大多數電子設備必須必須承受沖擊和保持對工作的外殼。您的機箱在三架飛機中能承受重擊嗎?它會變形而在極端的溫度?是電子設備的內部冷卻系統經過深思熟慮?有兩種方法來回答這些問題。首先:在現實生活中測試完成的設備(原型),并根據結果將其發送以進行修訂。第二:模擬物理過程并糾正開發過程中的問題。這樣可以更快,更高效,因此您可以在第一次迭代時就已經擁有可以工作的原型。機械設計工程師Promwad不得不嘗試這兩個選項。檢查機箱的安全性讓我們先從內置到汽車內部的設備發送緊急信號(圖1)。根據職權范圍,必須使用彈簧鎖將其固定。禁止使用螺絲。
圖1.汽車內部(前側)的緊急信號裝置必須僅用塑料卡扣固定在適當的位置。
我們決定以模擬車輛與障礙物碰撞。我們的目標是保持設備工作在意外發生后,保護乘客(他們不想受傷,因為設備的安裝跌出)。圖2 顯示了如何在汽車的儀表盤內部的設備外觀。
圖2.緊急傳輸設備的模擬外殼使用夾子將其固定在儀表板上。
碰撞會發生什么?我們知道我們需要一個相當強大的坐騎。仿真幫助我們計算了強度,并讓我們測試了設計。我們計算的夾緊力兩個條件的鎖存器:插入設備到汽車的內飾面板和碰撞圖3和圖4 使用動畫顯示在不同角度捕捉過程。實際上,捕捉過程會有所不同,但是在建模過程中,希望在合理的范圍內盡可能簡化任務。最主要的是,以占鎖預加載。
圖3.捕捉過程的模擬,以獲得外殼到位。
從圖3中的動畫中,您可以看到閂鎖首先穿過零件。這一招可以和簡化任務的時候應該做的。在我們的計算中,稍后將包括接觸部分。圖4 示出了夾具的模擬側面圖。
圖4.捕捉過程的模擬顯示了從側面看時夾子的彎曲。
發生事故時變送器會發生什么情況?下一步是汽車與障礙物碰撞過程的模擬,占鎖存器的預載荷,即我們的第一個計算轉移到第二計算。在圖5中 的動畫可以讓你看到設備在模擬碰撞。
圖5.模擬的碰撞顯示了設備與儀表板的偏離。
模擬諸如這些可以讓你看一個產品在一個完全不同的方式。注意到如何在結構上形成的杠桿。在這個項目上,一切準備就緒,可以生產原型。最后期限收緊。誰也沒有料到這樣的結果。根據仿真結果,我們按時暫停了原型的生產。它減少了一次迭代,為客戶節省了資金。我們提出的設計變更,從而減少從儀表盤上的新組件的選擇造成的設備的離開。我們還調整了裝置的下部的安裝。
在這個項目上建模另一個例子是用于在塑料鑄件(注射成型)的缺陷的計算。這樣的計算使我們選擇了最好的材料,并使細節在技術上更加先進。其結果是,我們的產品在批量生產開始后收到的可能水槽插件的報告。計算也被用于殘余應力鑄造補償期間進行。此類缺陷通常是由于鑄件冷卻不均勻而產生的,并取決于產品的材料。隨著時間的流逝,它們會導致出現裂紋和外殼完全損壞。如果您看著塑料產品開始破裂,則可能會遇到這種現象。鑄造缺陷現在,讓我們到下一個項目的舉動。圖6
顯示了一個連續生產的塑料外殼元件。
圖6.在這一部分,模擬揭示了塑料內產生缺陷。
圖7 示出了建模從鑄件中不從產品的前側看到的問題的結果。
圖7.模擬顯示了塑料內部發生的問題。
盡管缺陷發生在塑料內部,但客戶仍必須意識到這些缺陷。你可能已經注意到,知名品牌不允許在自己的產品這樣的問題。正如你所看到的,仿真結果不相符的100%的現實,但整體情況仍然相似。在批量生產中,一個鑄件可能與另一個鑄件不同,這是正常現象。
某些產品可能由于制造商的故障而有缺陷。借助計算機輔助工程(CAE)系統,您可以向制造商傳達建議,并減少零件的迭代次數。這正是我們在該項目中所做的。結果,在短時間內解決了該問題。然后,該產品開始批量生產,沒有明顯的缺陷,不僅從外部而且從內部也沒有。圖8 中的動畫顯示了另一種產品的填充。該計算考慮了澆口系統,模具的冷卻系統以及模具本身。
圖8.動畫顯示了成型零件中塑料的流動。
圖9中的紅色 突出顯示了鑄造缺陷。
圖9.仿真中的紅色區域表示模具中的缺陷。
該缺陷在圖10中清晰可見。
圖10.您可以在這張照片中看到缺陷。
碰撞測試
強度測試是平板電腦和智能手機評論中的熱門話題。通常,論壇參與者會討論設備在意外跌落后是否會運行。在Promwad,我們還在消費類電子產品的開發中進行了此類測試。以藍牙智能網關為例(圖11)。
圖11.藍牙智能網關的外殼上有用于USB和LAN的開口。
當從1.2 m的高度掉落時,設備必須保持其原始狀態,這是客戶的要求之一。在技術任務中,指出了設備可能損壞的可能問題點。我們進行了七次計算,并收到了積極的結果。圖12 顯示了其中一個計算結果:
圖12.此動畫顯示了外殼如何響應1.2米的跌落。
進行原型制作后,我們測試了該設備在現實生活中的跌落情況。結果再次是積極的。請記住,通過物理特性銑削的原型與通過鑄造方法生產的標準情況略有不同。銑削時,產品中會殘留殘余應力。但是,在這種情況下,最好在進行強制轉換之前進行測試。在對獲得的原型進行分析之后,我們決定通過在設計中添加肋來稍微加強外殼(圖13)。對將手指按在外殼上的效果進行建模后,設備的剛度應該增加了約30%。
圖13.在機柜的設計中增加了肋條,從而增強了它的強度。
然后,我們訂購了新的原型。在測試了抗跌落能力之后,該器件仍然開始崩潰,沒有人期望到這一點(圖14)。
圖14.在測試期間,原型中出現了意外裂紋。
我們決定重新模擬并將結果與實際進行比較。實際上,該程序顯示了這個新問題(圖15)。
圖15.模型顯示了模具中的薄弱點。
我們去除了單個肋骨。在下一次模擬之后,我們獲得了積極的結果。
對設計進行任何更改,都必須對物理過程進行重復的計算和計算機建模,這將節省開發電子產品外殼的時間和金錢。最好在工程分析系統中而不是在現實生活中檢查外殼的強度。
Maxim Kendys是Promwad Electronic Design Company的機械設計工程師。
編輯:hfy
-
電子設備
+關注
關注
2文章
2882瀏覽量
54748 -
機械設計
+關注
關注
7文章
169瀏覽量
19831
發布評論請先 登錄
TG-5510CB溫度補償晶振高端電子設備的理想時鐘源
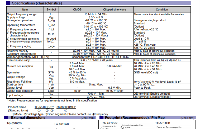
奧德賽Odyssey電池PC925極端天氣下維護方法
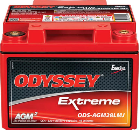
評論