器選型的常見誤區
減速電機概述了解多少?
線性模組在哪些情況下需要進行定期維護?
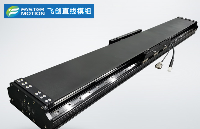
評論